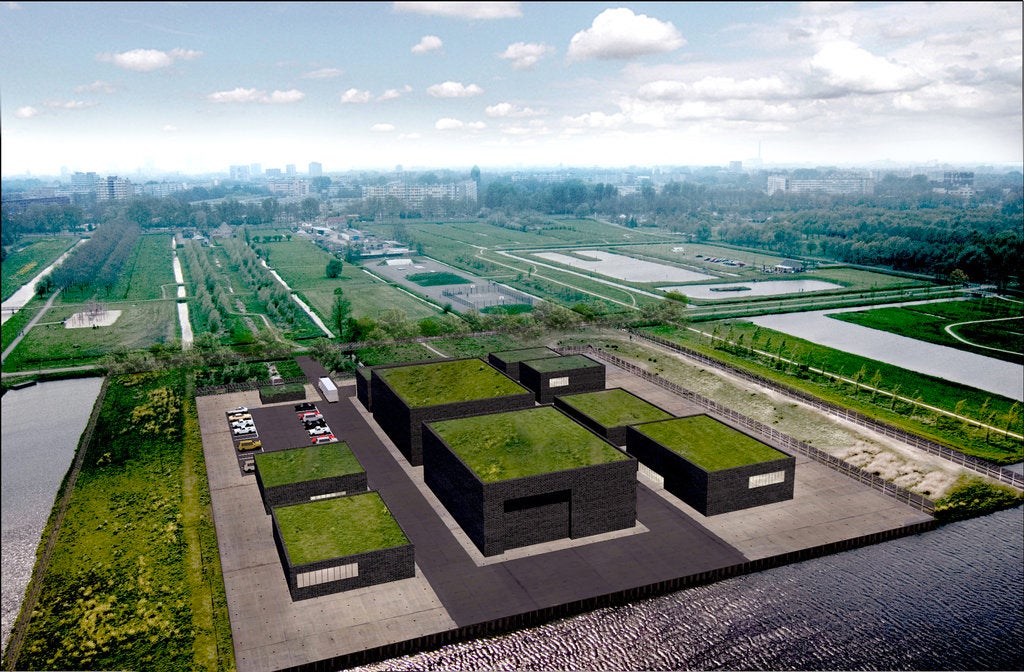
The soaring cost of nuclear power generation, in part due to increased safety regulations, has seen the sector struggle to compete against increasingly cheap renewable energy sources and gas fired power generation.
A potential saviour, however, could come in the form of molten salt reactors, a class of nuclear fission. The technology is considered much safer than traditional nuclear, and as a result, considerably cheaper and more cost competitive. However, despite the concept for the technology being established in the 1950s, a commercial model has yet to be realised.
Leading developer, Moltex Energy, recently received $2.5m in funding from the US Department of Energy, and is gearing up to build its first Moltex Energy Stable Salt Reactor in Canada, with the support of New Brunswick Energy Solutions Corporation and New Brunswick Power. The company says the reactor, once finished around 2030, will prove the commercial viability of its patented technology and help facilitate a clean energy future.
Heidi Vella (HV): How does Moltex Energy’s technology – and molten salt reactors more generally – differ from nuclear reactors in use today?
Rory O’Sullivan (RO): Molten salt reactors can inherently increase the safety performance of nuclear because the fuel is already in a liquid state so the radioactive gases aren’t in the fuel as gases. Therefore, although things can of course go wrong, there is no scenario that would cause a major radioactive release like what happened at Chernobyl.
Even though extremely unlikely, the solid pellets used by current reactors – which are based on technology from the 1950s – could get too hot, have a meltdown and release a lot of radioactivity. Nuclear plants today are some of the safest facilities on the planet, but that comes at a high cost and as the complexity of plants has increased they have become uneconomical.
However, with the enhanced safety advantage provided by molten salt reactors, plant design can be simplified to reduce costs; for example, compared to Hinkley point C our plant will be 15 times smaller.
HV: Moltex Energy is not the only company developing this kind of technology; what makes yours different?
RO: The difference is that typically other molten salt reactors circulate liquid fuel through a system in the plant. This highly radioactive fuel, going through pumps, heat exchangers and pipework etc, is highly corrosive meaning the reactor needs to be replaced after several years. It works, but it costs a lot to replace the reactor.
