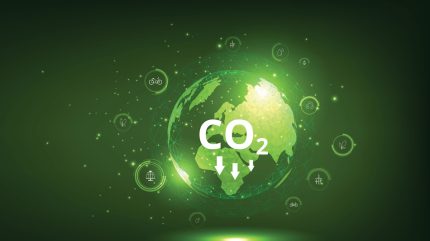
The demand for batteries continues to grow as the world transitions towards a lower carbon energy system.
Although batteries are essential for a sustainable future, the materials used in their production often come with a significant carbon footprint.1
Following article two focusing on the ‘negatives’: addressing the environmental impact of anodes, we shift our attention to the ‘positives’, and the critical challenge: how can we decarbonise cathode material production?
Cathode Types: NMC and LFP
Two main families of cathode materials dominate the battery industry: high-nickel variants such as nickel manganese cobalt (NMC) and lithium iron phosphate (LFP). “Each of these materials has distinct characteristics and applications,” starts Greg Pitt, Vice President, Battery Materials at Worley.
NMC cathodes are widely used in electric vehicles (EVs) due to their high energy density and long cycle life. However, the mining and refining of nickel and cobalt, in particular, have significant environmental and social impacts.
LFP cathodes are increasingly favoured in applications where safety, cost, and longevity are prioritised over energy density. LFP’s reliance on iron and phosphate, which are more abundant and less environmentally damaging to mine, gives it an edge in sustainability.
Factors contributing to the carbon footprint of cathode materials
The carbon footprint and environmental, social, and governance (ESG) impact of cathode materials are influenced by several factors:
- Energy mix and consumption: Converting raw materials into battery-grade feedstocks and then cathode materials is energy-intensive and a source of CO2 emissions, especially with regard to their thermal treatment process steps. If the energy mix isn’t fully renewable, this process contributes significantly to emissions.
- Waste streams: Some are hazardous and require careful management, while others are voluminous in solution and require significant energy to crystalise and dry for disposal.
- Water use: Water is essential in the production processes, but its consumption can strain local resources, especially in water-scarce regions.
- Plant efficiencies: The overall efficiency of manufacturing plants, including energy use, waste management, and resource utilisation, plays a critical role in determining the environmental impact per kilogram of material produced.
So, what options can cathode producers consider to reduce the carbon footprint of their materials?
Nine strategies for decarbonising cathode materials
“If it were as simple as adopting a single approach, we would have done it by now,” says Pitt. “The reality is that to meaningfully address the carbon footprint of cathode materials requires a multifaceted strategy.”
These strategies can include:
- Adopt newer processing technologies
Ongoing research into more efficient or more sustainable processing technologies offers numerous opportunities for plant design improvements. “Some technologies impact discrete processing steps, whilst others involve a holistic end-to-end process change,” says Pitt.
“For example, companies such as Canadian-based Nano One are making strides in scaling new cathode materials processes that are more efficient, consume less energy and produce less waste, and can be deployed in smaller, more flexible plants.”
Nano One has devised a simplified method – the One-Pot process – of producing cathodes without producing sulphate waste. The process combines all the materials required for a cathode in one step with significantly reduced energy and water consumption – as opposed to multi-phase production.
The One-Pot process is compatible with both NMC and LFP cathode production. And the environmental savings can be considerable – cutting an estimated 60% of emissions for the NMC cathode and 50% for LFP.2 The method also delivers an 80% reduction in water consumption. “Our estimates show that the process is commercially viable, enabling our customers to be competitive in the marketplace,” says Pitt.
- Flexible plant design:
Given the ongoing technological advancements in this rapidly evolving industry, it’s essential to design plants that can be easily upgraded to incorporate new technologies as they become available.
“We’re developing flexible plant designs that can adapt to technological advancements and market changes over time,” says Pitt. “The concept focuses on a high degree of modularity and scalability, standardised footprints and careful thought into lifting and craneage.”
This allows for easier upgrades, expansions, and the integration of new processes or technologies without requiring extensive reengineering. “It’s a change in mindset away from bespoke optimisation of each facility to a future-proofed, manufacturing style mindset to replicate designs in building blocks,” says Pitt.
- Optimise startup, ramp-up and plant availability:
“We often see project concepts that overlook the impacts of start-up and shutdown activities for an operating facility,” says Pitt. “Too often designs are developed for an ideal steady state, without due consideration to the reality of operating long process trains with a mixture of continuous and batch unit operations.”
It can take eight to 24 hours to ramp up after a shutdown or production pause, during which time any off-spec materials need to be stored, and then either discarded or recycled.
“Careful management of these operating conditions can enhance overall throughput and efficiency, reducing the environmental impact per kilogram of cathode material produced,” says Pitt.
“For instance, incorporating buffer tanks or intermediate storage can improve plant uptime and prevent production halts due to issues like full overflow tanks or equipment stoppages. Though these additions may increase capital costs in the short term, their efficiency benefits per kilogram of product usually outweigh the expense.”
