
From body movements to bumping backpacks, there is a pool of energy generated in our daily lives which is just waiting to be tapped. The piezoelectric effect, where mechanical strain is converted to small measures of electric current, has attracted funding from the US Government’s military research body DARPA, which is using it to develop energy-harvesting boots, while a similar technology has been installed in Japanese station walkways to garner power from footfall.
In the mainstream, research has stayed relatively confined to highly efficient ceramic applications. Now, a new project to develop 3D fibre structures could open up a whole new range of opportunities by making the technology more flexible, and more importantly, comfortable. Dr Navneet Soin of the University of Bolton’s Institute of Materials Research and Innovation explains what prompted the project and what it means for fabrics of the future.
Adam Leach: What initially prompted you to research the power-harnessing potential of 3D textile structures?
Dr. Navneet Soin: The existing piezoelectric devices and architectures do not take into account that the harvester should be imperceptible to the user and for wearable technologies should be comfortable. Moreover, the need for it to be low-cost, environmentally friendly and recyclable cannot be stressed enough. Based on the university’s rich heritage and knowhow in textiles and materials, the team at the University of Bolton has devised this unique 3D textile structure which brings together the piezoelectric properties of PVDF [polyvinylidene difluoride] fibres into a structure which is highly flexible, breathable, resilient and readily available for commercial exploitation via FibrLec Ltd.
AL: Can you explain how the textiles could be used to generate energy?
NS: In our case, the 3D spacer fabric is composed of two separate conducting textile faces of silver-coated polyamide, which are joined together/separated by the piezoelectric PVDF spacer yarn. Whenever the fabric structure is compressed, say during walking, the impact is passed onto the inter-connecting PVDF yarn, which produces a charge that is collected via the two metallic faces of the fabric. Thus, only a single cohesive structure is required for the production of piezoelectric charges and its collection, eliminating the need for further metallisation to make electrodes.
The holy grail of ignition remains elusive, but each step brings the world closer to limitless nuclear energy.
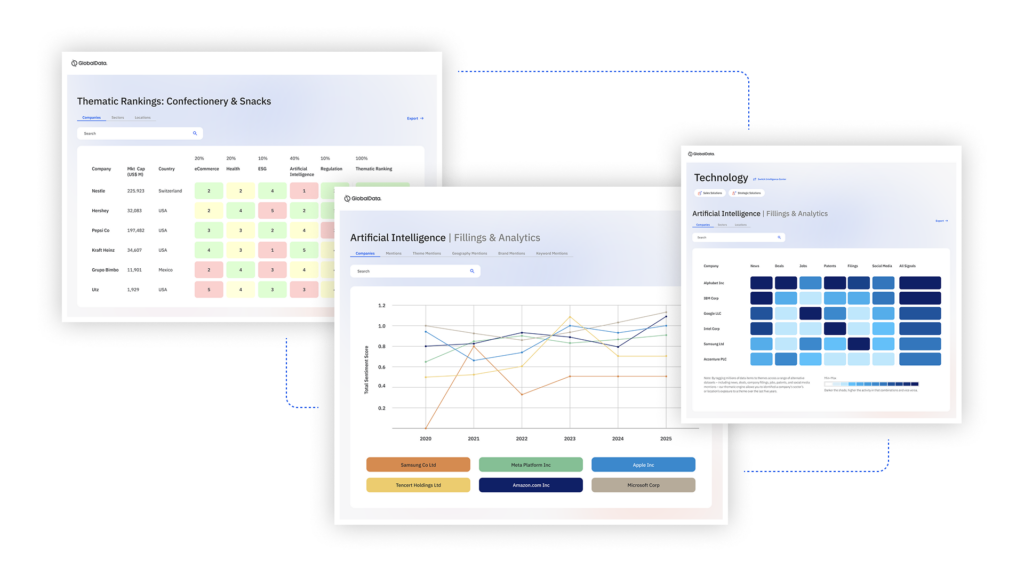
US Tariffs are shifting - will you react or anticipate?
