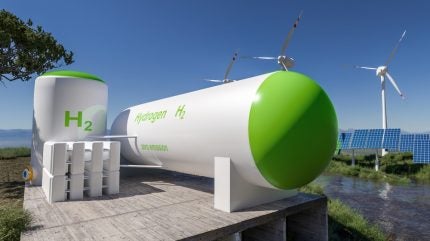
Green hydrogen is attracting much attention for its potential as a zero-emission alternative to fossil fuels to decarbonise heavy industries. However, considerable challenges influencing the levelized cost of hydrogen (LCOH) must be overcome for this nascent industry to reach a viable commercial level and fulfil its potential.
With emission reduction targets and net zero between 2030 and 2050, time is in short supply for successful solutions to be developed and scaled up. However, Worley is taking on the challenge with a series of measures to accelerate development of the necessary solutions to reduce the LCOH.
LCOH is used to determine the total production costs for hydrogen over the complete lifecycle of operations. There is an urgent need for solutions that address both the capital expenditure (Capex) and operating expenditure (Opex), while maintaining the highest safety standards.
To produce green hydrogen at scale, water must be split into its chemical elements using an industrial-sized electrolyser powered by renewable energy. An estimated 30% of LCOH is from Capex, according to experts at Worley. However, 70% of the LCOH is from Opex – due primarily to the cost of the energy required to run the electrolysis plant.
Resolving Capex issues for hydrogen projects
For any solution to be commercially viable, it must be replicable and scalable. Worley is developing a productised hydrogen solution with a lower capital cost to decrease the LCOH.
Initially, the focus is on smaller hydrogen plants with capacities of 100MW-200MW. However, achievable costs to make a project commercially viable are challenging at these capacities. So, lessons from these smaller assets will be used to scale up facilities and develop larger projects.
As the capacity increases, the results from multiple studies executed by Worley suggests the LCOH curve will trend downwards. The expectation is, the higher the plant capacity, the lower the LCOH.
“We determine the lowest possible cost for a functioning, safe hydrogen plant and design it, using standardisation and modularisation to create a minimum viable product,” explains Stock.
From the Capex perspective, the costs of technology are a significant component, accounting for 30%-35% of the total installed cost of a hydrogen plant. There are further expenses with the balance of plant (BOP), which includes components from original equipment manufacturers (OEMs) such as power systems and compression.
To lower costs and increase efficiency throughout the supply chain, Worley is building partnerships with technology providers and key OEMs. The company is working with partners to create a ‘supply chain led’ solution, which will simplify and reduce the cost of the hydrogen production unit.
“We remain technology agnostic – this is Worley’s strategy,” adds Stock. “We look at all the technologies available and can then be flexible with our own productised H2 solution to determine the overall lowest cost of technology.”
Measures to drive down Capex for hydrogen plants
Given the importance of standardisation in energy industries, reaching a consensus around specific solutions is essential. However, with the hydrogen sector still in its relatively early stages, there is no data available from fully constructed plants with learnings from commercial operation.
Worley aims to establish standards to build a plant, and then upgrade them in a structured manner when new innovations and learnings are emerging. This approach can be leveraged across the supply chain partnerships.
Another key factor is the scale up effects on equipment costs. If the standardised design is used to build multiple plants, the individual package components can have the same or similar design specifications. This enables the ordering of identical items in bulk from the same supplier for use at multiple plants.
Cost-reduction efforts are also applied to prefabricated modules. Here, modularisation can make a notable difference in reducing on site construction costs and timelines while increasing safety.
“Modularisation may cost more to initially fabricate, but cost benefits can be found in the construction phase,” says Stock. “We can identify savings via standardisation and modularisation that positively impact engineering, supply chain and construction,” he adds.
Opex and addressing energy costs for hydrogen production
Given that Opex takes up the majority of LCOH costs from energy consumption for electrolysis, a key goal at Worley is to both minimise energy usage and optimise its application.
To address Opex costs, Worley has collaborated with IBM and ABB to develop an Asset Optimisation Centre (AOC), which is a prototype digital platform designed to optimise the operating costs associated with hydrogen production.
“We adopt every possible measure to reduce energy consumption within the plant,” adds Stock. “Our Asset Optimisation Centre monitors the continuous operations and finds the best options available. Adjustments can be made in the plant instantaneously to produce the lowest levelized cost of hydrogen at that moment.”
The AOC will be able to identify the optimum time to produce hydrogen during the peak hours of generation from renewables, which is crucial for intermittent resources. For example, a hydrogen plant should operate at peak capacity when wind turbines are turning with the highest frequency. If using solar power, the ideal time for production is during the sunniest periods of the day. Factoring in other data insights such as weather forecasts will allow the AOC to predict the optimum conditions to schedule production.
“The algorithms in the AOC identify strategies to operate and manufacture the lowest cost of hydrogen considering weather conditions, storage options, the fleet of assets, technology, and maintenance options – and then can suggest a set point for operations to produce, at any one time, the lowest cost of hydrogen,” explains Stock.
A core component of the AOC is a digital twin, which is integral to achieving optimised maintenance strategies. Operational insights can be used for predictive maintenance to minimise downtime and optimise uptime.
Additionally, data from the AOC will certify that the hydrogen is produced using renewable energy, ensuring it meets green standards for sale in international markets.
How collaboration can advance green hydrogen
While green hydrogen is widely predicted to be a key contributor to the net zero economy, it is still developing. Determining the optimum solutions will take time. However, pooling resources and expertise from different companies and organisations can be a key driver to accelerate industry progress.
“The green hydrogen industry is a learning process. We want hydrogen to move quickly but it also takes a long time to build up experience. Collectively we need to change our approach and accelerate the learning process right across the industry,” adds Stock.
“All industry participants need to work collaboratively and we’re striving to lead the way. Whether it’s with our own supply chain to productise, with customers to achieve the business case, with technology providers to integrate solutions, or with government agencies that are looking at subsidies – it’s a collaborative effort. Driving down the LCOH requires collaboration across all these aspects.”
For expert insight on standardising hydrogen projects, Worley is leading a forthcoming webinar. To find out more and register, follow this link.