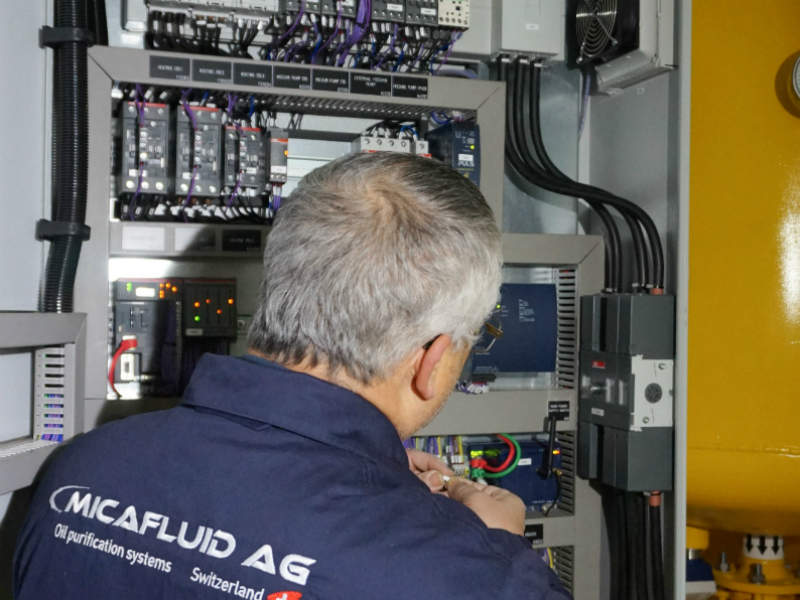
During training and commissioning, Micafluid AG process engineers perform training for the operators at our workshop in Schlieren, Switzerland. This can also be done at the customer’s on-site facilities.
The operators are trained in the concepts around “best practice”, process control, operation and maintenance. If malfunctions or interruptions of the operation occur, our engineers are available 24 hours a day to assist the operators on-site.
- ISO-certified inspection and training
- Providing experience
- Preventing unforeseen problems
Spare parts
Micafluid AG OEM spare parts and components are available through our Swiss Service Center. Our team is on hand to provide professional advice and expert assistance to help accurately identify your needs.
For optimal and safe operation, it is essential that only original components are used. Each component is tested and approved before delivery of the specific application.
We are happy to supply you with spare parts for service, maintenance and repair for all systems manufactured by us.
We also gladly send you documentation such as operating instructions, schematics and maintenance instructions.
Please indicate the type of plant and the order number so that we can identify the plant.
We are also happy to assist you should you have a problem with another oil treatment plant. For this, we need the manufacturer, model and the technical specification.
Micafluid offers:
- A full range of spare parts and components
- Fastest possible on-time delivery
- Best pricing
Repair and maintenance
Oil treatment plants, vacuum pump units and regeneration units that require maintenance are completely repaired and tested by Micafluid AG service specialists.
A detailed service protocol indicates the state of the unit at arrival, performed work, testing as well as new guaranteed performance after maintenance.
The repair and maintenance services include:
- Improving safety
- Reducing costs
- Keeping production lines running