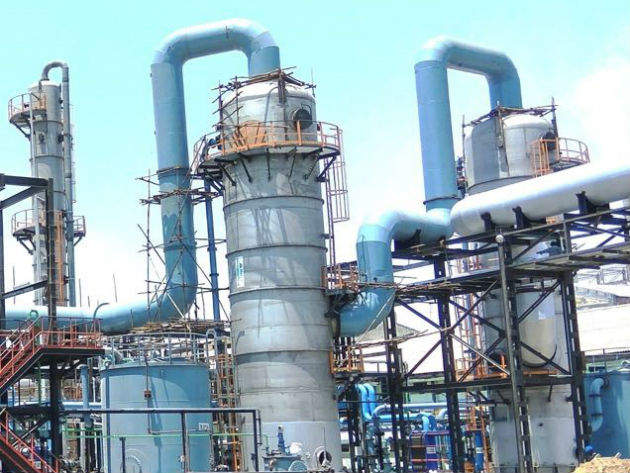
Derided as scientifically unsound and prohibitively expensive, carbon capture and utilisation (CCU) − the process by which carbon dioxide (CO2) is separated from industrial pollutants and converted into commercially viable products – has failed to gain serious traction since trials began 10-15 years ago.
Now however, Carbon Clean Solutions (CCSL), a London-based specialist in carbon separation technology, is set to change all that.
Using a proprietary solvent, CCSL plans to capture 60,000t of CO2 from a 10MW coal-fired power station in Chennai, India. The project, believed to be the first of its kind, captures CO2 at just $30 per ton, significantly lower than the $60-90 typically observed in the global power sector.
The captured CO2 is then used by Tuticorin Alkali Chemicals & Fertilizers (TACL) to produce soda ash, a key raw material in glass manufacturing and detergents industries.
“CCSL has demonstrated that it is possible to capture CO2 from the flue gas off a coal-fired boiler at a cost in India of $30 per ton, but the real breakthrough is that we have been able to capture CO2 at a point where it makes business sense to convert it into a product,” says CEO Aniruddha Sharma.
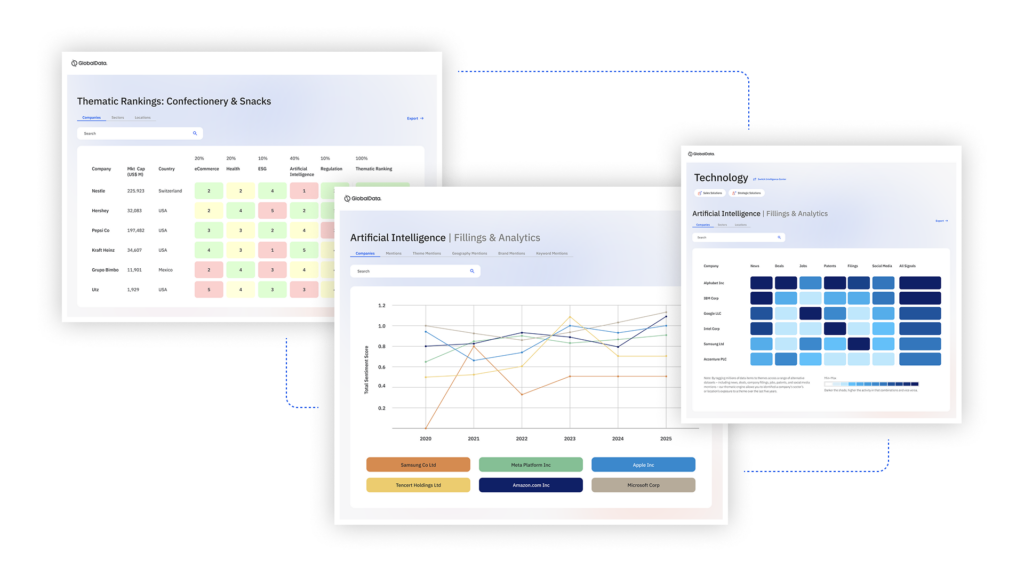
US Tariffs are shifting - will you react or anticipate?
