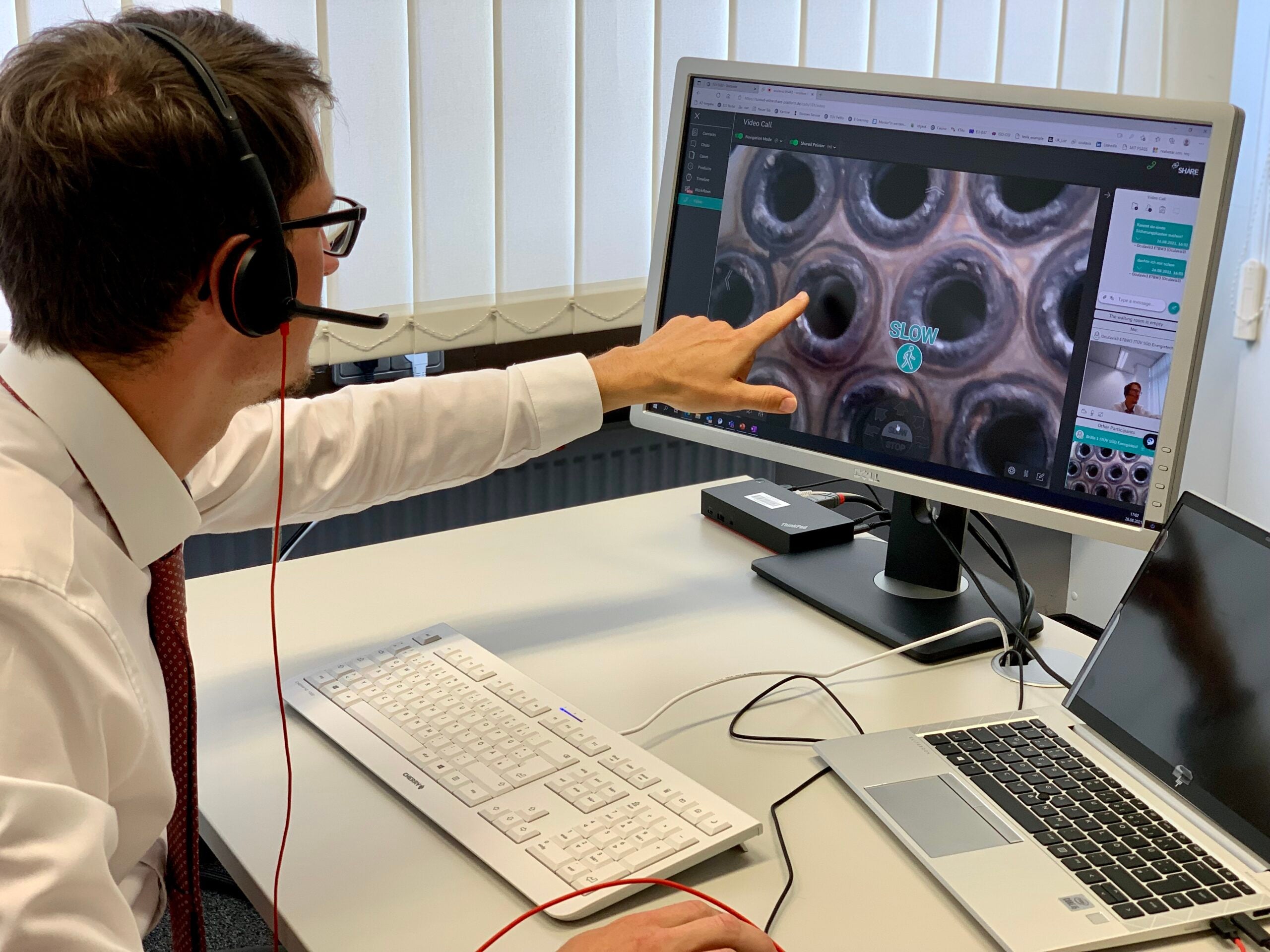
Nuclear power has a reputation as an energy source in need of constant monitoring and maintenance, to ensure that operations run smoothly, and both workers and those around the plant stay safe. While it remains an open question as to whether nuclear power deserves this reputation, there is one particular benefit that comes from additional safety oversight in the sector: the nuclear industry is something of a hotbed of innovation in safety and monitoring devices.
One of the latest is a joint project by US-based RealWear and German technology firm TÜV SÜD to bring assisted reality (AR) to the nuclear industry. The former has deployed more than 100 of its HMT-1 devices at TÜV SÜD’s business lines including automotive and oil and gas, head-mounted cameras that enable a worker to broadcast their point of view to distant inspectors and experts to aid in the inspection of equipment that is later installed at nuclear power plants.
