In the energy transition, diversifying power sources is often seen as a necessary step on the route to net zero. According to the International Energy Agency, if we are going to meet zero emissions by the middle of the century, then a “dramatic transformation” of our energy system is needed, and the inclusion of new energy sources is necessary.
While renewable electricity generation shows promising growth, much existing energy infrastructure was designed for liquid or gas fuels. Industries such as shipping, construction and manufacturing still rely heavily on crude oil and natural gas. For consumers, much of our global energy infrastructure and pipelines, notably in the global south, was designed for the transportation of crude products. Decarbonising these liquid fuels provides a cheaper route to net-zero for these consumers, even if it only fills a gap on the way to renewables.
As such, some have looked into producing alternative liquid fuels from a variety of sources, from plants and organic matter to waste material. Plastic, which is originally produced using crude oil, can also be used to produce synthetic oil and gas through a process called pyrolysis.
Through pyrolysis, the plastic is heated to extremely high temperatures, between 300⁰C and 900⁰C, with a lack of oxygen. This causes it to break down into smaller molecules and transforming it into pyrolysis oil or gas. This product can then be used as a fuel or to create new, second-life plastic products.
Supporters of pyrolysis claim that it holds the answer to the dual challenge of plastic waste and excessive fossil fuel consumption. Pyrolysis company Stellar 3 has developed a “particular pyrolysis technology that is the most flexible and efficient with the highest quality outputs”, CEO Dan Nienhauser says. However, the process is not without its detractors.
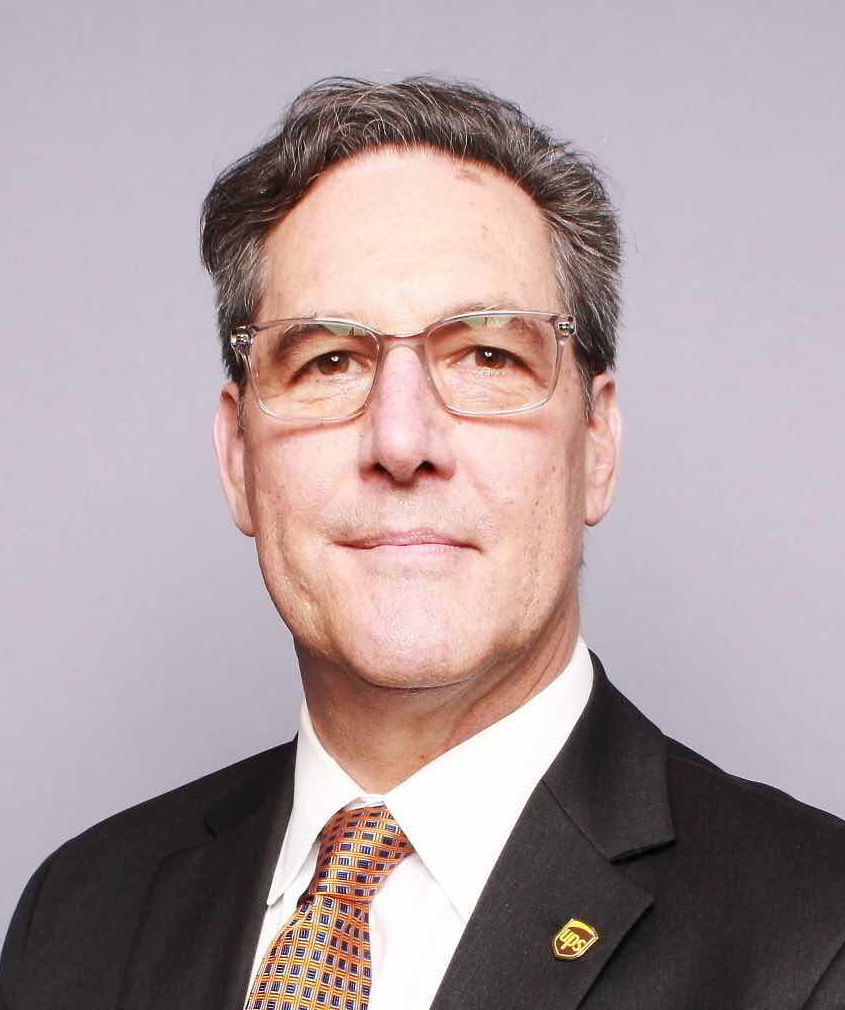
An emerging technology
Plastic degradation, through pyrolysis, uses differing types of plastic, such as polyethylene or polystyrene, to produce a variety of liquid gas fuel products. Plastics can be added individually or as a mix in order to produce a diverse range of products. Differing types of catalysts are used to improve the pyrolysis process, including ZSM-5, zeolite, Y-zeolite, FCC, and MCM-41. While high temperatures are used, pyrolysis avoids incinerating its feedstock, instead reforming it into fuels.
