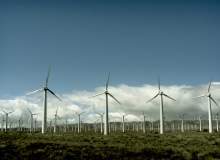
Power Plant O&M Costs and Industry Trends
Whether the energy source is fossil fuel-based, nuclear or renewable, the cost of operation and maintenance (O&M) forms an important part of a power plant’s business case, a piece of the investment puzzle along with capital expenditure and fuel costs that must be balanced against life-cycle profitability, output efficiency and availability. These ongoing costs – both fixed and variable – include day-to-day preventative and corrective maintenance, labour costs, asset and site management, maintaining health and safety, and a host of other important tasks.
O&M costs vary widely between different forms of power generation, and the O&M burden often plays a varying role in the basic cost analysis of different power plants – high maintenance costs are often offset by advantages in other areas, and vice versa. Here we present the average O&M costs for six of the most common power generation methods while exploring the reasons for those costs and how they fit into the wider landscape of power plant economics.
The basis for this analysis is data taken from the International Energy Agency’s (IEA) World Energy Investment Outlook 2014, which includes raw information on average yearly O&M costs in the power industry, both currently and in the future. The IEA’s future cost predictions are based on its so-called New Policies Scenario (NPS), which incorporates countries’ announced policy commitments and plans in its projections. Current costs are taken from 2012 data, with projections given for 2020 and 2035. As the IEA’s O&M data is split between different countries and regions, we have taken the data for Europe as the default comparison point between power generation methods.
Gas turbine ($20 per kW)
Gas-fired power generation is known for having relatively low O&M costs when compared to other generation methods, and the IEA’s stats bear this out. Power plants equipped with simple-cycle combustion turbines, the most common – and least efficient – gas-fired technology, have reached an average annual O&M cost of just $20 per kilowatt (kW) produced, making this technology the cheapest O&M option in the industry.
According to the IEA’s figures, more sophisticated gas plants also benefit from favourable economics in this sense – combined-cycle gas turbine (CCGT) technology can boost efficiency from 39% with simple turbines to 60% at an average O&M cost of $25 per kW, while the cogeneration achieved by CCGT plants with combined heat and power (CHP) pushes efficiency to more than 80% for a similarly modest rise in O&M cost.
The upkeep of an effective lubrication system for gas turbines is a major consideration for gas-fired plants as a preventative maintenance measure, and forms a vital component of their O&M spending. In a wider sense, as renewables become a larger part of developed economies’ energy mix, gas-fired plants, with their ability to quickly ramp output up or down as needed, are becoming more important as a reliable and variable supplement to intermittent renewable supply. This growing requirement makes flexible generation a paramount concern, and the strain caused by frequent starts and stops will likely drive gas-fired O&M costs as renewables take control of a growing portion of the energy supply mix.
Large-scale solar photovoltaic ($25 per kW)
It’s a testament to the ongoing development of solar photovoltaic (PV) technology that, at $25 per kW, large-scale PV installations are among the cheapest power generation technologies for O&M. Of course, the relative simplicity of solar PV is the defining factor here – cleaning and removing debris from PV cells along with careful monitoring of inverter units and AC subsystems are the primary maintenance tasks. The IEA also projects steeply falling initial capital costs for these projects up until 2035, meaning that solar PV is rapidly catching up with fossil fuels as an enticing financial proposition as well as an environmentally responsible one.
Concentrated solar power (CSP), on the other hand, is a more sophisticated and novel technology that has not yet benefited from the collective build-up of research and development that is driving down costs for solar PV. With sky-high capital costs and an O&M burden of $290 per kW in Europe, CSP is currently incredibly expensive to run and maintain, but economies of scale, more resilient materials and declining component costs are expected to bring a significant O&M cost decline in the coming decades; the IEA expects O&M at CSP plants to be $183 per kW by 2035.
