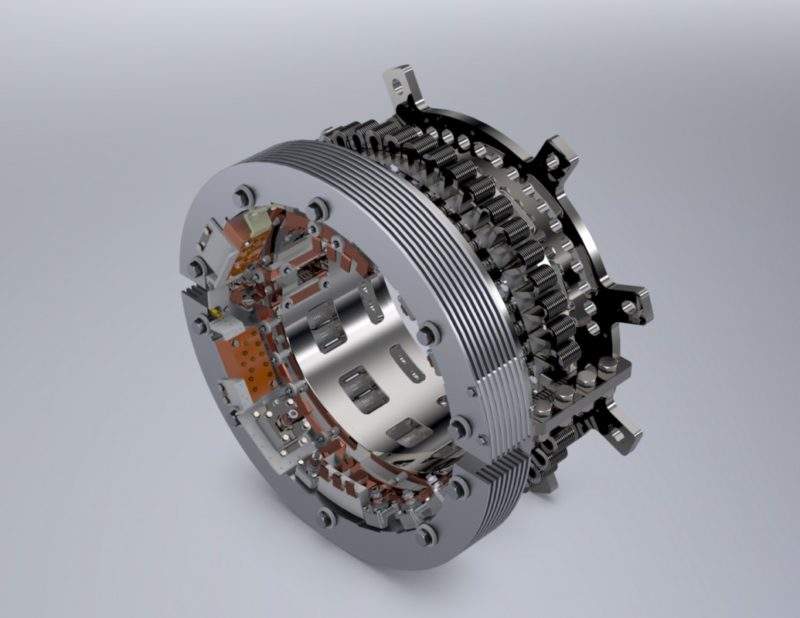
When a utility company based in Saudi Arabia experienced operational problems with the starting hub of a critical synchronous motor drive, the company initially approached the motor OEM for assistance. On learning the existing 35-year old hub was considered ‘obsolete’ they found no support was forthcoming. Seeking a viable alternative, Quartzelec, the independent engineering service provider globally recognised as an expert in rotating electrical machines, was approached to provide technical support.
Working through a third-party engineering sourcing specialist, Quartzelec responded to the request for a solution; but rather than simply looking to fabricate replacements for the hub components that had failed and ‘nursing’ others that were becoming increasingly unreliable, Quartzelec proposed developing and fitting an ‘all-new’ external starting hub – Quartzelec’s Rosenberry Hub; a cost effective solution for synchronous motor starting and often used in machine life extension programmes.
Upon detailed on-site investigation it was discovered that the in-situ vertical motor had no suitable end‑of‑shaft location for a conventional Rosenberry Hub. Unwilling to admit defeat, Quartzelec rose to the challenge of designing and reengineering its original hub design, ultimately developing a totally new solution to fit around the shaft – creating the first ever Split Rosenberry Hub.
The stresses created when starting synchronous motors can cause serious equipment damage but for fixed speed synchronous motors that need to start asynchronously, extra switching devices are installed on the rotor to allow the induced field currents to flow safely without damaging components.
Designed for mid-shaft mounting where there is insufficient space for conventional solutions, the new state-of-the-art electronic Split Rosenberry Hub can either be installed on a new motor or retrofitted to existing machines where components have become obsolete or the existing design is troublesome. This protects and enhances the operation and lifecycle of a host of rotating machine assets. The Rosenberry Hub range complements other Quartzelec branded and marketed products that include fault rated and certified terminal boxes, flexible condition monitoring services, electronic and pneumatic purge solutions; all available with ATEX and IECEx certification.
The replacement process
Within seven weeks of order placement, a full diagnostic check had been completed on the existing machine and a proposal for the new design approved. Over subsequent weeks Quartzelec engineered and tested the new hub before it was air freighted for installation in the utility company’s plant.
The existing starting hub was removed along with all associated rotor-mounted controls, power cabling and resistor elements before being replaced with the new one. Each new Rosenberry Hub is supplied as a complete assembly for ease of installation; also dynamically balanced with a residual mass imbalance of less than two gram-metre. This ensures that the assembly has a neutral balance effect, but in-situ balancing can also be implemented during commissioning, if necessary.
Quartzelec Specialist Products Design Manager Ian Martin said: “Our hub is designed with conservatively rated devices able to withstand high dv/dt with a high current (600A DC) rating; and it does the job perfectly.
“Our design not only improves motor safety and longevity but by reducing oscillating torques, stresses on other motor components are minimised making for a more efficient machine. The design and development order for our client went without a hitch and took just five months from initial contact to final commissioning and again proves our expertise and ability to breathe a new lease of life back into an ageing motor.”
About the Hub and its operation
Based on Rosenberry Hub principles first developed in the 1990s, a typical hub weighs in at around 250Kg and at 400mm in length can be fitted on machines with a rotor diameter up to a maximum of 425mm. Suitable for rotating speeds of up to 1500rpm, it is designed to run for more than one million hours, so should deliver almost faultless operation throughout the life of the machine. The hub is also exceptionally flexible, being conservatively rated at 600A DC and 750V DC (1,500V PIV) and is appropriate for use on the majority of OEM manufactured synchronous motors.
When starting the motor, the stator supply is energised with no excitation being applied to the exciter field. This means the stator current produces a rotating field that induces an alternating voltage in the motor field which in turn forces the motor to accelerate until it reaches synchronous speed. Motor starting torque during run up is improved by a short term rated starting resistor within the rotor circuit which is switched out once the motor is synchronised to minimise losses.
Developed using devices with high dv/dt withstand, all components are easily accessed and have been specifically selected for rotating duties. Many of the standard silicon devices used are readily available to help minimise costs and provide supply chain security. The hub also features the minimum number of connections and wires to improve reliability. Full maintenance and support is also available from Quartzelec for any hub it delivers and full support for any machine can also be incorporated.
Success at Quartzelec
In 2017, Quartzelec celebrated ten-years of OEM independence and 100 years of heritage, building its reputation as a cost-effective provider of electrical engineering services. Key to this was strong leadership, a dedicated and knowledgeable 600 plus workforce and a positive ‘can do’ approach that enabled the business to achieve a £63.4m turnover with continual global growth.
Commenting on this, Quartzelec MD Daniel Laval concluded: “The past ten years has given us the opportunity to flourish and truly establish ourselves as the competent partner of choice for reliable, responsive and cost effective independent support solutions and we are now consolidating plans to grow the business further over the coming decade and beyond.”
Quartzelec designs, manufactures, repairs, refurbishes and rewinds large, project-critical motors and generators with state-of-the-art production facilities, an extensive library of design drawings and a full design department. It also has the ability to work on any OEM‑manufactured machine and/or equipment, including those built by companies such as GEC Machines, GEC Alsthom Large Machines, ALSTOM and Cegelec.