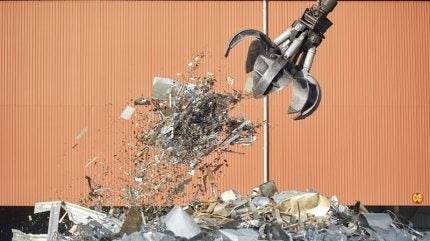
Sweden has long been a pioneer in the world for integrating sustainability into business. In fact, the Swedish government has set ambitious climate targets to become the first fossil-free welfare country with net-zero emissions by 2045. In this context of broad societal commitment to clean economic growth, Sweden’s steel producers have also long embraced environmental stewardship in their operations and as steelmaking is one of the biggest emitters of CO2 globally, this is positive news for manufacturers and the construction industry.
One leading Swedish producer of advanced stainless steels and special alloys is Alleima.
Headquartered in Sandviken, Alleima’s offering includes products like seamless steel tubes for the energy, chemical and aerospace industry, precision strip steel for white goods compressors, air conditioners and knife applications, based on more than 900 active alloy recipes. It also produces ultra-fine wires for medical and micro-electronic devices, industrial electric heating technology and coated strip steel for fuel cells technology for cars, trucks, and hydrogen production.
Mikael Silver, head of sustainability for Alleima’s strip steel division, opens up about the company’s commitment to circularity, sustainability, and how, as a result of its investments and activities, it is supporting its clients become more sustainable while boosting product quality.
Low-fossil steel
Swedish steel companies work vigorously to reduce their CO2 emissions. Ambitious work to shift the remaining blast furnaces using fossil coke to reduce iron ore to fossil free reduction and increased use of recycled steel is underway. Alleima started using recycled steel in 1921. Advanced manufacturing technologies, such as recycled steel based electric arc furnaces (EAF) in combination with continuous casting and sequential hot rolling result in energy and emissions savings. For energy intensive processes, the attention to efficiency is vitally important.
“We use a lot of energy in our production processes, particularly in melting raw materials and heating operations” Silver explains. “After melting, the steel is continuously casted, the castings are heated before hot rolling and the steel must be reheated before cold rolling into strip products. The thinner the product is the more heating operations are required. The applied manufacturing technology in our fully integrated steel plant at Alleima enables us to significantly reduce heating operations in primary processes and therewith reduce the consumption of electricity or gas.”
He explains that one advantage of being located in Sweden is the access to fossil-free electricity. The entire nation relies heavily on fossil-free electricity and globally Alleima uses 96% fossil-free electricity. Many of Alleima’s furnaces are electrically heated, but for those that are still powered by gas we have increased the use of biogas.
“We purchase a significant share of biogas, produced from biomaterials, which helps reduce our fossil CO2 emissions,” Silver adds. “We also take measures to reduce our CO2 impact in other processes, such as using biodiesel (HVO) for diesel-powered vehicles on-site in Sandviken and we are extending the use of heat recovery from our processes for facility heating.”
Steel recycling and waste management
Recycling is integral to Alleima’s steel production. Scrap steel is a primary raw material, reducing the need for virgin materials and the associated environmental impact. Efficient waste management systems ensure minimal industrial waste, with by-products being repurposed.
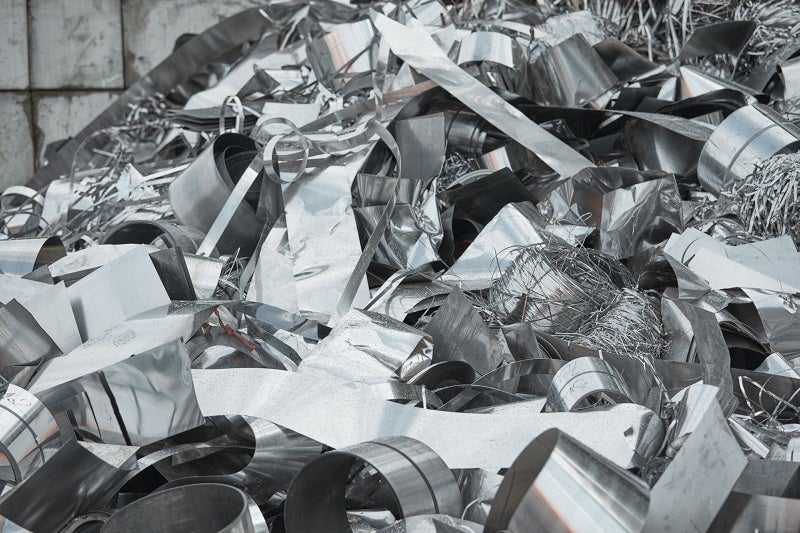
According to Silver: “By using recycled materials, we significantly cut CO2 emissions associated with raw materials. On average, 80% of our raw materials are recycled, but we still need to use about 20% virgin material from mines, such as chromium and nickel, which are CO2-intensive. The industry average for chromium producer is emissions of 10 tonnes of CO2 per ton chromium. We use suppliers with lower CO2 emissions for these materials. Our main Ferro chromium supplier for strip products just emits 3,3 tons of CO2 per ton chromium. We are also extending our buyback program of steel leftovers from our customers. By knowing the exact chemical composition of the raw material, we can use more recycled steel in our heats.”