Subcritical coal power ($43 per kW)
Coal has long been the workhorse of the power generation market. It may be in the twilight of its reign as environmental policymakers look to limit their reliance on coal-fired power, but its strong all-round financial characteristics will make coal economically competitive in the absence of high costs for carbon emissions or skyrocketing coal prices. O&M costs aren’t spectacularly low for coal, with the cheapest subcritical plants coming in at $43 per kW, the cost rising steadily through the more efficient supercritical and modern ultrasupercritical coal combustion technologies before arriving at $88 per kW in the case of the less-polluting and carbon capture-ready integrated gasification combined cycle (IGCC) plants.
A major driver for O&M costs at coal-fired plants is monitoring and servicing the many moving parts involved in the generation process, including turbines and generating sets, coal yard conveyors and handling systems. As coal power stations are often baseload plants, these components are often expected to operate continuously while being subjected to heavy loads and high temperatures, as well as varying levels of dust, dirt and moisture. Innovations in predictive maintenance and asset optimisation have helped bring down costs over the years, but O&M expenditure in this highly mature sector of the industry is now expected to remain stable through to 2035.
Onshore wind power ($46 per kW)
Access is the predominant issue for wind turbine O&M, as the stark disparity between costs for onshore and offshore wind farms demonstrates. Operation and maintenance costs at onshore wind power sites now rival the simplest coal technologies at $46 per kW, and are expected to fall below the coal O&M price by 2020. Their offshore counterparts, which are also vastly more capital-intensive to build, are currently sitting at $181, nearly four times the expense.
Automated off-site equipment monitoring methods are becoming increasingly important as a cost and time-effective maintenance strategy, especially offshore, where gaining access to turbines for repair or modification works is an expensive operation in itself. Siemens has installed the WebWPS SCADA remote monitoring system on all of its modern wind turbines. “On average, our specialists resolve 80% of [turbine] events remotely within ten minutes, without a technician needing to visit the site for further inspection,” the head of Siemens Energy’s Diagnostic Centre Merete Hoe told Future Power Technology in 2012.
Large-scale hydropower ($53 per kW)
Large-scale hydroelectric power is currently significantly cheaper to operate and maintain than smaller-scale projects; the former has an average yearly O&M cost of $53 per kW with the latter slightly higher at $70. Unusually, however, the cost for maintaining large installations like dams and barrages is predicted to rise rather than fall in the future, drawing nearly even with the stable costs of small-scale hydro by 2035.
Ageing equipment in need of replacement at long-established hydroelectric dams, as well as the complexity of running and maintaining new equipment alongside older components may partly explain the gradual increase predicted by the IEA. American Hydro Corporation chief hydraulic engineer Gerry Russell offered another explanation in 2010: “Market conditions…are testing the limits of operation for many hydro generating facilities. Generation equipment now is being operated routinely in regimes that traditionally would have been considered outside of design limits and appropriate only for transitional or possibly emergency conditions. These new requirements are increasing the level of operation and maintenance capabilities and costs for many plants.”
Nuclear power ($198 per kW)
As well as representing a hefty capital commitment to build, nuclear power plants are not cheap to operate and maintain. For every kilowatt generated there is an average of $198 spent on O&M in Europe, with every other region bar China (consistently the cheapest country for power plant O&M costs) recording costs of over $100. Even China’s $80 per kW is expected to spike to $112 by 2020.
The processing, enrichment and fabrication of uranium into fuel elements represents a significant expense, not to mention the cost of waste disposal. Ensuring the integrity of equipment is also a major task, with nuclear plants operating with a large number of pumps, valves, cables, circuit breakers and a host of other mechanical and electrical components that must work under tough conditions.
Of course, the repercussions for safety failures are particularly catastrophic in the case of nuclear power, so ongoing risk management is essential and there is justifiably a high bar set for safety standards. Despite these significant O&M costs, nuclear energy’s other advantages – reliability, lack of carbon emissions, low fuel prices – will likely see the technology continue to play a major part in the energy mix of the future, especially as reactor technology improves and the psychic scars created by Fukushima begin to heal.