- Collaborate with equipment suppliers:
“By improving collaboration across the vendor ecosystem, we can identify incremental improvements and innovations for major equipment like kilns, dryers, and reactors. This can lead to better ESG outcomes,” says Pitt.
Enhancements such as improved heat recovery, lower energy consumption, and reduced use of saggers – the disposable crucibles used in certain types of kilns – can make a substantial difference to each kilogram of material produced.
“As always, there is a trade-off between the ability of newer, more advanced equipment to perform to specification, reduce the environmental impact and do so in a cost-competitive manner.”
- Diversify the energy mix:
Shifting from carbon-intensive electricity to alternative energy sources – or choosing locations with abundant and resilient renewable energy – can reduce the carbon footprint of cathode production.
“Sweden, Norway and Quebec are known for their abundant hydropower resources, which provide a stable, low carbon electricity supply,” says Pitt. “Establishing battery material plants in these areas can significantly reduce the carbon footprint associated with electricity consumption.”
In addition, Morocco is rapidly expanding its renewable energy capacity, particularly in solar, wind power and battery energy storage. With its ambitious plans for renewable energy, Morocco offers a promising location for plants looking to minimise their carbon footprint while benefiting from the country’s growing renewable energy infrastructure.
- Leverage economies of scale:
As battery material plants are scaled up, there’s an opportunity to incorporate more efficient processes and circularity loops that wouldn’t have been practical for smaller facilities.
“We recently assisted a customer who initially planned to import high-purity oxygen in cylinders, which would have required an extensive logistics exercise,” says Pitt. “Instead, we demonstrated that purifying oxygen on-site, even at slightly lower purity, provided cost benefits, reduced environmental impacts, and improved operational resilience.”
This is just one of many efficiency opportunities that are possible with large-scale facilities, though they are often overlooked because they may not be central to the primary processing steps. The advantages of this approach demonstrate that scaling up production can lead to innovations that boost efficiency and reduce emissions, supporting sustainability goals.
- Implement recycling and recovery loops:
In addition to recycling of off-spec product, introducing recovery and recirculation systems for heat, water, and off-gases can greatly reduce resource consumption and enhance sustainability in battery material plants.
Water recovery systems allow for reuse in the production process, minimising overall freshwater requirements, thereby conserving local resources.
“We have designed systems that use rooftop rainwater collection to augment the facility’s water needs and reduce dependence on local sources,” says Pitt. “In other instances, we’ve installed Zero Liquid Discharge (ZLD) systems to ensure that no liquid waste is discharged from the plant.
“We have also developed systems that optimise gas usage to enable more efficient consumption,” continues Pitt. “For example, we have modified the way nitrogen is used to minimise ammonia lost to the scrubber”
- Explore synergistic co-location:
Co-locating plants with adjacent industries allows for the utilisation or valorisation of byproducts. For instance, sulphate byproducts can be upcycled into fertilisers or detergents, while alumina silicate byproducts can supply the cement industry.
“Cinis Fertilisers’ business model is to transform a sodium sulphate waste stream into fertilisers,” says Pitt. “This process alleviates waste disposal costs for the materials producers, generates a new revenue stream for an adjacent industry and overall lessens the environmental impact of material processing.”
“RockTech is adopting a similar strategy by investigating the use of byproducts from its lithium production processes. Their business plan includes repurposing alumina-silicate residues—typically regarded as waste—as additives in the construction industry, especially in cement production. This approach not only diverts waste from landfills but also offers an alternative to conventional cement additives, thereby reducing the carbon footprint of cement manufacturing.”
- Rethink plant infrastructure:
For battery materials plants, assessing the heating and cooling needs of each area is key to optimising energy use and reducing carbon footprint.
“By evaluating temperature requirements, plants can avoid unnecessary energy use to heat or cool large volumes,” Pitt explains. “Some areas may not need extensive climate control, allowing for the removal of excess systems. Physical partitions within buildings can improve climate control efficiency, and in some cases, process equipment may not need a building, eliminating the need for heating or cooling altogether.”
Incorporating energy-efficient insulation, using passive design strategies to naturally regulate temperature, and implementing advanced climate control technologies only where needed can further enhance efficiency.
A journey of incremental improvements
Decarbonising cathode materials is a complex challenge with no single solution. While innovations like those from Nano One offer promising advances, the industry cannot afford to wait for a single breakthrough to solve the problem entirely.
The path to sustainability is a long one, composed of numerous small steps and incremental improvements. By tackling the most significant challenges first and continuously chipping away at emissions, the industry can make meaningful progress in reducing its carbon footprint and improving its ESG outcomes.
“To quote Tzu: ‘The journey of a thousand miles begins with a single step.’ With persistence, the cumulative impact of these steps will be significant across the industry,” concludes Pitt.
Missed Part 1 and 2? Read Part 1 here. Read Part 2 here. Coming soon: Part 4 of five – Focusing on the ‘positives’: Addressing the environmental impact of cathodes.
References:
1 https://www.minviro.com/resources/guides
2 https://nanoone.ca/technology