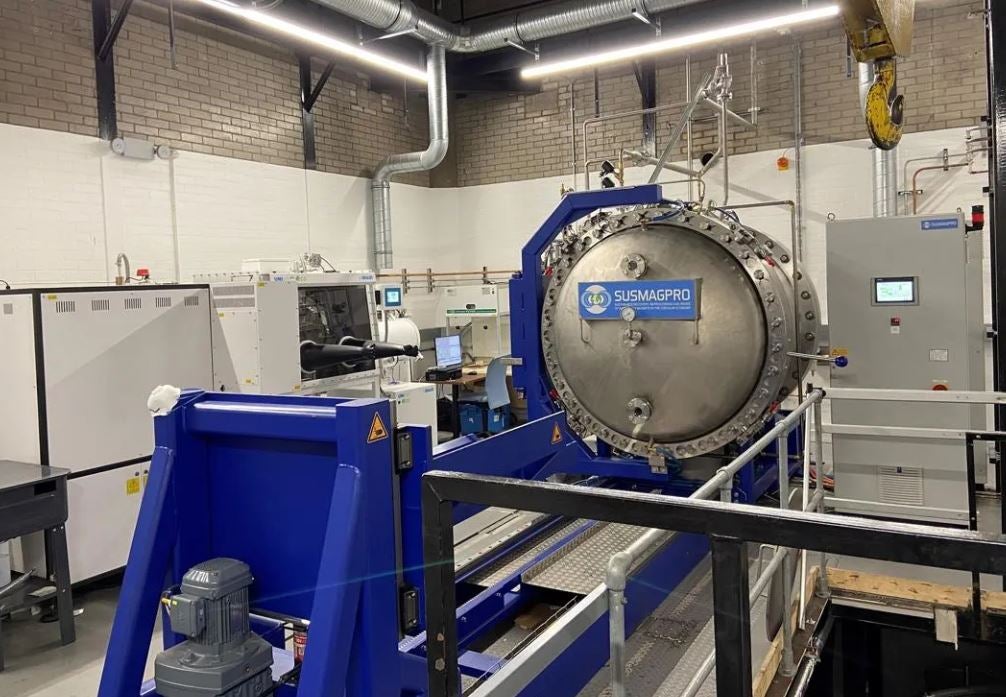
Rare earth technology company Maginito is to acquire Birmingham-based recycling company HyProMag, positioning the city as the UK’s first centre for rare earth magnet recycling.
The manufacturing facility will be located in Birmingham’s Tyseley Energy Park, which develops low and zero-carbon transport fuels including hydrogen, electric vehicle (EV) charging, biogas and biodiesel.
Established by academics from the University of Birmingham’s Magnetic Material Group, HyProMag uses a patented process known as Hydrogen Processing of Magnet Scrap (HPMS) to extract rare earth metals from scrap.
According to the University of Birmingham research group: “HPMS is used to reduce permanent magnets containing neodymium, iron and boron to a demagnetised powder”.
The company says its technologies target “key challenges” in “efficiently extract[ing] these materials from a wide range of scrap sources”, reprocessing them with a “minimal environmental impact compared to primary production”, said Professor Allan Walton, HyProMag co-founder and head of the Magnetic Materials Group at the university.
Short loop magnet recycling is expected to require 88% less energy for sourcing critical minerals than primary mining processes.
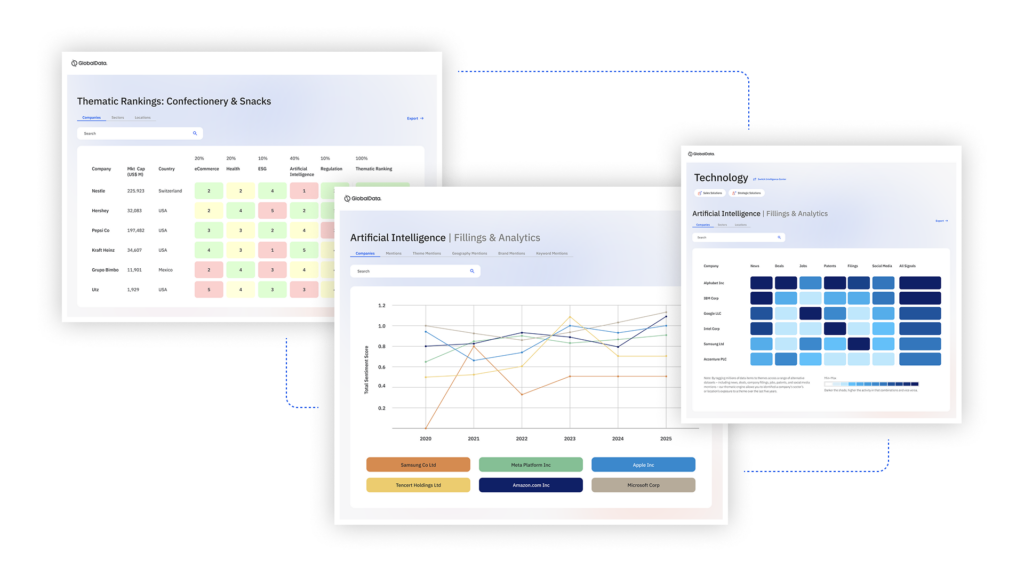
US Tariffs are shifting - will you react or anticipate?
Don’t let policy changes catch you off guard. Stay proactive with real-time data and expert analysis.
By GlobalDataRecycling solutions to rising rare earth metal demand
According to the International Energy Agency, the average electric car requires more than double the amount of copper and manganese than a fossil fuel-powered car. It also uses several other minerals, rarely used in other vehicles, such as lithium and graphite.
Given growing demand for critical minerals, interest in recycling the metals is growing, and the UK Government seeks to promote recycling.
Rare earth metals are used frequently in energy transition technologies such as EV charging batteries, solar panels and wind turbine generators, as well as consumer goods such as mobile phones and loudspeakers.
“Creating a more circular economy for critical minerals not only reduces waste but also alleviates pressure on primary supply (for instance, from mining). An efficient circular economy of critical minerals would require increased recovery, reuse and recycling at the end of a product’s life,” states the UK’s Critical Mineral Strategy.
The EU’s critical raw mineral act encourages member states to adopt and implement critical mineral recycling, aiming to move towards at least 15% of the EUs annual consumption coming from recycling by 2030.
According to President of the EU Commission Ursula von der Leyen, the Act will “bring us closer to our climate ambitions. It will significantly improve the refining, processing and recycling of critical raw materials here in Europe.”
HPMS recycling at Tysley Energy Park
David Kennedy, director of HyProMag, explains that the company was founded to “accelerate the commercialisation of the HPMS process”. The collaboration with Mkango has “supported the company’s growth and enabled the participation in major collaborative projects on rare earth magnet recycling”, he adds.
HyProMag built a pilot plant for HPMS recycling last year, and has now started to build a large-scale ‘short loop’ recycling facility at Tyseley Energy Park. The process here will supply neodymium/iron/boron magnets and alloys for a wide range of markets including automotive and electronics.
The plant will have a minimum production capacity of 100 tonnes a year. The $5.3m (£4.3m) project is being funded by an Industrial Strategy Challenge Fund known as Driving the Electric Revolution and delivered by funding body UK Research and Innovation.
Production is due to begin in the UK this year, with the company also beginning production in Germany in 2024.