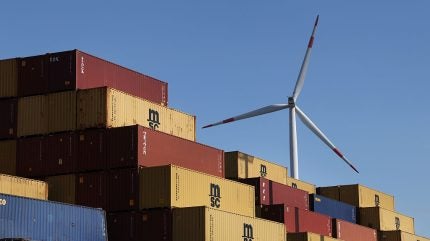
Wind power is increasingly occupying space in the global energy mix, and supply chains for turbine components are growing in tandem.
Both public and private investment has been funnelled into the technology as part of the energy transition while traditional energy companies, including oil and gas giants such as TotalEnergies and Equinor, have invested in wind to diversify their portfolios.
By 2028, global wind turbine installation, both onshore and offshore, is predicted to reach 760.20GW, up from 119.86GW in 2023, according to Power Technology’s parent company GlobalData.
However, the industry’s supply chain poses a potential hurdle to these ambitions, as the construction of wind turbines requires a range of materials including steel, fibreglass and rare earth elements (REEs), all of which are dominated by China.
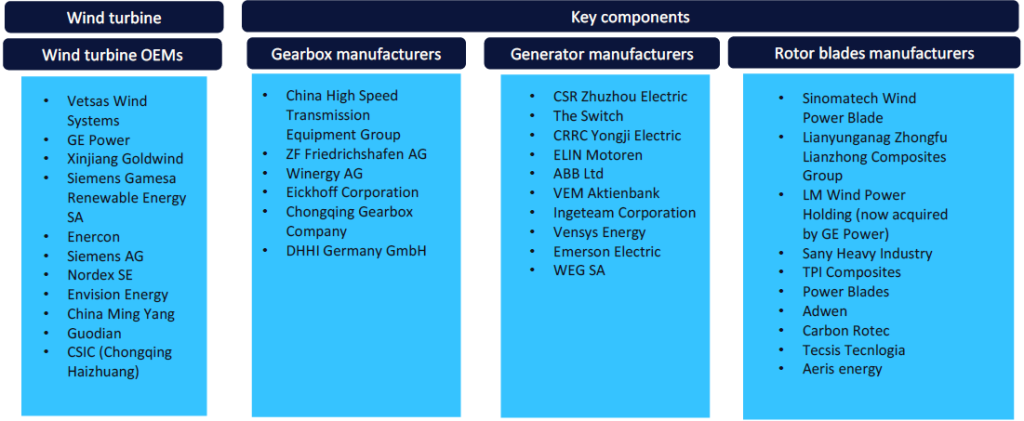
Recent geopolitical developments led by US President Donald Trump’s trade war and macroeconomic headwinds have exacerbated the complexities of these supply chains for manufacturers globally.
Indeed, in December 2024, wind developer Ørsted cited supply chain bottlenecks as a key reason for opting out of Denmark’s offshore wind farm tender in the North Sea, which received no bids overall.
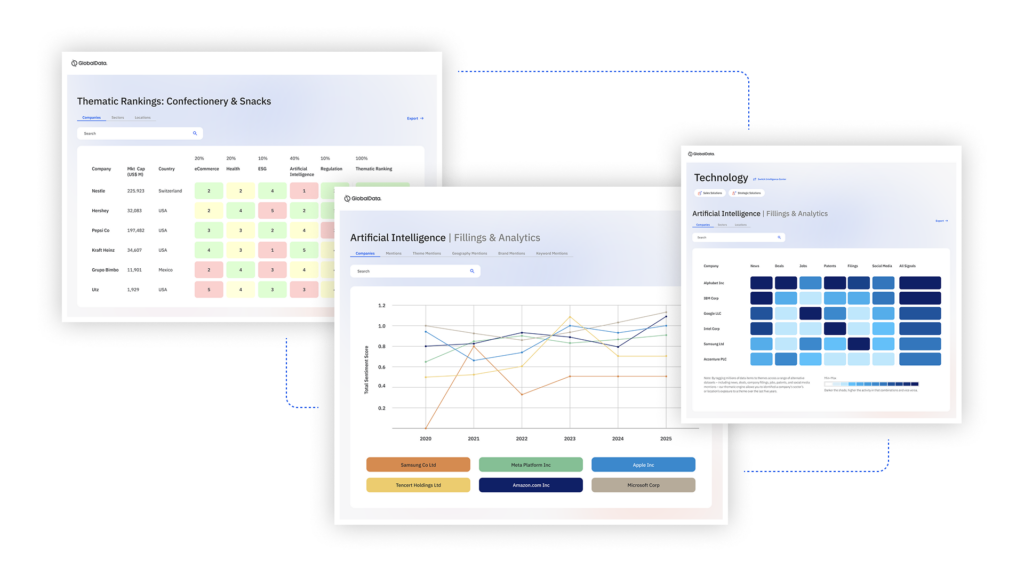
US Tariffs are shifting - will you react or anticipate?
Don’t let policy changes catch you off guard. Stay proactive with real-time data and expert analysis.
By GlobalDataOnly two months later, in February, Mitsubishi paused its plans for offshore wind projects in Japan, pointing to supply chain issues once again.
For the industry to maintain its upward trajectory, securing supplies of wind turbine components is crucial. Diversification through alternative materials and near-sourcing are key risk management strategies for wind manufacturers to futureproof their place in the energy transition.
Steel in wind turbines
Steel serves as the backbone of wind development, constituting up to 90% of a turbine’s mass. As such, the health of the global steel supply chain is of major importance to wind manufacturers.
According to the World Steel Association’s most recent data, the start of 2025 has seen a year-on-year decrease in global steel production from 2024.
Uncoincidentally, the market is undergoing a period of extreme volatility, most notably making headlines as part of President Trump’s tariffs.
