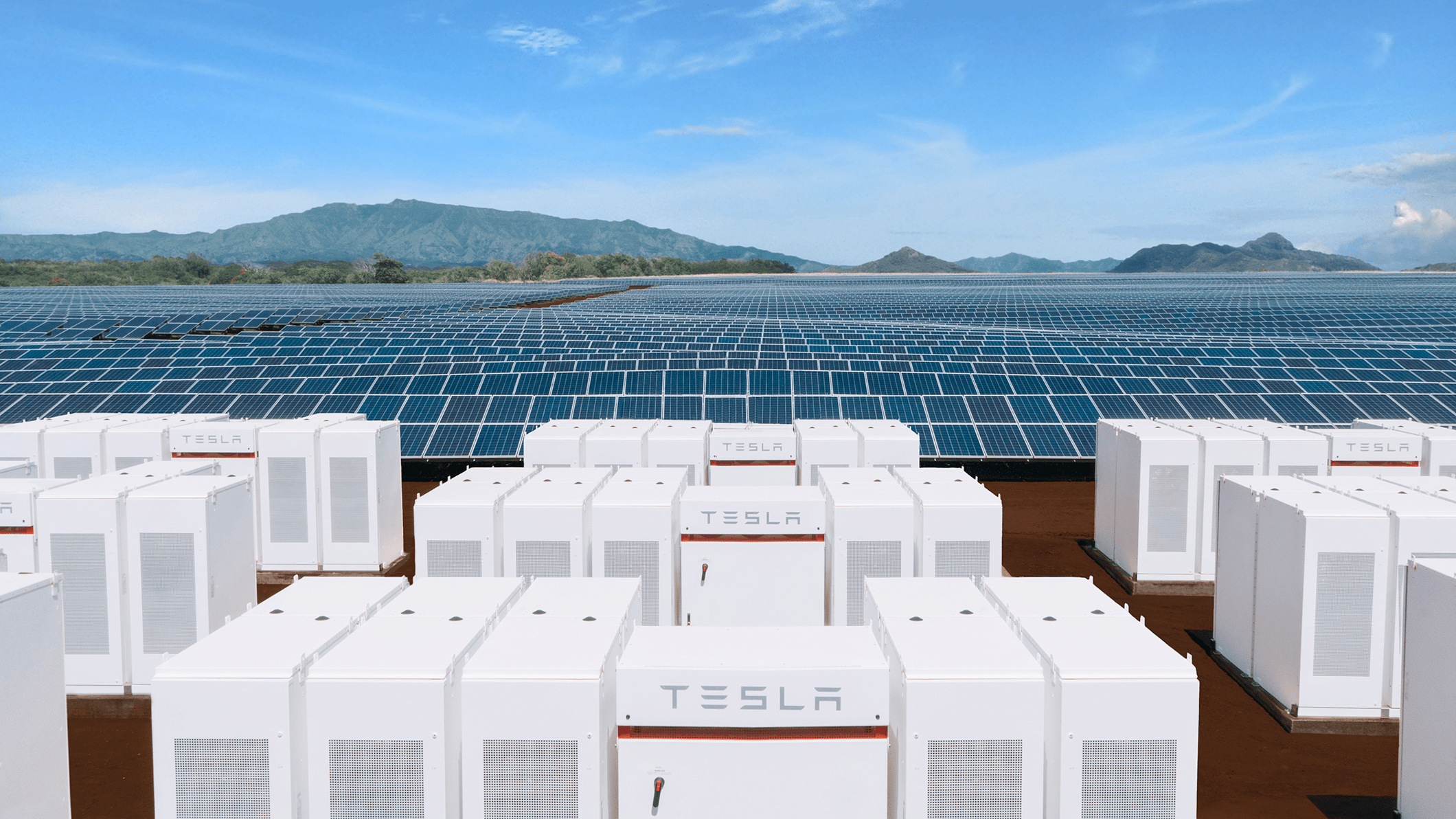
On Tuesday, electric vehicle and battery manufacturer Tesla held its ‘Battery Day’, announcing its intention to halve the price of battery energy storage.
The company, which began in electric vehicle manufacturing, has become a leader in utility-scale energy storage supply. The company announced plans to build a new battery production plant in the US and to scale up cell production to produce 100GWh in 2022.
On an outdoor stage in California, Tesla CEO Elon Musk and senior vice-president of energy engineering Drew Baglino told shareholders about five technology innovations the company has moved into production to halve production costs.
Materials and components in batteries change to allow greater capacity
One of these measures involves the company ending its use of cobalt in batteries. Tesla joined the Fair Cobalt Alliance in September, and Musk said the company has had difficulty in finding ethical and responsible sources for the metal. However, it did not give an estimated timescale for the change.
