3D printing or “additive manufacturing” is the process of joining materials to make objects from three-dimensional model data, usually layer upon layer.
In 2017 the 3D printing industry was worth $7bn, up from $3bn in 2013 and by 2025 it is expected to account for over $20bn all over the world.
How well do you really know your competitors?
Access the most comprehensive Company Profiles on the market, powered by GlobalData. Save hours of research. Gain competitive edge.
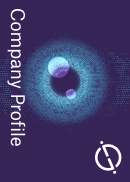
Thank you!
Your download email will arrive shortly
Not ready to buy yet? Download a free sample
We are confident about the unique quality of our Company Profiles. However, we want you to make the most beneficial decision for your business, so we offer a free sample that you can download by submitting the below form
By GlobalDataAdditive manufacturing (AM) has found its application in different sectors of the power industry, both in building prototypes and in mainstream production leading to process simplification and operational efficiency.
AM can produce components with complex geometries, consume fewer raw-materials, produce less waste, have reduced energy consumption and decreased time-to-market.
With the power industry under pressure, manufacturers are turning towards AM for solutions with reduced costs and shorter timeframes.
During the initial phase of making inroads in the power industry, 3D printing has achieved a fair level of success with the power industry and technological firms creating an ally for the benefit of each other.
3D printing in the solar power industry
Though technical feasibility of solar cells has been proved long back, the capacity factor (CF) is still low with an average of around 17% in best case scenario. The low CF of the solar panels makes it difficult to attain economics of scale for large solar plants and therefore requires subsidies for continued operation over a period of time.
3D printing can be a game changer in this respect as it is now being used to create solar panels.
Although the technology is at a very nascent stage, MIT researchers claim that applications of additive technology in solar panels could reduce manufacturing cost by 50% with 20% increase in efficiency compared to traditional solar panels. 3D printed solar panels are light super-thin solar strips which can be easily transported anywhere with reduced chances of damage.
In Australia, the Commonwealth Scientific and Industrial Research Organisation (CSIRO) used industrial 3D printers to print rolls of solar cells in the form of A3 sheets which can be used on the surfaces of windows and buildings and function as efficient solar panels. The scientists developed a photovoltaic ink to be used on the flexible plastic strips.
In another instance, The Australian Solar Thermal Research Initiative (ASTRI) in partnership with CSIRO developed a Concentrated Solar Plant (CSP) where the entire solar field is 3D printed.
3D printing and the wind power industry
Development and innovation through materials and manufacturing technologies are essential for the wind industry to prosper and to continue increasing its annual energy production.
AM could in the future enable in-site manufacture of turbine components that are designed for the unique needs of the resources of a particular location. Also, AM provides a tool to make up for the demand and supply for wind turbine spare parts of the discontinued models, for which the manufacturer will have limited quantity to meet the repairs.
The US Department of Energy’s (DOE) Wind Program and Advanced Manufacturing Office has partnered with public and private organisations to apply AM in the production of wind turbine blade moulds. Traditionally, blade design requires the creation of a plug, or a full-size representation of the final blade, which is then used to make the mould. This is one of the most time-consuming and labour-intensive processes in wind blade construction where 3D printing can save these critical resources.
Another potential benefit is that large wind blades would not have to be carried over long distances. Instead, the 3D printer could be taken on-site and “print” the blades thereby saving transportation cost. Also, this would cut down the manufacturing time of the mould by 35% making it possible to combine different materials in different areas of the blade.
3D printing and batteries
Research teams all over the world are exploiting 3D printing technologies to create complex internal structures of batteries with increased capacity and flexibility in shape and size.
A team from Manchester Metropolitan University, UK – funded by the Engineering and Physical Sciences Research Council – has taken up a project to develop a new kind of energy storage system (ESS) using a conductive graphene ink and a desktop printer capable of printing the ESS. Graphene, with its high electrical and thermal conductivity, can easily out-perform graphite – commonly used in Li-ion batteries.