We’re different because we put liquid fuel in conventional fuel pins; traditionally, reactors have fuel pins a couple of metres long, with lots of small solid pellets in it, but ours uses liquid fuel salt.
Therefore, we now have the big safety advantage of molten salt fuel contained in pins so you don’t have the engineering complexity of circulating a liquid fuel. This means the whole plant design can be simplified and because of the safety benefits, the reactor doesn’t need to be rebuilt every few years. The plant lasts 60 years or longer.
Another advantage of our solution is that we can use conventional nuclear waste fuel instead of burying it. We recycle it in our reactor and the end product is only radioactive for several hundred years, which is significantly shorter than for conventional waste that is radioactive for around 300,000 years. So, we’re also reducing the social issue around nuclear waste.
HV: One of the selling points of Moltex’s technology is it can store thermal energy to operate alongside renewables, much like gas, but can it compete with gas on price?
RO: It’s an important question. We’re not really modelling our technology to compete with renewables because the future grid will be, as we see it, a mixture of renewables and nuclear. We envision 50% renewables and 50% nuclear and not gas, because, if we are to fully decarbonise the energy system, gas is not an option. It’s a temporary fix.
Renewables are getting much cheaper, but they’ll never be cheap enough to provide affordable electricity with energy storage. Therefore, it’s necessary to have nuclear peaking plants to sustain the energy supply during the periods where there is no sun or no wind.
Our nuclear power plant provides thermal storage, not electric storage, which means the cost of our storage today is ten times cheaper than the U S Department of Energy’s lowest potential theoretical cost for electricity storage. So even though battery storage is going to get cheaper and become bigger, it is never, ever going to be affordable to have an entirely renewable and storage grid.
Whereas, we can produce heat from our reactor, which is stored in tanks of molten salt. So, for example, if we have 1,000MW plant, we can store the energy for 16 hours, and for eight hours a day we can run 3,000MW.
Our cost estimates for a 1,000MW plant is $2,000 per kilowatt (/kW), which is cheaper than the capital cost of coal. A 3,000MW power plant with increased storage and turbines for the peaking capability, increases the costs to $3,000/kW, but the costs are divided between three so is about $1,000/kW.
That is comparative with gas from capital cost, and the nuclear fuel cost is almost free, or at most 5-10% of costs, whereas the cost of gas is about 80% of expenditure costs.
HV: What are Moltex’s main hurdles to commercialisation then?
RO: Presently, the biggest challenge is getting the finance to complete the R&D and design. Once that is done the cost of construction will be more straightforward, because we will have all the information we need to build it.
We have raised about $10-15m so far but need $50-70m more in the next three years. Ultimately, we think this will come from a mixture of government funding and private investment.
It’s challenging because for typical venture capital investors who would normally invest in early stage technology, our time frames for deployment are too long. Additionally, governments have been so restrictive in the nuclear sector, it’s scared investors away; that’s why we have to rely on government funding.
But governments have to stand-up now and actually help if they want this technology. We are waiting for the UK government to make a move, but they have been slow. There was an article in The Times that said [UK Prime Minister] Boris Johnson will be announcing £500m towards small modular reactors in the North of England, so we’re hopeful.
However, our concern is that the funding could go primarily to small modular reactors that are based on existing solid fuel technologies. They are going to be ready a year or two earlier than us and have lower investor risk because it’s more traditional technology. But the technology is not going to achieve the same cost reduction as ours and doesn’t have storage and flexibility or reuse nuclear waste. It’s a distraction for the government, but it is not going to deliver the results they are expecting.
HV: What’s next for Moltex Energy?
RO: Along with finance, the next stage will be bringing in other partners, construction and design engineering firms to support us. We will do most of our validation to see if it works while the reactor is offline; nuclear is so heavily regulated, we need to know all the answers before we can even contemplate building an actual nuclear power plant.
Then we will build the actual reactor, which will be both a final test and a commercially operating reactor. That will validate all the technology so we can build more.
The timeframe will be ten years for the plant to be built – three years for the early design, three years detailed construction drawings and licencing and planning, and then roughly two-three years to build.
Internationally and in the UK, we’re looking at other customers, other utilities to build plants with and we’re already getting interest. Eventually, we see hundreds, if not thousands, of plants being built in the next 20-30 years.