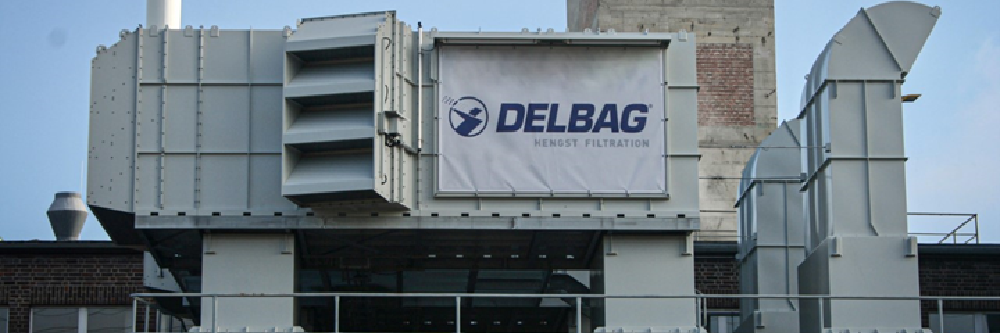
While gas turbines are designed to be as robust as possible, ensuring optimal performance requires attention to their environment. Dust particles can severely disrupt performance, especially if the turbine is operating in extreme climates, such as frost or high humidity. Over time, abrasive particles may erode or build up blades, and even the slightest change in the aerodynamics of the turbine blades can have a significant impact. Salt particles combined with a humid environment can lead to especially aggressive corrosive damage.
While regularly cleaning the blades would solve this problem, this would require shutting them down, leading to a reduction in power production that was being avoided in the first place. Removing airborne particles requires air filtration that is effective and robust enough to function even in adverse weather environments without frequent maintenance.
For one power station and heating service company in Germany, their 30-year-old pulse filtration air intake system was no longer functioning optimally, and they were facing frequent unplanned shutdowns.
Upgrading to three-stage air filtration
With people relying on this power station for their heating, frequent shutdowns were not an option. The company chose to replace its old hose jet filter system with a state-of-the-art Hengst (formerly Delbag) MultiMaster Vario static filter system, which included a three-stage filter setup.
Not only did this filtration system ensure more effective turbine blade protection, but it also provided the opportunity for an easy and proactive filter exchange, with three-stage filters expected to lead to significant savings in terms of operating costs further down the line. Each of the three stages consisted of 16 bag filter 4006 (ePM10 75%) in the first stage, and 20 filter elements in downstream stages. The second was fit with MultiPlus 8509 (ePM1 80%) as a reverse compact filter, and the third with MultiPlus 8511 (E11).
Overcoming obstacles: thinking outside the unit
Each site can present its own challenges, and at this power station the foundations for the old filter house were fixed concrete shafts, which also functioned as a system to release exhaust air. This meant that dismantling the shafts was not an option.
Hengst experts had to find a solution that allowed them the install all three filter stages in the limited space between the first and second shaft. The team refurbished the intake house at the front of the units, while the combustion air was to be realised via two lateral hoods.
Operating costs of air intake systems can be reduced by optimising air filters, variation of different filter types and utilising several filter stages. The three-stage MultiMaster Vario filter system that was used to filter the combustion air was designed for an overall airflow volume of 55,000 m3/h, making it ideal for preventing any dust accumulation that would lead to fouling, corrosion, or erosion.
To further prevent unplanned downtime, Hengst included an infrared anti-icing system in the weather hoods to prevent filter garment from freezing, and allowing it to operate at any time of the year. Additionally, the system features a fully integrated sound muffling solution so that it complies with noise pollution regulations.
To find out more about how Hengst provided effective air filtration within a tight schedule, despite on-site obstacles, download the whitepaper below.