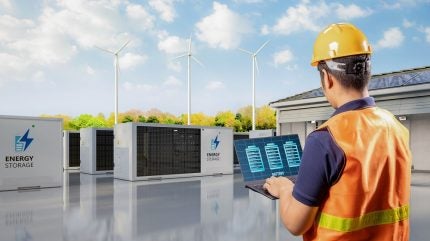
Battery energy storage systems (BESS) are essential to the renewable energy transition, providing capacity to store energy surges that can be released when solar or wind power generation is low. BESS ensure a consistent, reliable power supply to ensure that the energy industry reaches its sustainability goals and optimizes the use of renewable infrastructure.
However, electrochemical energy storage is notoriously vulnerable to overheating, which presents significant challenges to the performance and lifespan of BESS. Additionally, the rising energy density of units, and their proximity to residential communities, creates further complexities in safe thermal management and transportation.
In this Q&A session, John Turner, the Vertical Growth Leader for Renewable Energy at nVent, a global leader in electrical connection and protection solutions, helps BESS engineers understand and address the thermal and safety challenges posed by increasingly complex Battery Energy Storage Systems (BESS).
BESS installations are becoming increasingly energy dense. How can mechanical designers overcome this challenge?
The difficult part of increasing energy density is that, as you put more energy into a more compact unit, you have to get rid of the excess heat. You’re minimising the surface area for heat rejection while increasing the heat that discharges from the battery. Since there’s limited surface area because of the increase in compactness, liquid cooling is really the only method that helps manage the battery temperature. It’s critical for the batteries to maintain a temperature between 23 and 27°C, because if they get warmer or cooler, they start to degrade due to internal chemistry changes, and that reduces longevity in the life of that system.
BESS will be key to reaching net zero, including in residential areas. However, what risks come with introducing these energy-dense systems into urban areas?
The major one is the risk of failure and fire. That’s why there’s a lot of scrutiny put around the safety of these systems. Specifically, a fire bench and safety certification that BESS need to pass. Ensuring you’re keeping the electric load and the dangerous connections away from people in residential and urban areas is critical. Proper BESS enclosure design will protect the batteries from the environment, whether that’s wind, rain, snow, or fog, but also keep people safe.
How can enclosures help control the thermal management of BESS installations to improve performance and protect communities?
Enclosures incorporate proper thermal management design, from active cooling with air conditioners to liquid cooling with chillers. The enclosure is designed to make sure that you can mount all the components efficiently while retaining proper fluid distribution. If the battery system is outdoors, painting the enclosure in light colours can also help reduce the transmission of heat and lower the cost of thermal management.
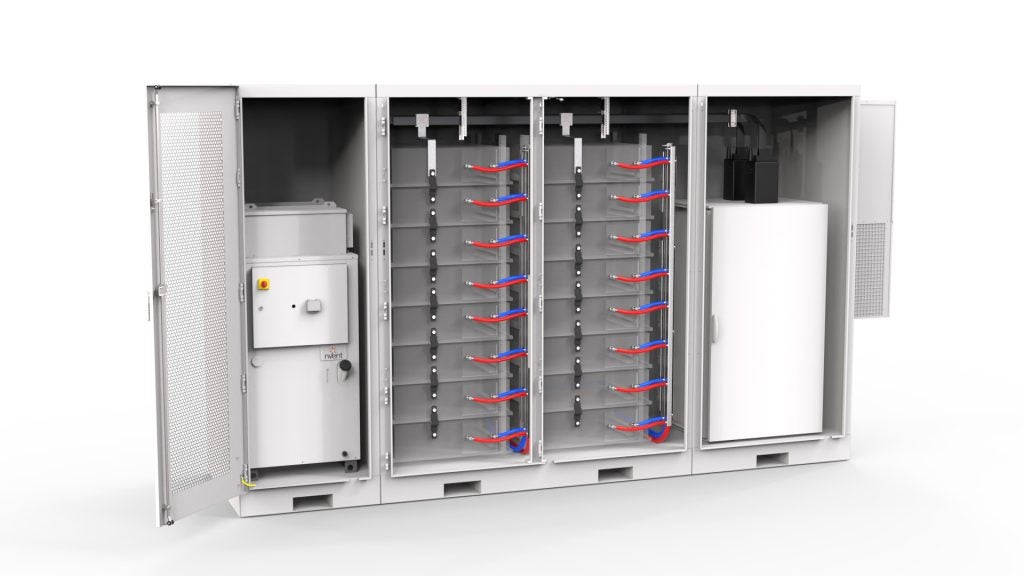
BESS installations are often heavy and difficult to manoeuvre. How can transportation challenges be overcome to ensure installations reach their destinations on time?