A team from Harvard University is also developing a miniature version of Li-ion battery with the use of 3D printing. The micro batteries were fabricated by accurately printing stakes of different compound’s layers (Li4Ti5O12 or LTO and LiFePO4 or LFP), serving as the anode and the cathode respectively and enabling the development of self-powered miniaturized electronics, robots, medical implants and more.
Researchers at the Ulsan Institute of Science and Technology in South Korea have developed a novel production technique of Lithium-Ion batteries that gets one step closer to direct electronics printing.
IBM and ETH Zurich researchers created the first liquid battery through 3D printing called the “redox flow” battery. The particular battery can produce energy and cool at the same time. The team used 3D printing to produce a micro-channel system for supplying the battery with electrolytes. This system minimises the need for pumping power and eliminates internal high temperature.
In recent years increased numbers of electronic components have become 3D-printable and in the near future we can expect prototyping of smart functional hi-tech devices developed for home.
3D printing and conventional power generation
The US Department of Energy (DOE) has been supporting the development of 3D printing for applications in conventional energy.
In July 2018, the DOE selected 15 R&D projects for federal funding of $8.8m to develop innovative technologies for fossil fuel power systems.
In one of these projects, DNV GL plans to develop and validate computational support tools that optimise novel material combinations for fabricating micro channel heat exchangers via additive manufacturing for supercritical CO2 power cycle technology, providing new options for materials with property gradients for the fossil power industry.
In another project, United Technologies Research Center aims to demonstrate the application of computational methods and tools to microstructure evolution and mechanical properties prediction for additively manufactured nickel-based super-alloy parts for turbine engines.
In April 2018, Siemens achieved a milestone by producing the first 3D printed metal replacement parts for an industrial steam turbine.
According to the company, this is a game-changer, as it can reduce the lead time for producing these parts by 40%. In 2017, Siemens completed its first full-load engine tests for gas turbine blades, produced entirely using additive manufacturing technology. The company is in the process of developing additive manufacturing solutions not just for turbine blades, but also turbine vanes, burner nozzles, and radial impellers. The company acquired Materials Solutions, a company specialising in 3D printing, in 2016. Siemens is investing €30m in a 3D printing facility in the UK for Materials Solutions.
GE is also of the opinion that 3D printing is a disruptor for the energy industry. The company has shipped 9,000 3D printed gas turbine components.
The company further believes that 3D printing will enable it to enhance the efficiency of turbines in much less time owing to quick manufacture of prototypes and testing. An example of such components is the 3D printed fuel nozzles for the company’s HA-class gas turbines. The nozzle helped the company push the efficiency of the turbines to 64% and is now working towards achieving an even higher efficiency of 65%.
In 2016 the acquisition of Arcam AB, a Swedish inventor of electron beam melting machines for metal-based additive manufacturing, and a producer of advanced metal powders, helped GE gain the required expertise in 3D printing. Another benefit of 3D printing is that it makes the supply chain simpler by cutting costs.
3D printing and the nuclear power industry
R&D is also ongoing to identify the applications of 3D printing in the nuclear industry.
In February 2018, Russia’s state-owned nuclear power utility, Rosatom, established a company for the development of additive manufacturing technologies. It has already developed a pre-production prototype of a Gen II 3D printer, the commercial production of which is scheduled for this year.
In March 2017, Siemens successfully installed a 3D printed part – a metallic 108 millimeter (mm) diameter impeller for a fire protection pump, in the Krško nuclear power plant in Slovenia. This technology can be used for obsolete parts which are no longer available, allowing old power plants to continue their operations. Westinghouse is also using binder-jetting additive manufacturing in order to cut costs and cut short the lead times for parts that are difficult to obtain.
3D printing and the power industry: Conclusions
3D printing, a cutting-edge technology, is gradually finding its application in various facets of the power industry including renewable and conventional power sectors and battery storage devices.
However, as the technology is still in experimental stage and yet to achieve full commercialisation, it will be a matter of time to fully understand how deep this new technology can penetrate in the power industry given the high equipment standards required for efficient plant operation and the hazardous environment they endure.
Related Company Profiles
Siemens AG
Manchester Metropolitan University
IBM AS
CSP Srl
Westinghouse Holdings Corporation