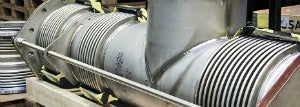
Belman has recently designed and manufactured a corner relief expansion joint made entirely from Hastelloy. The unit has been installed in the exhaust vapour pipeline section of an Austrian chemical plant.
Special design
After careful consideration, the customer selected the corner relief expansion joint in order to reduce the forces acting on the heat exchanger nozzle. Belman was requested to provide a solution that could take the thermal movements from both directions, while reducing the pressure thrust on the connection. The customer’s initial preference was for angular expansion joints, but due to the restricted space this option was not possible. Through the selection of a corner relief unit, the customer had the advantage of utilising the pipes natural flow. The unit was designed to absorb both axial and lateral movements. In this case, two flow bellows are in front of the bend, with the balancing bellow being connected to the pipe system through the tie rods. The corner relief expansion joint ensures that the loads acting on the pipe section close to the reactor are kept at an acceptably low level.
Choice of material
The choice of material was specified by the plant operator and was of critical importance due to the expansion joints location. The pipe section in which the unit is installed is connected on one side to a chemical reactor. For such a demanding environment, Hastelloy is an appropriate choice of material. The primary advantage of this nickel-based alloy is its ability to withstand high-stress service in a corrosive and erosion-prone environment, where more common iron-based alloys would fail. Hastelloy is widely used in pressure vessels, chemical reactors and pipes in the chemical industry. The customer insisted on the choice of Hastelloy as the material guarantees many years of high performance, even in the most aggressive environments.
Experience in special materials
Belman has experience in using special materials for its expansion joints. To ensure the shortest delivery times, we carry in stock not only standard materials, but also duplex, aluminium, titanium and high-nickel alloys such as Inconel, Incoloy, Hastelloy, Monel etc.
Please ask your Belman sales contact for more information about the materials with which we work.
Design parameters
Dimension: DN 300 – Installation length: 678 mm – Medium: Exhaust vapors – Design pressure: 0/10 barg – Design temperature: 20/180°C – AX: +/-11,5 mm – LA: +/-3,5 mm – Bellow: 2.4819 – Flanges: 2.4819 – Welding ends: 2.4819 – Inner sleeve: 2.4819