
The US Environmental Protection Agency (EPA) and other environmental and regulatory bodies around the world have begun to police fugitive methane emissions resulting from fuel leakage, unburned methane, and other sources of greenhouse gases (GHG) that don’t originate from the combustion process.
Brian Kromer, Managing Director and Principal, Step2Compliance, said things changed when natural gas was labelled a pollutant in 2016 based on New Source Performance Standards (NSPS) targeting oil and gas operations (NSPS OOOOa). Such rules also being applied to power producers that use natural gas-based turbines or engines. Thus, anywhere along the oil and gas and power generation value chain will have to measure and report on methane leakage and losses such as: gas emitted from oil and gas production sites; the amount of methane lost into the atmosphere due to flaring: seal leakage in pipelines and compressors. They will be forced to measure the amount of methane coming into a facility and compare it to how much is utilised versus how much is lost. They will be required to capture leaked methane and feed it back into the process, or harness it to generate on-site power.
Inflation Reduction Act Ups the Ante
The US Inflation Reduction Act introduced measures to tighten the screws on methane leakage. The amount of permitted methane leakage has been lowered, with penalties enacted of up to $1,500 per ton of excess methane. But monitoring, measuring and dealing with methane leakage is easier said than done, said Rick Fisher, Vice-president at Continental Control Corp (CCC). He noted that methane doesn’t go away when you use a three-way catalyst.
“Every compressor station and any plant running a gas turbine or gas engine is going to suffer methane leakage,” said Fisher. “Even something as simple as shutting off a valve in a compressor station often leads to some venting of methane.”
Even facilities with a good environmental track record are going to find methane measurement and tracking challenging. Fisher believes it will probably require real-time measurement and advanced controls.
“Controls must now be able to accurately calculate GHG emissions as well as the conventional pollutants,” said Kromer. “Facilities must learn to track the amount of methane leakage and find ways to recapture it and put it to use.”
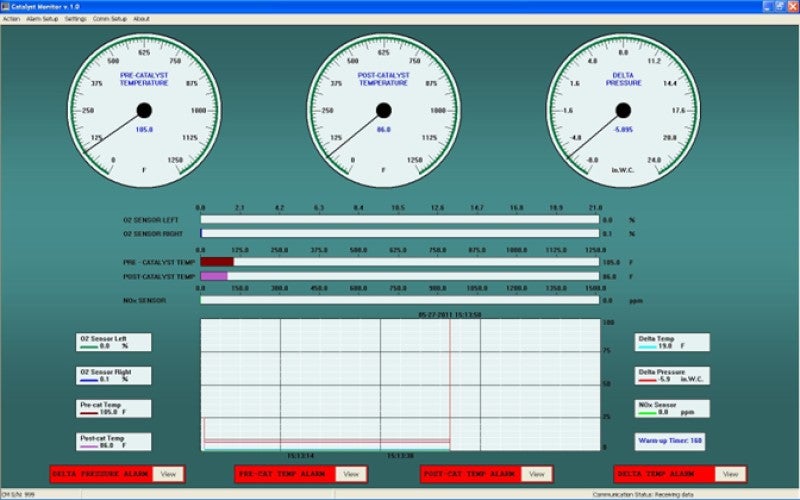
Measuring Methane
The vendor community is beginning to respond to demand. There are a number of products that address the various needs of the methane measurement market. Here are a few examples:
Baker Hughes subsidiary Panametrics offers ultrasonic flare flow meters. They provide flow data and diagnostics for petrochemical plants, refineries, and offshore platforms. This is done by determining the molecular weight and mass flow rate of the flare and sweep gas as a way to reduce product loss by identifying sources of leaks in a flare system and achieve optimal combustion
ABB has released HoverGuard as an addition to its ABB Ability Mobile Gas Leak Detection System. This Unmanned Aerial Vehicle (UAV) detects, quantifies and maps leaks up to 300ft from natural gas distribution and transmission pipelines, gathering lines, storage facilities, and other potential sources. It automatically generates digital reports that summarise results and can be shared in minutes after a survey. Cavity-enhanced laser absorption spectroscopy detects methane with a sensitivity more than 1,000 times higher than conventional leak detection tools.
Teledyne Flir’s FLIR GF320 detects hydrocarbon and volatile organic compound (VOC) emissions from natural gas production and use. With this optical gas imaging camera, inspectors can check components and see potential gas leaks in real-time. The GF320 is lightweight, offers both a viewfinder and LCD monitor, and has direct access to controls. Embedded GPS data helps in identifying the precise location of faults and leaks.
CCC offers a range of fuel control, fuel measurement, and emissions monitoring tools to accurately measure GHGs. Its Catalyst Monitor continuously measures pressure across the catalyst as well as pre- and post-catalyst temperature and notifies the user if minimum or maximum temperatures are exceeded. When combined with CCC Air Fuel Ratio Controls (AFRC), it can make corrections to set points to maintain low emissions levels and extend the useful life of catalysts. This arrangement can be used to provide evidence of engine compliance and fuel consumption over an extended period of time.
Additionally, the CCC FM50 flow meter records individual flow to an engine or to an enclosed combustor at a point in time or total flow over a period of hours, days, or months. A mass flow calculation is used to continuously correct for temperature or pressure fluctuations. As it uses a venturi for flow measurement, pressure drops across the device is minimised.
“CCC does things that many can’t do such as continuously measure the true rate of methane compliance,” said Kromer. “Its tools can help monitor methane related to the exhaust as well as fugitive emissions.”
Vortex Services of Canada offers the Vortex Emissions Target Solution. It packages a number of elements that address methane measurements, such as a fuel measurement, fuel valves, a display panel, sensors (O₂ and NOx) a catalyst monitor, and several venturi elements to improve the fuel/air mix.