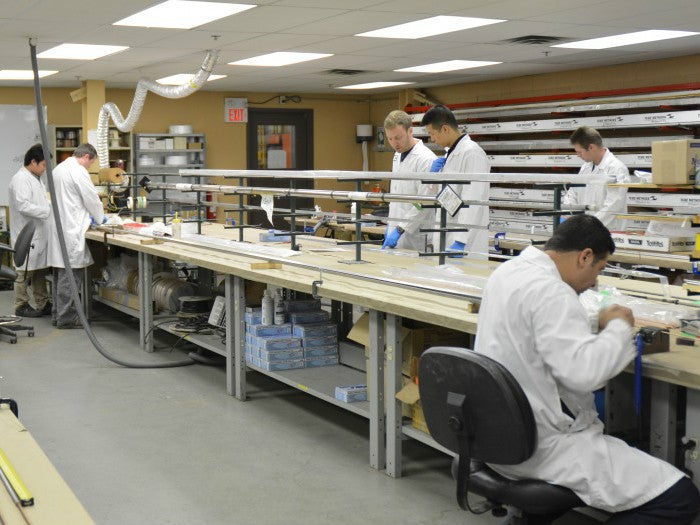
Stern Laboratories manufactures highly reliable electrically heated nuclear fuel simulators, which are designed and built to meet the particular requirements of each customer application.
These fuel simulators are used extensively in our laboratory, but have also been supplied to customers in North America, Europe and Asia for use in their laboratories.
Indirectly heated nuclear fuel simulators are designed and fabricated to represent various fuel designs, such as: BWR fuel rods with heat flux ratings over 300W/cm² and heated lengths up to 3,810mm which are used to perform Boiling Transition (BT) experiments in full scale (9×9 and 10×10) BWR fuel assemblies; PWR fuel rods with heat flux ratings over 400W/cm² and heated lengths up to 4,267mm, which are used to perform Departure from Nucleate Boiling (DNB) critical power experiments in 5×5 fuel assemblies; and CANDU fuel bundles and strings which are used to perform loss of coolant and emergency cooling experiments at operating temperatures over 1,100°C, with low heat flux.
Sheath materials used include nickel and Zircaloy alloys. Thermocouples can be installed in the heater rods internally in the insulation, internally in dual layer sheaths, externally in grooves in the sheath, or externally with spot welded tabs. Axial heat flux profiles can be varied with great design flexibility.
Many directly heated fuel simulations have also been built, particularly for critical heat flux (CHF) experiments in 28, 37 and 43 element CANDU experiments. These directly heated (Joule heated sheath) fuel simulators are usually made from high nickel alloy tubing and include internal thermocouples, which can slide and rotate to monitor temperatures (and dry out) over most of the heater surfaces.
Specialty fuel simulators, containing hollow pellets (UO2 or other material) with the electric heater passing through the pellets, capable of very steep temperature ramps to over 1,100°C (2,000°F) are also designed and built. New processes and better materials to advance our capabilities and services are continuously being investigated and developed.
Available facilities:
• Custom computer software for design of heaters and components
• Equipment and technology for joining metals (Zircaloy, Tantalum, Molybdenum, Titanium, Nickel, Copper, etc)
• Water jet cutting machine (414MPa) for precision machining of heater filaments
• Laboratory swaging machine to enable precise dimensional control
• Wire EDM machine for machining of heater filaments
• Helium leak testing equipment for the detection of defects
• Clean room for assembly of heater elements in a controlled environment