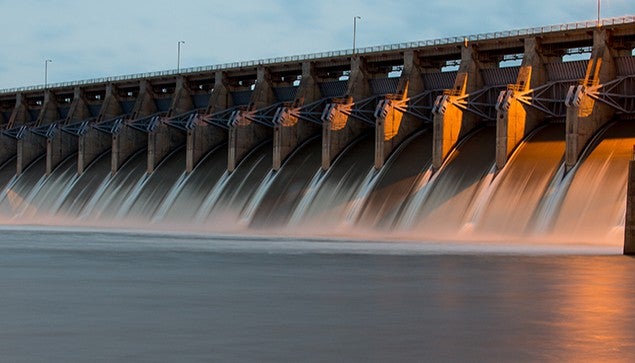
When a US-based engineering solutions provider needed urgent support to help in the rotor refurbishment of a pair of large hydro-generators at a pumped-storage underground power station, it turned to TS Metals, part of the Quartzelec group of companies, to engineer, laser profile and deliver the high specification components it needed.
The refurbishment contract was demanding and required several thousand individually laser-cut laminations to support the rebuild of two stacked ring rotors of hydro-generators that were originally built 50 years ago.
The client was looking for a partner they would work with that could not only precisely manufacture these key components in such large quantities, but more importantly, demonstrate a clear and technical understanding of the complexity of the refurbishment project and the rebuild required to ensure a right-first-time solution.
With a long history in the design and building of rotating electrical machines, Quartzelec looked to leverage this unique heritage to its advantage.
Quartzelec’s international business development and LTSA leader Stephen Densley said: “We had first liaised with the US-based project designers a number of years ago, concerning the possible manufacture and supply of stator coils. Our skills and project knowledge were obviously acknowledged as we were approached to support our customer in carrying out a design review for the refurbishment of these large hydro-generator rotors.
“Having made a strong technical contribution, it was clear that our TS Metals, part of the Quartzelec group of companies, was more than capable of engineering the replacement rotor rim laminations, which were one of the most critical components in this refurbishment.”
TS Metals business unit manager Ian Addison said: “The original laminations would have been produced using bespoke press tooling, which today would incur significant cost and manufacturing timescales to replicate.
“Laser-profiling the laminations not only would reduce the delivery on this project but would allow thicker material to be precision manufactured, offering similar savings in terms of build time for the machine with less individual laminations to stack.”
The total order, worth over $1.8m, is the most significant US order to date that TS Metals have received and is another milestone along their expansion path as they continue to expand and build a respected presence in this market.
Densley added: “TS Metals were chosen for this project because, working alongside the Quartzelec Engineering team, they were able to demonstrate a highly intelligent and collaborative design and manufacture process, incorporating stringent quality checks and achieving the exacting tolerances that were essential to the success of the build of these rotor rims.”
Working to exceptionally tight deadlines to ensure the project was delivered on time, TS Metals delivered the first part of the order during a four-month period, completing in February in staggered phase consignments.
Delivering approximately 300t of laminations over several months was planned to allow the customer to manage space at site, which went extremely smoothly.
The laminations are currently being installed in the first generator by the engineering team at the facility and the first generator is expected to return to full service soon, ready to deliver many years of faultless operation. The second machine laminations are just entering the production phase now, with completion expected by November.