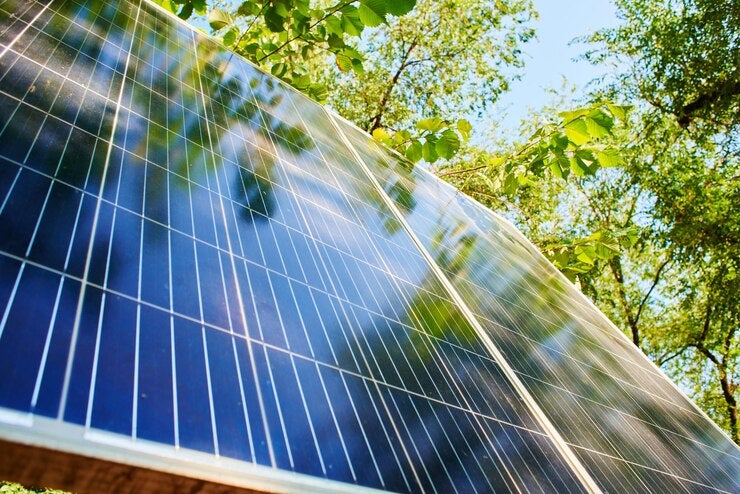
“The more you know about a customer’s day-to-day business needs, the better you can advise them and the better the acquired solution will work later in the application.” So says Florian Jammer, key account manager at Pfeiffer Vacuum for thin film deposition. He discusses the the technical trends on the market that one observes in the field of PVD for TFC gs – including wear protection coating of cutting tools, tools for solar cells, optical coatings for semiconductors, architectural glasses and more.
What are the most important points for customers given current political and economic instability?
FJ: Everyone has noticed that due to the geopolitical problems, some truths that were believed to be certain have changed. As a result, reliable partnerships have become even more important than they were 2-3 years ago.
What should customers look for in a reliable partnership?
FJ: A reliable partnership is characterized in particular by the fact that the supplier supports the customer throughout the entire value chain. This typically starts with the design of the vacuum concept of new plant types. It also includes a consultation carried out with expertise and a technically sophisticated calculation of the equipment, as well as the process consideration taking into account the selection of the right vacuum pumps. Ensuring on-time delivery following pre-defined schedules are moreover part of the mutual journey, and it ends with commissioning support as defined at the time of purchase. At Pfeiffer Vacuum, this is complemented, of course, by a globally available, well-positioned and well-equipped service footprint for our customers and their end customers which also ensures long-term satisfaction for all parties involved. To make sure all of the above listed customer’s needs get taken care for, a team of 10 colleagues intensively support our customers.
That certainly sounds like an approach worth pursuing, even in quiet times. What are the biggest challenges or fears at the moment?
FJ: In my opinion, we are currently dealing with two groups of main problems. On one hand there are availability and price issues. Components that were never difficult to obtain, such as simple power cables or electrical components, are simply not available. This means that plants cannot be completed, leading to delay in the commissioning.
Technical Trends + Innovations
- Usage of magnetic couplings for rotary vane pumps and Roots pumps;
- Displacement of diffusion pumps by turbo pumps;
- Usage of energy-efficient drives, e.g. IE4 motor;
- Availability of intelligent interfaces for embedding intelligent pumps.
