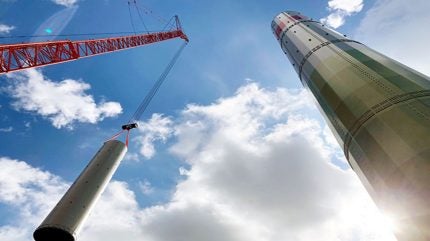
ENERCON, Salzgitter’s subsidiary Ilsenburger Grobblech and TMGROUP’s SMB Schönebecker Maschinenbau have collaborated to produce a lower-emissions steel tower for wind turbines.
The steel tower components will be used in early 2025 on an E-138 EP3 wind turbine as part of the Diepholzer Bruch wind farm project in Lower Saxony, Germany.
The project will make it one of the first onshore wind turbines in Europe, and the first in Germany, to feature a tower constructed from lower-emissions steel.
ENERCON global procurement director for towers Stefan Frey stated: “Working together with such strong partners from the steel industry means we are making significant progress in our mission to integrate sustainability systematically and measurably in our products and processes.
“By pooling our expertise, we can reduce the CO₂ footprint of this steel tower by more than 70%. This co-operation provides us with an important basis from which we can offer our customers an even more sustainable tower option in future, while of course maintaining our high quality standards and using state-of-the-art tower technology.”
Wind turbines featuring a hybrid tower concept are fully constructed from steel. The bottom section consists of pre-edged steel plates, while the top is made of conical steel sections.
This design offers advantages in installation and transport, especially with increasing tower heights and larger base diameters.
To reduce greenhouse gas emissions in producing heavy plates, Ilsenburger Grobblech is utilising CO₂-reduced slabs from its sister company Peiner Träger and another European partner.
These slabs are made entirely from scrap in an electric arc furnace (EAF).
Ilsenburger Grobblech managing director of sales Thorsten Gintaut said: “We are working closely with strong research and industry partners to achieve a steel production that is as climate-neutral as possible. We are therefore very pleased to be producing the first lower-emissions tower for a wind turbine in Germany together with ENERCON and other companies from the steel industry.
“The Salzgitter Group is a leader in the transformation towards low-CO₂ production processes and steel products. With our SALCOS – Salzgitter low CO₂ steelmaking programme, we are working on replacing fossil fuels with hydrogen produced from renewable energies.
“The aim is to avoid the generation of CO₂ in the steel production process from the outset and thus enable us to reduce our overall CO₂ emissions by an estimated 95% by the end of 2033.”