On 12 March, a 25% tariff on US imports of steel, aluminium and other derivative products went into effect. Both the EU and Canada announced retaliatory tariffs of 25% each, but the EU’s plans have since been paused until July.
At the nexus of the trade war and the use of steel as a bargaining chip is China, which dominates both global steel production and wind power manufacturing as a whole, undercutting global competition with cheap and heavily subsidised exports in what the Centre for Strategic and International Studies (CSIS) calls “the Chinese overcapacity problem”.
China’s dominance is nothing new in the wind industry, but the tariffs on steel have brought into sharper focus the need for supply chain diversification as a shield against geopolitical stressors.
“China is a powerhouse nobody can get around, but it’s not about pitting countries or regions against each other,” explains Markus Zeitzen, wind energy service provider Det Norske Veritas (DNV) ESG senior business development manager. “Selecting two or three suppliers from different areas can give you resilience in your supply chain through competition.”
Speaking to Power Technology alongside Zeitzen, DNV global head of sustainability and ESG services Christopher Lilholm adds that “it is increasingly important to look at the sustainability performance of the steel that goes into the turbines”.
Indeed, low-carbon steel, also known as ‘green steel’, has become another consideration for wind turbine manufacturers looking to reduce their emissions. It is produced through technologies such as direct reduced iron, electric furnaces and green hydrogen.
While these developments are necessary to address the emissions-intensive production process of steel, this inevitably adds additional costs and complications in the supply chain, particularly as there are currently no universal standards for green steel.
“Even steelmakers find it hard to label their products correctly,” says Lilholm. “So, for a turbine maker to navigate communicating that to clients is not easy, but it will be essential.”
Alternative materials to steel continue to gain traction, such as wood, which is attractive both for its superior sustainability and widespread availability. Since securing an EU grant of Skr69m ($7.3m) in 2020, Swedish start-up Modvion has been developing wooden turbine towers that can reach taller heights than steel equivalents due to less material being required.
However, steel is only one branch of the turbine supply chain that manufacturers must negotiate.
Fibreglass in wind turbines
Fibreglass is a key component in turbine blades, nacelles and hub covers and is arguably the strongest tier of the turbine supply chain.
According to industry association Glass Fibre Europe, due to the material’s raw mineral components, which include silica sand, kaolin clay, limestone and dolomite, “there is no risk of supply shortages or over-reliance on concentrated sources”.
However, fibreglass also faces excess capacities from Chinese producers. On 19 March, the EU imposed anti-dumping duties of between 26.3% and 56.1% on imports of glass fibre yarns from China, citing the importance of the material in the EU’s “clean tech supply chains” and green transition.
For World Wind Energy Association secretary-general Stefan Gsänger, the main challenge in fibreglass supply for wind energy is “recyclability and how fast the recycled material can re-enter the market”.
The life cycles of fibreglass and the epoxy resins that coat turbine blades remain a sticking point for the wind industry’s environmental footprint. The complex layers in the chemical compounds are difficult to separate, leading to landfilling and resource waste.
Several wind turbine manufacturers are exploring the possibilities of recycling fibreglass to further boost supply chain resilience.
US-based Carbon Rivers uses pyrolysis technology to recover glass fibre that can be remelted, closing the material loop and securing supply for manufacturers while reducing dependence on volatile material prices. Wind giants such as Ørsted and ENGIE have also successfully recycled turbine blades from specific projects, but this has yet to be achieved at scale across the industry.
Wind Europe senior supply chain analyst Lizet Ramirez confirms that “alternative technologies and materials require a big push to be ready on the scale that we need them”.
“Quality assurance is also essential in recovering and reintroducing materials,” she adds.
Another consideration is the impact of the innovation race on supply and demand, as Zeitzen explains. “Over the last few years, turbine components have gotten bigger, but if you innovate constantly, you overburden your supply chain, as well as research and development and asset lifespan. We are seeing several turbo manufacturers slow down for security,” he says.
REEs and the future of turbine supply chains
Out of the 17 classified REEs, four are primarily used in wind turbines: neodymium, praseodymium, dysprosium and terbium. These are essential in producing neodymium–iron–boron permanent magnets that generate electricity and maintain the integrity of a turbine’s walls.
China dominates this supply chain too, controlling 60% of global REE mined production and roughly 90% of global processing output. Ramirez confirms that “there is a near total reliance on China for permanent magnets and limited alternative supply routes available”.
In December 2023, China initiated an export ban on separation and extraction technologies for manufacturing permanent magnets, which has escalated to export controls on seven REEs, announced in April this year.
The impact of this on REE supply chains for wind turbine manufacturing has yet to become clear given the to-and-from nature of the US-China trade war, but Ramirez highlights global shifts towards proactive and preventative supply chain risk management.
“For example, the EU is investing in innovations to secure critical raw materials. From the recently announced 47 strategic projects, five are dedicated to REEs and permanent magnets. This is good news for the wind industry in making the most of domestic resources and building new partnerships,” she confirms.
With such policy support, near-sourcing key materials can become more of a reality for turbine manufacturers outside of China’s monopoly, which also covers copper and aluminium.
However, Lilholm points out that competition for access is the ultimate issue: “Do wind developers have the economic gravity to purchase supplies over other sectors?”
Investment in diversified materials and supply chains is pivotal – especially as high demand for materials from major industries such as construction and automotives relegates wind turbine manufacturing to relative unimportance in times of strained supply.
Gsänger identifies solar energy’s “amazing” development and supply chain as a model for the wind industry to look to, adding that “we need the markets because supply chains and manufacturing follow where the markets are”.
“This is really where the wind industry needs to grow up,” asserts Zeitzen. “It is time to look deep into the entire supply chain.”