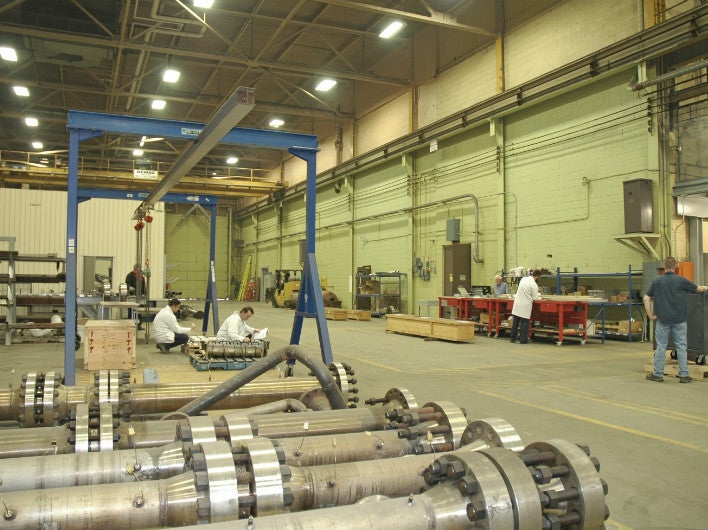
Numerous large and small scale facilities simulating various nuclear reactor components and systems have been fabricated and experiments have been performed simulating normal operation, as well as accident scenarios (often involving high energy levels) to provide data for use in code validation and licensing submissions.
Pressure drop, vibration and endurance tests have been performed for CANDU, PWR and BWR fuel assemblies and components, up to full-scale, for investigative and development purposes and for qualification of design improvements.
Simulations of both primary and secondary nuclear reactor coolant systems have been fabricated and tested to determine their characteristics under normal and abnormal operating conditions. Forced mechanical vibration tests are conducted in air to characterize the dynamic vibration behaviour of individual rods and fuel assemblies for interpretation of measured fuel assembly response while underflow test conditions.
Natural frequencies and mode shapes are obtained based on the phase relationships from accelerometers mounted on the fuel. Flow-induced vibration tests are performed to measure vibration amplitudes and resonant frequencies of the fuel assembly and individual rods. The displacement amplitudes and frequencies of the fuel assembly are measured using accelerometers installed in several fuel rods and proximity probes located on the fuel channel walls.
Endurance tests can be performed for extended periods at typical operating conditions which give the highest vibration amplitudes, to demonstrate reliability of the fuel and components. Stern Laboratories has a design team and construction crew that can bring new experimental development facilities into service rapidly and modify them quickly when necessary to meet new customer requirements.
Available facilities:
• CANDU fuelling machine simulator to investigate fuelling machine operational problems and perform qualification testing of new fuel channel components
• Various full-scale CANDU fuel channels to perform cross flow experiments, investigate various accident (such as LOCA) transients, investigate loading effects, etc
• High-pressure and temperature loop (rated at 11.5MPa and 315°C) with a pulse pump to provide variable frequency (up to 480Hz) and variable amplitude controlled acoustic pulsations in a horizontal CANDU fuel channel
• High flow, low pressure and low-temperature loop (rated a 340l/s @ 73m head, 1.5MPa and 150°C) for pressure drop, flow-induced vibration and endurance testing of up to two full-scale standard or XL PWR fuel assemblies
• High pressure and temperature single phase loop (11MPa and 315°C) with variable speed pump for pressure drop and endurance testing of BWR fuel components
• High-flow, high-pressure test loop with jet pump steam recirculation (rated at 9MPa, up to 10kg/s @ 50m head, up to 20% steam quality)
• Vertical channel to perform countercurrent flow limiting (CCFL) experiments on BWR fuel assemblies (10×10) at accident conditions
• High pressure and temperature loop (rated 18MPa and 371°C) with nitrogen injection capability to investigate the effects of dissolved nitrogen on Critical Heat Flux (CHF) at normal operating conditions
• Corrosion Test Loop (rated at 11MPa, 320°C with 70kW of DC power) for testing samples (e.g. nuclear fuel sheaths, steam generator tubes) under precisely controlled conditions of water chemistry, flow, temperature, pressure and heat flux
• Large-scale test facilities to determine removal mechanisms of radioactive aerosols in nuclear containments
• CANDU calandria vessel (¼ scale, two-dimensional) to perform moderator velocity and temperature distribution experiments
• CANDU Pressure Tube Burst facility (full-scale) with nine fuel channels to study the mechanical interaction of in-core components following a pressure tube/calandria tube burst at normal reactor operating conditions
• CANDU Header/Feeder facility (full-scale) to investigate the distribution of emergency coolant from reactor headers into the feeders at normal reactor operating conditions
• Cold Water Injection Test loop (large-scale) to investigate the effects of emergency cooling in full-scale, parallel CANDU fuel channels. This loop can also be used to investigate the maintenance cooling requirements in CANDU fuel channels at shutdown conditions
• Electric boiler (4MW, 12MPa, saturated water)
• Service steam boiler (3.8kg/s, 1.2MPa, saturated steam)
• De-ionized water storage tanks (200m³ capacity) and ion exchange column for water chemistry control