Cobalt is a suitable metal for stabilising energy flows in mid-tier batteries. However, a paper in the Journal of the Electrochemical Society suggests that cobalt has a negligible effect in higher energy, high-nickel batteries.
Baglino told shareholders: “Using novel coatings and dopants, we can get a 15% reduction in cathode cost per kilowatt-hour. We are also looking at the processing costs for cathodes. About 35% of the cost per unit of storage comes from transforming the battery metals into their final form.
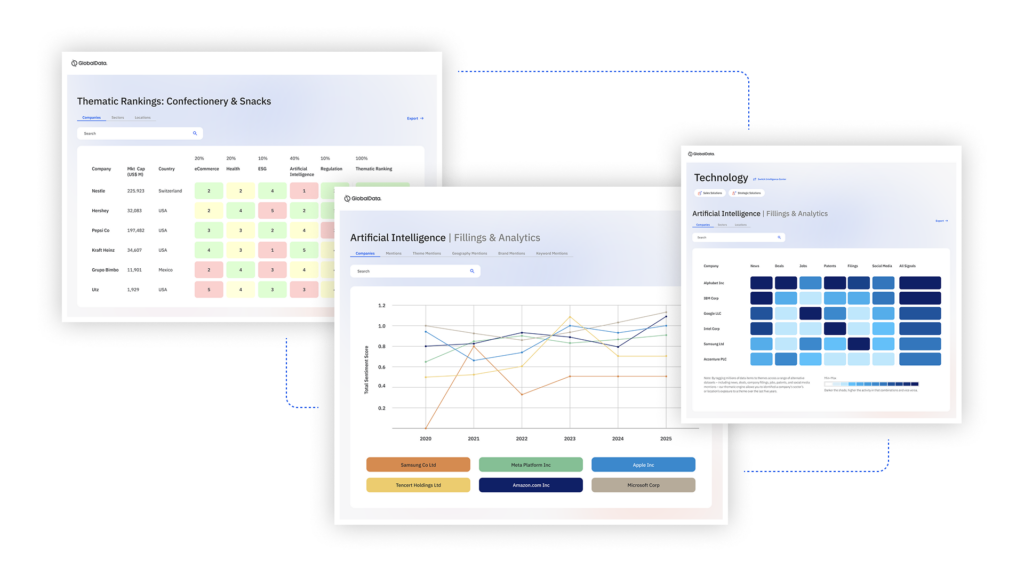
US Tariffs are shifting - will you react or anticipate?
Don’t let policy changes catch you off guard. Stay proactive with real-time data and expert analysis.
By GlobalData“We’re proposing a process that requires 66% less capital investment and a 76% reduction in processing cost.”
A ‘three-tier system’ for Tesla battery vehicles
Musk continued: “In order to scale, we need to make sure we are not constrained by total nickel availability. I think we need a three-tiered approach to batteries, starting with iron as a medium-range battery, then nickel-manganese above that, then high-nickel for long-range applications.
“Everything considered, nickel is maybe 50% or 60% better than iron. It would be relatively straightforward to do a cathode that’s two-thirds nickel, one-third manganese, which would two thirds more energy storage with the same amount of nickel.”
We intend to increase, not reduce battery cell purchases from Panasonic, LG & CATL (possibly other partners too). However, even with our cell suppliers going at maximum speed, we still foresee significant shortages in 2022 & beyond unless we also take action ourselves.
— Elon Musk (@elonmusk) September 21, 2020
Cathodes form the negative terminal of a battery, with another metal forming the positive anode terminal.
The executives announced plans to use silicon in anodes, which stores eight times the energy of standard graphite materials. While silicon is relatively abundant and therefore cheap to use, it swells when charged with lithium in a battery. Baglino said the company had designed new batteries with this in mind, allowing it to reduce anode costs by 5%.
Manufacturing, recycling and structural batteries
Another change in the internal layout and size of its electric vehicle cells would give it five times the energy storage capacity and a 16% range increase, according to Baglino. Overall, this results in a 14% cost decrease.
Musk said reassessing the battery manufacturing process allowed the company to make 18% cost savings. He said: “We can make a terawatt-hour less space than it took to make 150 gigawatt-hours. I would not have thought this was possible several years ago.”
Baglino also announced the start of Tesla’s battery recycling pilot in its Reno factory during the next quarter. The company believes it has a greater capability to recycle its own batteries than third-party recyclers.
Furthermore, Baglino said the could eventually not need to use mined minerals: “At that point, we have an awesome resource in those batteries to recycle, to make new batteries. The difference in the material coming from vehicles, versus the ground, means we would always go to the vehicle first.”
The executives said these processes would reduce battery pack costs by 12% alone. Tesla would save a final 7% of costs by integrating cells into the structure of its vehicles. Musk likened this to the structural fuel tanks found within aeroplane wings, saying: “It’s just how it’s done”.