Proper testing is required to make sure the enclosure is designed to hold the weight of the batteries. Then, shipping tests need to be conducted to check that lifting procedures and transportation are well-documented and the enclosure can arrive on site the way it should. Obviously, nothing is completely bulletproof against full transportation, but making a system that takes into account the full weight of the batteries, plus all other components, has to be integrated into the design aspect early on.
As the chemistry behind batteries evolves, mechanical teams might have to adapt their designs fast to accommodate new battery types. How can flexibility and adaptability be inbuilt into BESS enclosures to prepare for this?
The best way to future-proof design is to make sure you get a scalable system where all the battery racking and also the enclosure’s width, height, and depth can be changed to accommodate new cell and module designs as the batteries get denser. With the nVent enclosure design, we can easily go deeper and taller to adapt to different modules while designing for a specific battery rack. If we don’t have a standard enclosure that will house these modules, we can design custom solutions that will adapt for future needs.
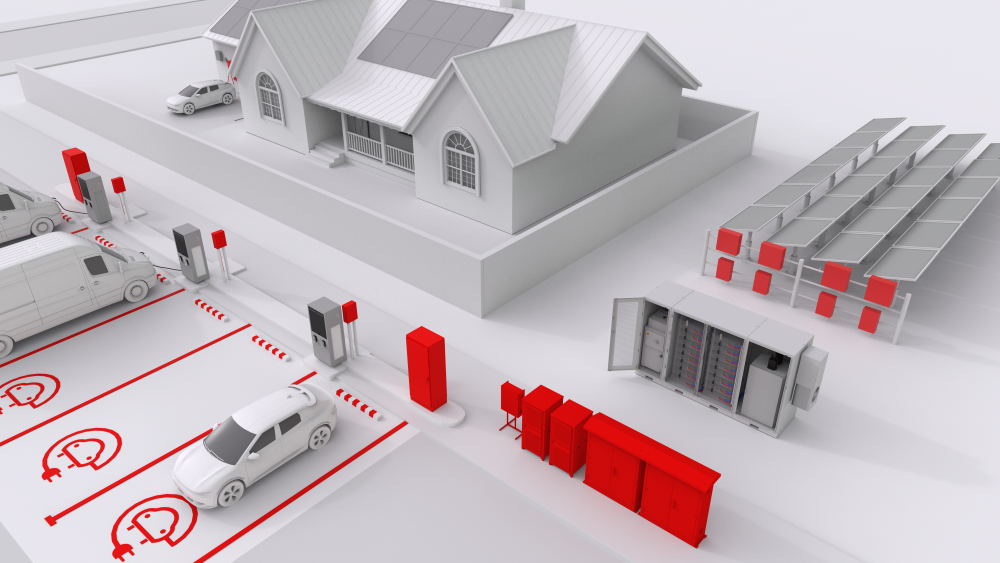
Finally, what do you think does the future look like for BESS? How will these systems evolve in the years ahead?
One of the main design themes we’ve seen in the industry is a transition to smaller units that can be scaled in the field. It’s about creating more of a build-a-block design where you can configure the solution based off of more standardised sizes and components. This gives more flexibility for customers and also helps to improve installation because they’re lighter to manoeuvre. From a technology standpoint, it’s just about how the chemistry changes and making sure that we’re agile with the scalability of full system design. That’s where nVent is in a really strong position with our capabilities in enclosure design, thermal management, and then the electrical fastening and connectors.
Contact John Turner at john.turner2@nvent.com to learn more about how nVent can help the industry overcome safety and thermal management challenges, or download the whitepaper below.
About nVent
At nVent (NYSE: NVT), we believe safer systems ensure a more secure world. We connect and protect our customers with inventive electrical solutions. We design, manufacture, market, install and service high performance products and solutions for mission-critical equipment, buildings and essential processes. Our solutions are helping build a more sustainable and electrified world. For more information, visit nvent.com.