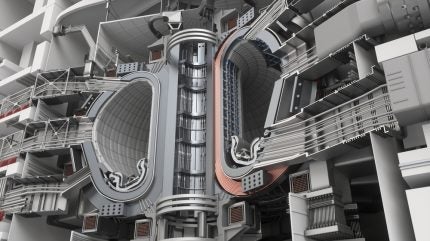
While there are still many unknowns in nuclear fusion science, the fundamental conditions required to unite two light atomic nuclei are well understood. Put simply, a combination of extreme high temperature, ultra-low base pressure, and a strong magnetic force is essential to ignite a plasma and confine and maintain a fusion reaction.
To achieve a necessary base pressure lower than 1·10-8 hPa, strong vacuum technologies such as turbopumps and multi-stage Roots pumps are deployed. These systems have proven their ability to achieve high compression levels, including for the light hydrogen isotopes used to fuel fusion reactions. Pumping speed remains a challenge, prompting some projects to look towards cryopumps as a potential solution. The one thing these various pump types have in common, however, is the extreme conditions they must withstand during a nuclear fusion reaction.
Operating temperatures
The temperature required to perform fusion depends on the type of reaction being attempted. Deuterium-tritium is widely preferred due to its high reactivity and the relatively lower plasma temperatures necessary to produce significant power. Nevertheless, temperatures remain more than 100 million degrees Celsius – six times hotter than the centre of the sun.
Reaching and sustaining these conditions is one of the biggest challenges researchers face, and sourcing vacuum pumps and other components that can operate reliably despite the high temperatures and subsequent thermal radiation is critical.
Added to that challenge is the strong magnetic fields used to confine and insulate the plasma. Pumping equipment is easily impaired by high magnetic forces, so vacuum systems are typically installed at a safer distance of four to nine metres from the plasma vessel. But this is less than ideal, since distance has a direct impact on the effective pumping speed reached in the vessel.
Magnetic shielding
According to Andreas Schopphoff, head of market segment R&D at Pfeiffer Vacuum, there is a need to install the vacuum pump as close to the vessel as possible while avoiding the damaging effects of the magnetic field. Turbopumps are particularly sensitive to these forces.
“With turbopumps, you would need to come as close as possible to the actual vessel because otherwise you lose a lot of pumping speed,” says Schopphoff. “That means you must deal with quite a high magnetic field. When you have the rotor of a turbopump rotating in a magnetic field, it will generate an eddy current due to Lorentz force. That heats up the rotor and at the end of the day it will damage the entire pump.”
Considering this trade-off between the need for proximity and the importance of protecting pumps from magnetic fields, shielding has become an important measure. “I think we have done very well in simulating what kind of impact magnetic fields can have on turbopumps and dry multi-stage Roots pumps, so over the years we have come to understand how to design the magnetic shield,” says Schopphoff.
“You always have to look at what kind of magnetic field needs to be shielded. We have done some shields for 10 milliTeslas (mT) and we are now looking at shields against 200 mT. That makes a big difference because we have to go for much higher wall thicknesses, and it adds quite a lot of weight. In an electrostatic field, you cannot really shield away a magnetic field – you dilute it by using more material.”
Ionizing radiation and tritium damage
Heat and magnetic forces are not the only stressors on the pumping system. Since vast amounts of high-energy neutrons are generated during a deuterium-tritium reaction, ionizing radiation will inevitably cause damage to the reactor wall and affect the performance of system components, including the pump and electronics. To avoid an impact on the pump’s drive electronics, they are set up in remote, radiation-shielded cavities. The distance between the pump and electronics can be up to 120 metres.
“These fast neutrons enter our material in a certain depth and can modify the properties of the material to a certain extent,” explains Martin Fischer, market manager industrial vacuum at Pfeiffer Vacuum. “It’s also something that we need to be very careful of with hydrogen isotopes. Tritium is not stable and if you have tritium penetrating your sealing materials, for example, it can replace the hydrogen atoms and result in a change to the material properties of elastomeric sealings.”
Developing tritium-compatible equipment is a key focus for nuclear fusion scientists. Metallic seals are required to ensure that tritium – the only naturally occurring radioactive isotope of hydrogen – does not escape. This fuel has also made the use of lubricants in pumping systems problematic since oil is very affected by tritium contamination.
“You need to have high pumping speeds for light gases in combination with a dry compressing pump (no oil), and that is a big challenge,” says Fischer. “We did come up with a solution that used a magnetically coupled Roots pump, and we found viable ways to keep the tritium free of oil contamination. We are able to combine this kind of pump with a gas cooler so that compressing towards atmospheric pressure with a Roots pump becomes possible .”
With over 130 years of history and the world’s first turbopump design under its belt, Pfeiffer Vacuum’s technologies have powered innovations across a wide range of industries. The company is committed to helping researchers solve challenges in emerging fields such as fusion, and its HiPace turbopumps have proven their suitability for these experiments in projects such as Wendelstein 7-X.
“There are many considerations that we don’t know yet because many of the activities in research and the private sector are ongoing,” says Fischer. “Requirements that come up tomorrow or in one year might not exist today, and we will need to find a solution for them. We have a portfolio we can access, but there is also the possibility of going into development activities together with our customers. This is something that Pfeiffer Vacuum is very good at because we have succeeded at it in the past many times, and this is definitely something that will be required in the future of fusion technology.”
To learn more about nuclear fusion and the role of vacuums, download the whitepaper below.