RealWear is justifiably proud of its work, claiming that by eliminating the need for inspectors to travel to various nuclear plants around Europe alone, the project has saved 11 hours of travel time and around $4,390 per flight, to say nothing of the environmental benefits of cutting down on plane travel.
With much of the world still in a state of limbo amid the Covid-19 pandemic, could these AR glasses be the perfect solution to ensuring the robust monitoring of one of the power industry’s biggest sectors?
Remote benefits
“Due to the Covid-19 pandemic, we are not allowed to travel from our company [and we’re] not allowed to enter Japan,” says Christoph Gatzen, head of inspection at TÜV SÜD, discussing how the pandemic had impeded his ability to conduct his work across international borders.
“We decided to send these AR glasses down to Japan, where we also have a local legal entity from TÜV SÜD,” he continues. “My colleague from trips to Japan [was then] in the high-voltage laboratory, where the transformers were located, and he was doing the tests. Our expert was connected remotely and guided him through these different test cases.”
Examples such as these illustrate the benefits of the technology amid the current climate of closed borders and limited international travel, but these are advantages that will persist long after the pandemic subsides.
The ability for inspectors to monitor and assess nuclear plants around the world, regardless of their location and without having to travel in person, could dramatically improve the efficiency of the monitoring process, and help bring a sense of shared expertise and operational unity to the nuclear industry.
Beyond logistics, there are additional benefits for individual employees, especially if the technology is ever adapted for use inside nuclear plants themselves.
“One of the main principles of a nuclear power plant is to minimise the workers’ [exposure] so the workers get as little radiation as possible,” explains Katarína Balcová, marketing manager at TÜV SÜD. “So if you, for example, can minimise the number of people going into this area set-up that is also a huge, huge thing for the whole industry.”
Gatzen continues: “You can also use it for training purposes, [which] is something you can use outside these nuclear power plants in the training centre. To do these real tour trainings, how to make tests and how to use the different tools, that’s one advantage of these AR glasses; you have those hands free for working.”
This is particularly important considering the world’s big plans for nuclear development. According to the World Nuclear Association, around 55 reactors are currently under construction, and should they all be completed, the total number of reactors in the world will increase by around 10%.
Figures from the International Energy Agency put the expected growth in nuclear capacity between 2020 and 2050 at over 26%, and all of these new facilities and projects will benefit from easier access to inspection and monitoring.
Collaboration in technology and operations
The use of AR glasses could also be just the start of a wave of collaboration and flexibility in the inspection sector, if not the nuclear industry more broadly.
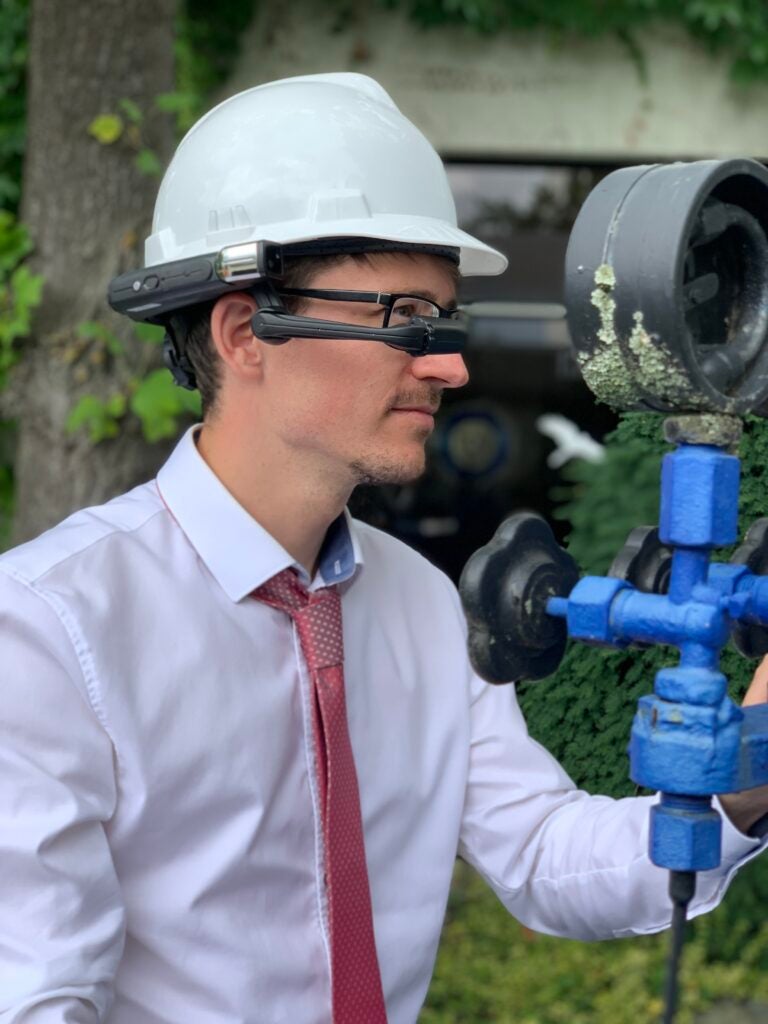
“In the past, we have also heard of one possibility [for] use, I would say something before AR glasses,” he says. “We have had a small submarine … to make inside inspections. But they are cable driven, not radio-controlled. So that’s something completely new, and we are also looking to use these AR glasses in different kinds of contracts and possibilities.”