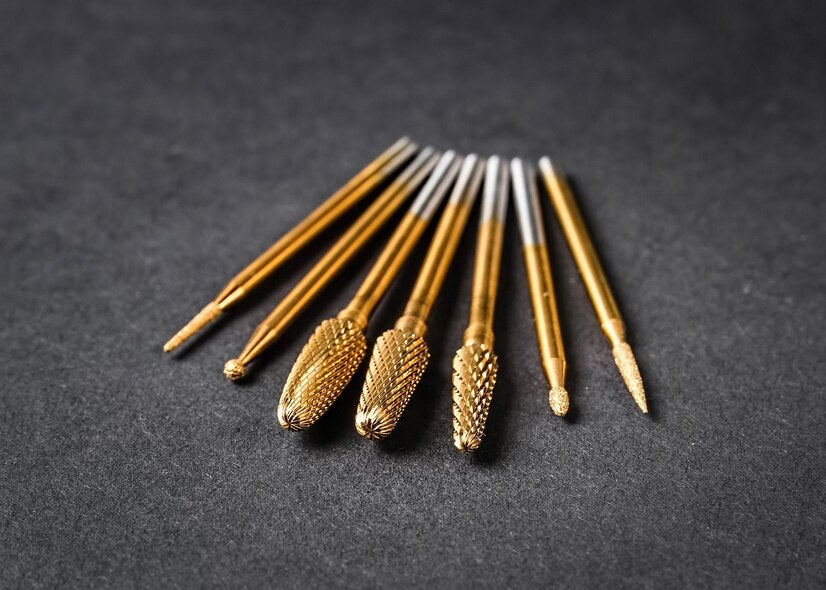
On the other hand the topic of energy has become increasingly important. Whereas in the past the purchase price was the decision criterion, today it is almost always the cost of ownership issue. This relates both to the effects of energy efficiency resulting in lower power consumption, as well as to service costs during operation. The topic of congestion symbol is also relevant, which may sound unusual in the context of industrial products. In fact, however, the trend has manifested that every company wants to position itself as environmentally conscious and sustainable.
Price is still important. But in customer meetings the intensity of the consultation is becoming more important again, and that’s where we can convince with our strengths in technical support and with innovative products. In coating lines, vacuum pumps are the second largest energy wasters after power supplies. It is also in line with the spirit of the times to consider the energy consumption over the lifetime of a product, keeping it as low as possible.
Let’s talk about saving energy with the appropriate vacuum equipment. Is it fair to say that something has changed in terms of technology that helps to save energy?
FJ: Oh yes, most definitely. It is nothing new that mankind will have to rethink sooner or later – but the explosive urgency is new. Current technical trends among our customers with regard to vacuum equipment include for example:
- The usage of magnetic couplings for rotary vane pumps and Roots pumps. Due to the sometimes very aggressive process gases, the oil begins to crack. This leads to the formation of small solids. In conventional pumps, these settle on or under the shaft seal and damage it. The result is leakage at the pump. Magnetic couplings do not require a dynamic seal, making maintenance more predictable and reducing the risk of failure.
- Or the displacement of diffusion pumps by turbo pumps, especially by those with hybrid bearings made of oil-impregnated ceramic balls, which are more robust in dust-rich applications in particular. The increased bearing wear with grease lubrication, especially in a flying bearing arrangement, has a considerable impact on the supplement due to the high speeds of the turbopumps of up to 90,000 rpm. As turbopumps work with a different pumping principle than diffusion pumps, and hence come with a different design, there are some variations in appearance and function detectable: Turbopumps have a smaller flange to the chamber, and expensive valve technology on the chamber is redundant. The requirements to the backing pump are lower (working pressure starts around 1 hPa vs. 1*10^-3 hPa), and they consume less electrical power. Turbopumps are more robust, require less service and less operating fluid (oil).
- But even if you stick to the same pumping principles, it is possible to use a more energy-efficient drive, such as the IE4 motor we use in our HiLobe, an intelligent Roots pump of the latest generation. Or do as more and more users are doing and utilize MSR technology (Multi Stage Roots technology), which is significantly more energy-efficient than screw pumps. Calculated as a rule of thumb, a pumping station of the latest technology can reduce energy consumption by about 30%. The first customers are already using MSR as pumping stations.
Would you point to any standout innovations among these new and interesting developments?
FJ: Oh yes, for sure. When considering the right pump technology and selecting the appropriate sizes, one should also not lose sight of intelligent interfaces for embedding them. No matter how powerful a pump is, if you can’t integrate it well into the software, all the fancy functions are of little use. Depending on the PLC control you use, you will need Profinet or EtherCat interfaces. All PV turbo pumps (HiPace and ATH), HiLobes and capacitive gauges are available with both. I have been wondering for quite a time why this is not talked about more.
A lot has changed, both in terms of what is required in the marketplace and how customers respond to the changing needs. The central importance of vacuum technology for the quality of PVD coating cannot be overstated. That’s why: Wherever you are uncertain about the workflow – whether it’s selecting suitable pumps for the vacuum process of a particular coating, asking about potential savings opportunities, wondering about the possibilities for integrating them into the overall system, or dealing with entirely different issues – Pfeiffer Vacuum will support and advise you.