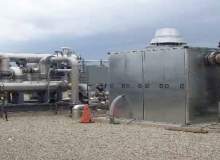
Because of the varied wastes in landfill, actual gas production is difficult to predict and control. Emissions regulations and the costs of meeting them depend strongly on plant location. Emissions regulations in Europe and (for example) California are strict and systems need to have 100% uptime.
Careful plant operation and maintenance is essential, particularly for older wellfields. Monitoring has to meet local and government regulations, and must continue for years after a project has been closed.
Successful operation depends on good design
Problems should be prevented by design. Wells and collection pipes need balancing, with enough pipes to extract the gas. Economic success depends on accurate recovery projections, a good power purchase agreement, relatively high natural gas prices, with subsidies and tax credits where available.
Landfill gas is around 50% methane and 45% CO2, although perimeter or sideslope wells may have lower methane content. Projects can meet on-site heating and electrical loads, be fed into fed into pipelines or export electrical power to the grid.
Then, the demand side of the meter generally needs only protective relays and disconnect devices but SCS Engineers has, in the US, seen widely varying costs on the utility side – from $50/kW to $250/kW. Alternative uses can include vehicle fuel, particularly if the operator or potential customer has a large vehicle fleet.
Plants often need to be expanded as LGE cells are filled, but gas recovery projections must again be accurate. Over-projection of recoverable gas will mean that the plant won’t work at full capacity and won’t repay investments.
"Most LFG recovery modelling uses a first-order model (production peaks shortly after initial waste placement and then decays exponentially), but site-specific coefficients must be accurate and are difficult to calculate accurately," remarks Jeffrey L. Pierce, VP of SCS Engineers. He stresses that a site’s flow meter accuracy needs to be verified, along with a review of wellfield operating practices and a thorough review of historic data. "Going only on a ‘desktop’ analysis isn’t enough."
Careful leachate monitoring can help prevent pollution
Landfills can produce several million gallons of leachate a year, and this can contain a variety of pollutants, depending on the material buried.
Bottom liners and collection systems need monitoring to prevent ground and surface water pollution. Subsurface monitoring wells need to test for landfill-related chemicals both upstream and downstream of the landfill. Storm water and erosion control systems need regular checking to prevent heavy rains causing water run-off into streams and rivers.
Odours should be reduced by keeping the exposed waste area as small as possible, covering highly odorous waste immediately and placing daily soil cover. Dust can come from trucks driving over unpaved routes, from dumping the landfill itself and from processing. Water trucks may be needed to suppress dust during dry periods.
Sites should prevent the escape of litter, with litter fences and daily litter pickups. They should minimise noise, too. Heavy equipment needs maintaining, and must only work within permitted operating hours. Barriers can help deflect noise, and operators may need instructions to close doors and tailgates quietly.
Monitor emissions at source to improve maintenance
Five regions are often monitored for gas: in soil, near surface, emissions, ambient air and indoor air. Pressures and water levels within the landfill can influence measurements. If atmospheric pressure is higher than landfill pressure, measurements will be inaccurate, while water in a soil gas well can prevent gas movement and detection.
Portable monitors can perform initial screenings of gas migration pathways and identify the source of methane leaks. Gas monitoring probes then need to be installed along the perimeter of the site and gas routinely sampled. Gas migrating underground to surrounding buildings can risk explosions or asphyxiation. Emissions should ideally be controlled at source – the landfill itself.
Besides combustion gases (NOx, CO, CO2, SO2), the UK’s Environment Agency lists important emissions as total particulate matter, heavy metals (As, Cd, Cr, Cu, Hg, Mn, Ni, Pb, Sn and Zn), total volatile organic compounds (VOCs), dioxins and furans (PCDDs and PCDFs), polycyclic aromatic hydrocarbons (PAHs), hydrogen sulphide (H2S), halide gases (HCl, HF), nitric acid (HNO3) and speciated organic compounds.