Flexible approaches such as these could also help the nuclear industry overcome some of its most well-established challenges, such as the risks posed to workers’ health.
“If you know the nuclear business and also nuclear power plants, they’re very safe and highly-regulated plants so it’s not so easy to go inside,” says Gatzen. “And we also have some physical restrictions; if you have a look inside such a power plant, because you are covered by a metal cage there’s no possibility to use these remote or radio-controlled possibilities.
“So, we are using this remote inspection before installing in the nuclear power plant production process, and also after the phase out of these power plants, we can use also these AR glasses to make the documentation and inspection of the different steps of decommissioning.”
The reference to the use of the glasses beyond mere inspection, and for use in areas such as decommissioning, highlights one of the less obvious benefits of an approach such as this. By integrating a new form of technology into an industry that has historically been hesitant to embrace change, the work of RealWear and TÜV SÜD could help establish a precedent of flexible working and collaboration in the nuclear sector.
“I would say in future we will have a combination of these new technology, but I’m sure it’s not that you can exchange these behaviours with 100% new technology,” says Gatzen, highlighting how the nuclear industry could be best served by a range of processes.
“You will always have some people going on-site and [be] asked to have an expert on-site. It is not possible to do everything with these glasses, because your view is very restricted and sometimes you must also have the possibility to see the surroundings and the environment of the component. I think it’s like it’s a hybrid version.”
Balcová echoes this idea, pointing out that change may be gradual, but that with projects such as these, it is certainly underway.
“For now, it’s being implemented at the component side, so [for] the manufacturers of the components that is not a problem at all to inspect their factories or how they are creating the components,” she says. “But as Christoph said, inside of nuclear power plants, for that we will need some time.”
Overcoming challenges in nuclear inspection
Of course, a precedent for flexibility can only be set in an industry that is, in its current state, somewhat rigid. Considering both the reputation of nuclear power from disasters such as the Fukushima disaster, to more recent events such as Russia’ invasion of Ukraine and occupation of nuclear facilities, there are concerns regarding what both maliciousness and misfortune in the nuclear industry could do to public safety.
“The new technology takes a lot of time to implement in the nuclear business because of the sensibility of the technology and also the sensibility of the people,” explains Gatzen, highlighting how decision-makers across the sector are justifiably uneasy with change when the potential for destruction is so high. “If you are talking about nuclear businesses, it’s an old-fashioned business.”
Balcová also notes disadvantages with the technology, those of familiarity with the glasses, or lack thereof. As is the case with any new technological process, considerable training and practice will be needed for the sector’s workers to make best use of the devices.
“Perhaps one of the drawbacks also would be a more human factor, I would say, and something that can be overcome with training, is [that] those people need to be trained properly how to use [the glasses],” she says.
“For example, if they move their head way too fast or something like that, the people on the other side can get nausea, so when they have multiple experts joining the inspection remotely, they just need to be really considerate about not speaking all at the same time so as not to confuse the inspector that is outside.
“But that is something that has not that much to do with technology, it’s just something that needs to be overcome with training.”
Yet Balcová is right in pointing out that a lack of familiarity can be remedied by training, a sentiment which is true for many aspects of the AR glasses. Any new technology is strange and unfamiliar when first deployed, but over time, and through practice, workers across the sector are more likely to become comfortable with it, from individuals entering nuclear facilities to inspectors seeing through their eyes far away.
In fact, Gatzen notes that this potential for growth could actually be a benefit, rather than a drawback, for the entire project: “It’s difficult to get new employees, but if you combine these old but important technologies with new technologies, and new possibilities, you’ve got a lot of interested questions from the new employees. We have more possibilities to make this training for new employees [and] it’s much easier to combine them with different experts.”