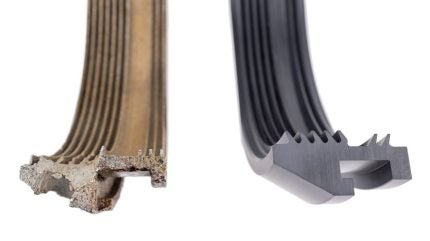
A long history of use has solidified aluminium’s status as the dominant material for manufacturing labyrinth seals – a type of non-contact seal used for minimising leakage and controlling contaminant ingression in centrifugal compressors. Today, despite the publication of several papers proving the superior performance of alternative materials, specifically high-performance thermoplastics such as PEEK, PAI, and PTFE, aluminium continues to be the go-to for OEMs.
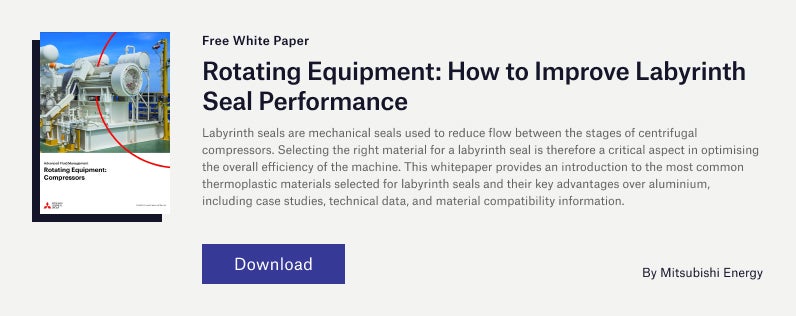
On one hand, since labyrinth seals are made to the end-customer’s specifications, more industry awareness is needed of the polymer advantage when it comes to improving the compressor’s efficiency and reliability. Nevertheless, many companies – both end-customer and OEM – have been deterred by the high costs of thermoplastic materials, which significantly exceed those of aluminium. To address both of these issues, this article discusses the key benefits of thermoplastic labyrinth seals while also assessing the return on investment (ROI) resulting from their improved sealing capabilities.
The polymer advantage
Labyrinth seals are comprised of multiple tooth-like projections and grooves. While maintaining radial clearances between the seal and surface, these projections create a tortuous path that is difficult for fluid and gas to flow through. In many designs, they consist of stationary teeth sealing against a smooth rotating surface, while in others they involve rotating teeth sealing against a smooth, abradable surface. Some designs even use a combination of the two, with interlocking teeth on either side.
Ineffective labyrinth seals can have a significant impact on a compressor’s efficiency, since any gas or fluid that escapes must be recompressed. Leakage is a common issue with aluminium labyrinth seals, which are susceptible to damage caused by vibrations, thermal fluctuations, and chemical exposure. Permanent deformation often takes the form of ‘mushrooming’ on the teeth, resulting in larger clearances for gas or liquid to flow through.
Faced with similar disruption, thermoplastic materials have an ability to deflect, thus avoiding permanent deformation. They also offer a much improved thermal performance, which helps to maintain consistent sealing properties under thermal cycling, and are inherently resistant to the corrosion common in a wide range of chemical environments. For example, filled with 30% carbon fiber to enhance its mechanical characteristics, Ketron PEEK offers strong temperature and chemical resistance, with a heat deflection temperature (HDT) of 230°C / 450°F. Meanwhile, with a 280°C / 534°F HDT, Duratron PAI is a thermoplastic characterised by its superior performance in elevated temperature and pressure conditions, in addition to an extremely low coefficient of friction.
From corrosion resistance to thermal performance and mechanical properties, these three factors combined mean that a well-functioning polymeric seal can be maintained over much longer periods of time than aluminium, keeping leakage, replacement costs, and downtime to a minimum. With all three of these advantages come opportunities to make long-term savings, but below we focus on the impact of efficiency improvements alone.
Quantifying ROI
Studies in rotating machinery suggest efficiency improvements of roughly 2-5% when switching to advanced polymer seals. This may sound small, but according to Derrick Bauer, Manager of the Material Engineering Department at Elliott Group, a leader in the manufacturing of oil-free, centrifugal compressors, “every half percent counts.”
“Being able to offer the best possible efficiency because of the seals is a big advantage,” he says, adding that the use of abradable seals made from a polymer known as Fluorosint 500 has enabled Elliott Group to achieve this. With the help of Mitsubishi Chemical Advanced Materials, Elliott made the switch to abradable polymeric seals in the 1990s and has never looked back.
“Abradable seals offer the lowest clearances, and lower clearances translate to higher efficiency,” he states. “The other major advantage [of polymers] is corrosion resistance. Depending on the application, aluminium and stainless steel seals can be eroded during service.”
Bauer is not the only expert to have emphasised the importance of these efficiency gains. One 2004 paper by John K. Whalen, Eduardo Alvarez, and Lester P. Palliser estimates that a 2% increase in compressor efficiency could equate to $700,000 annual energy savings in a two billion lb/year ethylene plant if all the major compressors were upgraded with thermoplastic labyrinth seals. This is based on the assumption that leakages are directly proportional to clearances.
Whalen et al go on to cite an example in which an ethylene plant in Orange, Texas upgraded a single compressor with Torlon PAI. After the upgrade, the plant discovered an increased compressor flow of 3.1% and a 2.7% reduction in steam consumption by the compressor’s steam turbine driver. Six other compressors were subsequently updated following these positive results, and through careful evaluation of all factors the plant was able to attribute a total plant output increase of 5% to the thermoplastic seal upgrade.
The paper’s authors note that, depending on the specific compressor, varying performance improvements are to be expected. High-pressure compressors and low flow compressors, for instance, are more likely to benefit from thermoplastic labyrinth seals on account of the labyrinth leakage making up a larger percentage of the overall gas flow. Compressors with high pressure drop seals can be expected to achieve a more significant improvement than double flow machines. Finally, older compressors with large clearance seals will see a more dramatic improvement.
Overall, upgrading centrifugal compressor labyrinth seals to thermoplastic ones offers oil and gas companies significant energy savings year on year. In combination with the other major benefits of the upgrade, such as the reduced maintenance costs and downtime achieved by the more long-lasting, durable, and corrosion-resistant material, it is clear that the higher upfront expenses are offset by substantial operational advantages for modern energy applications.
Sources
John K Whalen, Eduardo Alvarez, Lester P Palliser. Thermoplastic Labyrinth Seals for Centrifugal Compressors.