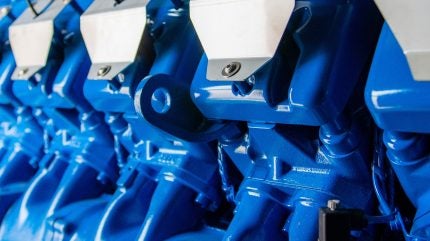
Today’s lubricants play a pivotal role in the engine management of CHP plants. Within these facilities, complex engines are employed to capture and utilise the heat recovered from power generation, with engine equipment required to work at optimum efficiency throughout its life span, often in challenging environments.
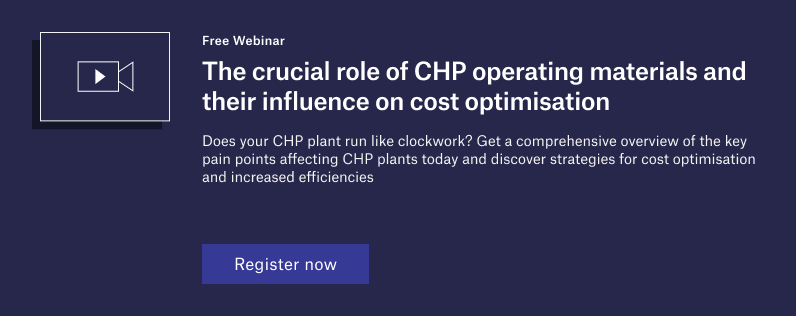
On September 10th 2024 at 3PMGMT, Texaco® Lubricants and GlobalData will be hosting a webinar to explore the crucial role of CHP operating materials and their influence on cost optimisation. To register, click here.
Maintaining equipment and ensuring its performance is vital for plants of this nature in order to be able to operate effectively. This requires CHP plant operators to not only assess and reactively protect their equipment during its lifetime, but also to proactively look at ways of ensuring long term efficiency and performance.
First, however, it is important to understand what it needs to be protected against. The arduous nature of the work required of CHP equipment means that it is susceptible to friction and wear, which can be hugely detrimental to a plant’s operation. With friction and wear come a whole host of potential issues, including reduced efficiency, increased maintenance and downtime, and shortened component lifespan.
All of these issues can lead to additional costs. Engine efficiency reductions can mean that the equipment requires more fuel for the same level of output, while additional maintenance and downtime increases operational costs. Similarly, shortened component lifespan and more frequent replacements can add significantly to the bottom line.
With this in mind, how can CHP operators help keep their equipment healthy, efficient, and in use? Fortunately, there are effective measures, such as regular maintenance, frequent monitoring, and the use of the correct lubricant.
In simple terms, lubricants are essential to the operation of power generation equipment, helping complex machinery, such as reciprocating engines and gas turbines, to help reduce the impact of friction, wear, and heat generation.
Lubricants are also helpful maintenance indicators – with oil analysis providing valuable information about the condition of equipment – an effective tool to help prevent unexpected downtime.
In addition, an often-overlooked aspect of the use of lubricants in a CHP setting is the impact they have on heat recovery. For instance, issues with a CHP plant’s cooling system can be responsible for up to 13% of the damage to CHP equipment.*
Fortunately for operators, Texaco Lubricants’ HDAX range of products has been designed to help equipment protection and performance in order to facilitate operational reliability. Texaco HDAX 9500 SAE 40, for example, offers piston deposit control, helping provide cylinder liner scuff and abrasive wear protection, and longer engine service life.
To help understand how to keep CHP equipment running at maximum capacity and keep costs to a minimum, please join Michael Guelck, Business Development Specialist at Texaco Lubricants, on September 10th 2024 at 3PMGMT to reflect on the impact of the Texaco HDAX range in a CHP environment.
Click here to register to view the webinar.
*Source: Dipl.-Ing. Michael Wentzke, Schadesreport Biogas-BHKWs