Many pyrolysis facilities produce a liquid oil with a high heating value which resembles conventional diesel. This product can be used to power vehicles and machinery after it is refined and blended with conventional fuels. As such, fuels produced through pyrolysis could offer a lower carbon solution for hard-to-abate industries.
Stellar 3 has developed a pyrolysis process which can recycle plastics including PVC. “PVC is typically avoided because it has a chlorine in it, so we have designed, developed and built a chlorine extraction pre-pyrolysis unit. What that does is it keeps the plastic to a temperature that where the plastic is still liquid, and then the chlorine evaporates, that chlorine is captured and condensed into a 30% hydrochloric acid into a special container, and then the rest of the plastic goes through the regular pyrolysis process”.
Pyrolysis is not a form of incineration, Nienhauser adds, as when burning waste an amount of energy is lost in the process.
“You're eliminating all the carbon footprint of taking oil out of the ground, shipping it to a refinery and then shipping it all the way to importing countries. Some of that can be replaced with a blend-ready diesel, produced locally based on the plastics that are there”.
Local energy production
For Nienhauser one of the major benefits of pyrolysis technology is that the plants are small enough to accommodate fuel production on a local level which is then transported in liquid form. Stellar 3 builds facilities which take in 30 tonnes of waste material per day, the equivalent plastic waste production of 250,000 people per day.
Alongside others globally, the company manages a processing facility located in the Philippines. “Because of the island location, one of the challenges is that you don't have extra room for landfill. So, once it's filled, you put extra plastic on the top of the landfill, and it rolls down into a river that ends up in an ocean. Our objective by 2030 is to have the capacity to take 500 tonnes of landfill waste per day and use it in a waste transformation facility,” Nienhauser adds.
The problem of plastic pollution
With the increased consumption and urbanisation of our society comes more plastic waste. Around 12 million tonnes of plastic makes its way into the world’s oceans every year. Environmentalists and NGOs are calling for better waste management of plastics. Currently, 9% of plastics are recycled and an additional 22% are mismanaged. Much of the plastic we used is currently either heads to landfill or the oceans.
Pyrolysis has the potential to increase the demand for second-life plastics turning them into a useful product. However, while pyrolysis offers a potential waste solution critics argue that it is not the fix-all green solution for both plastic waste and fossil fuel use.
How green is pyrolysis?
Producing a fuel from a hydrocarbon product means that when that product is burned, it will produce carbon dioxide and other greenhouse gases. As such, they can only reduce emissions from their suppliers, not their consumers. Synthetic fuels that make use of pre-existing oil and gas infrastructure could also delay the infrastructure overhaul need to transform our energy system. Detractors argue that whether it is oil and gas pipelines or vehicle engines, at some point our infrastructure and technologies will have to change.
Additionally, pyrolysis is not a perfect science. When producing a product from waste, it is difficult to ensure the exact same product every time when the input material varies. Critics say that given the variety in plastic types, in reality only a fraction of it is recycled effectively in pyrolysis.
But for Nienhauser, recycling any plastic should be counted as a positive. “When you put something into a system and you turn it into a gas, you can't change what it is from a from a molecular structure standpoint. That said, the developing world is very excited about ways of reducing waste.”
Stellar 3 is also developing recycling facilities that handle only one type of material. “We've done a pilot facility looking at end-of-life tires. Frequently, there are these very large facilities where their only purpose is to shred tires. We have a new plant that, instead of taking the shredded material, takes a whole tire and puts it into a vacuum sealed environment where the rubber and petroleum-based part is melted off it. You leave the steel and the fabric on top of a sieve and then you have the liquid that proceeds into the pyrolysis chamber.”
“In addition to providing a petroleum and carbon black product that can be put back into the tire industry, and you can create around 60% of a new tire if you have the right efficiencies in your system for from an old tire. And that for us is very exciting where we start to really cut back on those raw virgin materials”.
How much energy does pyrolysis need?
Any kind of recycling requires large amounts of energy, especially when heating materials to high temperatures. However, recycling remains more energy efficient than producing a product from original materials.
“It’s part of pyrolysis’ reputation, because there's a lot of companies that have done it less efficiently in the past,” says Nienhauser. But pyrolytic facilities are innovating: Stellar 3, for example, burns excess synthetic gas produced from the process to produce the necessary heat. “Once it's operational, the process needs a low level of external power which can be provided from renewables.”
For Nienhauser 2023 is “the year of chemical recycling”. “This is really a time where the circular economy starts to have economic legs, as opposed to being something that we do because we really have to. With all the climate challenges going on today, I think anything we can do, even if it's flawed compared to what we may envisage as a perfect 2050 scenario, it’s something we should start doing as soon as possible,” he concludes.