Don’t let policy changes catch you off guard. Stay proactive with real-time data and expert analysis.
By GlobalDataAL: What was the main finding of the research?
NS: The knitted single-structure piezoelectric generator consists of high beta-phase (~80%) piezoelectric PVDF monofilaments as the spacer yarn interconnected between silver-coated polyamide multifilament yarn layers acting as the top and bottom electrodes. The novel and unique textile structure provides an output power density in the range of 1.10 – 5.10 µWcm-2 at applied impact pressures in the range of 0.02 – 0.10MPa, thus providing significantly higher power outputs and efficiencies over the existing 2D woven and nonwoven piezoelectric structures.
AL: What previous research areas did you draw inspiration from?
NS: 3D spacer technology has been used extensively in applications from medical textiles like anti-decubitus blankets to highly breathable sportswear. However, there are no reports of the use of 3D textiles for piezoelectric energy harvesting. In the past, we have developed significant intellectual property in the area of continuous production of piezoelectric fibres, which we wanted to exploit.
Initially, we had trialled these piezoelectric fibres in regular 2D structures but soon realised that the addition of the metallic electrodes for charge collection is a limiting step in their use as wearable energy harvesting materials. To address this, we devised the 3D structure with integrated metallic electrodes made of silver-coated PA66 [polyamide 66] and then knitting the PVDF along with it to make a single integrated 3D textile structure.
AL: How could the energy be stored?
NS: We are currently exploring the use of storing this power output using dedicated electronics into small supercapacitors or batteries and using them offline for charging devices. However, if the application is suitable for low-power transfer such as transmission of some signal using wireless transmission then on-line applications can also be considered.
AL: What challenges did you encounter?
NS: The initial designing of the 3D piezoelectric textile structure itself was the most challenging part as there was no existing knowledge in the area to guide us and we had a limited idea of how the fabric would perform and behave. Also, in order to produce a significant amount of PVDF fibre for the knitting process, the melt-extrusion setup had to be scaled up from a lab-scale extruder to pilot plant level, requiring significant time and effort. Beyond that, once we were on the actual specialised knitting machines, we had to make several on-the-spot modifications to the structure to enhance its mechanical properties.
AL: What possible commercial applications might the research enable?
NS: We are currently exploring the use of these 3D piezoelectric fabrics in a variety of applications such as sensors for assisted living, non-invasive health monitoring, and of course for energy harvesting applications for charging small portable devices on the move by using them inside fabrics, shoe insoles, carpets and so on.
AL: How might it be applied to groups of people, for instance could it be used in a carpeted building with high footfall?
Is the government creating the right policy framework to support the sector and help it integrate?
NS: For a carpeted area which sees high footfalls like an airport, shopping mall, railway station concourses or even stadiums for that matter, the amount of energy produced could be significant. A similar project has been undertaken by a commercial energy harvesting company, which uses ceramic piezoelectric material, based tiles in walkways and they envisage enough energy will be produced to power bench lighting and multiple data transfer ports.
AL: In which aspects of the technology do you see room for improvement?
NS: We are currently exploring significant enhancement in the power output of these piezoelectric fibres and fabrics using suitable inorganic and organic additives. We are also looking at the development of suitable low-power electronics for storing and harvesting this energy. Also, further optimisation of the 3D structures and tailoring it for specific applications is an ongoing task.
AL: What will be the main challenges in making it a commercial success?
NS: As is the case with most of the lab to commercial ventures, the challenges involved are in the area of upscaling the technology, financial viability as well as finding the right applications to focus on. Also, the power output needs to be enhanced to make the product’s application commercially viable.
AL: What most excites you about the technology?
NS: We believe that this is just the first step in the creation of true flexible and wearable energy harvesting structures providing the highest level of functionality. We envisage that with continued development in the area, we could be looking at actual commercial harvesters based on this technology in the next four to five years, which are not only suitable for energy harvesting from human movement but from the ambient environment as well. The room for improvement in the technology is tremendous and since textiles are a multi-billion dollar industry the apparent volume where this technology can be used is very significant.