Alleima gradually implements a Life Cycle Assessment (LCA) model, which is independently reviewed by IVL Swedish Environmental Research Institute to ensure data accuracy. This ensures that customers have reliable information about the carbon footprint of Alleima steel, including the raw materials used.
Improving fatigue strength for sustainable steel
Sweden’s stringent environmental regulations ensure that steel manufacturers adhere to high standards of sustainability. These regulations promote cleaner production methods and the reduction of greenhouse gas emissions, fostering a culture of accountability and continuous improvement.
“The demand is increasing. So far there are proactive prominent customers delivering their products directly to consumers that are eager to reduce the CO2 emissions. What’s holding other business back from using sustainable steel? It’s mainly the availability of sustainability performance information for consumers, and political measures,” Silver explains. “Within the EU, the Emission Trading Scheme (ETS) requires companies with high fossil CO2 emissions to buy emission rights, making production with fossil fuels more expensive thus encouraging the use of non-fossil fuels. While emission rights are often still the cheapest option, at Alleima, we choose to pay more for the use of non-fossil fuels than it would cost to buy more emission rights. Political directives and consumer willingness to pay a premium for sustainable products are critical. We have noticed that customers are increasingly willing, and choosing, to pay a premium for better climate, product quality, and greater longevity.
Durable steel components require less frequent replacement, reducing the need for new raw materials and energy-intensive manufacturing processes. This longevity not only conserves resources but also minimises waste and the environmental impact associated with steel production.
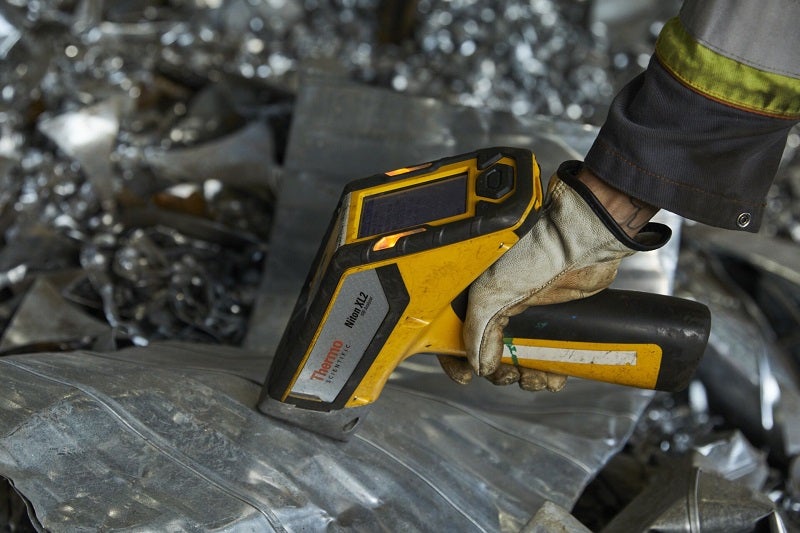
Wear, corrosion- and fatigue resistance are key attributes of Alleima steel. Elements such as chromium, nickel, and molybdenum are integral to enhancing the corrosion resistance, hardness and toughness of the steel, assuring functional properties over time. Additionally, Alleima employs advanced heat treatment processes that optimise the steel’s microstructure, further improving its ability to resist wear and exposure in challenging environments. By refining the grain structure and eliminating impurities, the steel’s fatigue strength is improved, which helps in preventing the initiation and propagation of cracks. In certain applications, mainly within the green hydrogen eco-system, Alleima also utilises tailor made surface coatings to enhance functionality and durability of its products and is thus facilitating the market development of a sustainable energy system.
The future of sustainable steel
Alleima has committed to the Science Based Targets initiative (SBTi), a global body enabling businesses to set ambitious emissions reduction targets in line with the latest climate science.
According to Silver: “We’re working on short and long-term plans to meet our CO2 reduction goals by 2030 and reach net zero by 2050. The short-term goal is to reduce the scope 1 and 2 emissions by 50% compared to 2019. By 2023 we had achieved 35% of those. One major initiative is replacing the remaining fossil gas in our heat treatment processes. The preferred solution is to switch to electric heating, though some heating operations may require biogas or hydrogen if electric heating proves infeasible.
“This hydrogen should be green, produced from a non-fossil raw material using fossil-free electricity.”
As a company dedicated to sustainability and continuous improvement, Alleima is the ideal partner to meet your steel component needs. Find out more about Alleima’s durable and sustainable steel in the free whitepaper below.