Monitoring techniques include organic vapour analyser-flame ionisation detectors (OVA/FID) and Fourier-transform infrared-red (FTIR). Regular grab sampling or continuous monitoring can detect long-term changes in composition. Continuous monitors often measure only one pollutant, however, and laboratory analysis can periodically check concentrations of a wider range of pollutants.
Volume and composition of gas will vary over time, so there is a need for effective gas management and engine control systems. Best available control technology (BACT) should be installed for flares, boilers, engines and turbines. Control charting energy production can also show up gas production problems.
Protect sensitive engine components from corrosive gases
Repairs to the site itself can be expensive, highlighting the importance of getting the initial design right. Deteriorating gas wells may need to be replaced. Leachate escape to neighbouring drinking water wells can mean that these need to be replaced with deeper wells.
Engines and turbines are particularly sensitive to pollutants. Collection and pre-treatment systems for removing moisture and particulates must be properly maintained. Preventive maintenance avoids unscheduled downtime, although maintenance schedules can be difficult to predict.
That is particularly true early in the plant’s life, with variable production of uncertain gas compensation. Regular maintenance repays by maximising efficiency and engine life, with unmanned sites needing remote condition monitoring.
These are usually gas turbines, dual-fuel (compression ignition) engines or modified lean-burn spark ignition gas engines. Many factors affect operating profiles and efficiencies. They include physical and chemical characteristics of the waste itself, gas management systems and site characteristics (age and remaining capacity).
Caterpillar points to four categories of corrosive contaminants: sulphur, halide, acid and silicon compounds. Gas engines need a corrosion resistant core and fuel system for low inlet fuel pressure. Jacket water temperatures need to be kept above 100°C to protect internal engine components from corrosion by preventing steam condensation.
Crankcase ventilation should remove any blow-by gases with fuel borne contaminants from the engine crankcase to prevent condensation and corrosion and extend oil life. Engine oil should be analysed for chemical content weekly. Monitoring shows when oil needs changing and when there is wear on engine components.
Paul Ervin of Biostream draws a direct relationship between gas quality and engine wear. "Although oils like Mobil’s Pegasus 605 are designed for fuels containing corrosive materials, in themselves they do not prevent engine wear. Oil analysis is essential but the results must be acted on. Management should be notified when limits are triggered, for example if the oil analysis shows high iron content or low oil total base number, with recommendations to correct."
Monitoring and preventative maintenance programmes should look at things like engine hours, maintenance records, oil and gas analyses and general site conditions. Critical maintenance activities (top end, bottom end and mid frame overhauls and gas train maintenance) in particular need strict quality control.
Ervin recommends that operators build a simplified oil analysis database. Data collection, too, needs to be simple, as do operating and maintenance procedures themselves. "Simplify, simplify, simplify," he stresses.
Landfill gas – (hopefully) facing a long-term decline
For the future, advanced gasification and fuel cells promise to double efficiencies while reducing air pollution and waste ash. Fuel cells are progressing rapidly, spurred by higher fossil fuel prices and incentives for reducing carbon emissions. Commercial versions of phosphoric acid fuel cells (PAFC) are already available.
The long-term trend, however, is to divert biodegradable municipal waste away from landfills, and this will reduce the potential for methane generation. In the US, the EPA estimates that landfill gas has fallen since 1990 from the second to third largest source of man-made methane emissions (after natural gas systems and animal-related emissions).
The "reduce, reuse, recycle" principle applies. Although landfill gas should be collected wherever possible, it is not actually a renewable resource. In the long term, landfill itself should be avoided.
Related content
Waste to energy in the UK – Tilbury’s milestone
Green energy proponents in the UK recently celebrated the milestone of achieving a one million ton food waste milestone, with more than one million tons of organic waste being processed into energy annually.
CCS: carbon emission saviour or dangerous earth shaker?
Carbon capture and storage is currently touted as a viable strategy for reducing the environmental impact of CO2 emissions, but recent research suggests there could be more problems than previously realised.