Don’t let policy changes catch you off guard. Stay proactive with real-time data and expert analysis.
By GlobalData“The Chennai experiment is also 100% privately funded, making it one of a kind globally. TACL has secured funding from local Indian banks but there are no subsidies, certificates or grants promised.
“This project is a game-changer. By capturing CO2 cheaply and re-using it efficiently, we believe that there is an opportunity to dramatically accelerate uptake of CCU technology around the world.”
Carbon costs: CCSL solvent reduces expenditure
Removing CO2 from waste gases in line with emissions regulations has the potential to become big business, but proponents of CCU have so far failed to convince sceptics in government and industry.
“Carbon capture has been around in the oil and gas industry for 30 years, but applying the very same technology to remove CO2 from power or chemical plants − for example, flue gases emitted from chimneys or a composition of a biogas or a natural gas − has been very challenging,” says Sharma.
“There are two reasons for this: very high upfront CAPEX and very high ongoing OPEX. At CCSL, we have invented and patented a solvent that is virtually non-corrosive, requires significantly less energy to run and has 10%-15% less oxidative and thermal degradation than traditional chemicals.”
“High-grade 316 stainless steel is used in many power plants, but our non-corrosive solvent means you can build units with carbon steel that is four to five times cheaper; that’s a major CAPEX saving.
“The CCSL solvent requires 30%-50% less energy for running the process compared with a standard amine, reducing OPEX costs by 30%-50%. Finally, because the solvent degrades by 10%-15% less than other amines, the amount ultimately released into the atmosphere is only 10 parts per billion (ppb).
“This has a huge impact on operating costs, not only in terms of reducing the amount of chemicals used during the industrial process but also with costs related to health and safety compliance.”
Cyclic process: the CO2 scrubbing system
CCSL’s claims its new solvent is more efficient at ‘scrubbing’ CO2 from industrial waste gases than traditional amines – ammonia-based chemicals that attract and bind CO2 molecules to their surface.
“The cyclic process involves two cylindrical towers,” explains Sharma. “The first unit is an absorber operated at room temperature. The gas rises upward, the chemical is sprinkled from the top, and the solvent scrubs the CO2 out of the gas in the middle where the gas and the chemical meet. The CO2 is chemically attached to the solvent and then collected at the bottom of the absorbing unit.
“This is then circulated to the second tower, the dissolver, which is heated to 110°C –120°C, breaking the chemical bonds. The solvent loses the CO2, which resumes its gaseous form and is recovered from the top of the dissolver tower. The chemical that has given out the CO2 is collected at the bottom of the dissolver, cooled and circulated back into the first tower, and the process continues.”
The power plant in Chennai went online on 7 October following the successful completion of CCSL’s pilot testing programme at Technology Centre Mongstad in Norway. A joint venture between the Norwegian Government, oil and gas giants Statoil and Shell, and the South African energy company Sasol, it is the world’s largest and most advanced facility for testing and improving CO2 capture.
“Technology Centre Mongstad contains a standard carbon capture plant fitted with a chimney that can be used for flue gases coming out of a combined heat and power (CHP) plant or a refinery,” says Sharma. “CCSL conducted 3,500 hours of testing over six months and captured 25,000t of CO2.
“The tests produced three major results; first, that the CCSL process produces just 10 parts per billion of the solvent in the air. Second, we were able to demonstrate 100% uptime and, finally, an outstanding level of corrosion resistance. This convinced our customer to invest in the project.”
TACL has been able to increase soda ash production by 65,000t per annum. The 10MW power plant is currently capturing about 97% of its CO2 emissions and is set to become a zero-emissions facility.
“TACL will be able to capture CO2 from their boiler emissions and then reuse it,” confirms Sharma. “For the end user the electricity produced by capturing carbon dioxide will be clean electricity and the steam produced will be clean energy. For that reason, we can say that it is ‘emissions-free’.”
A clean break: promoting CCU technology
Having proved the efficacy of its new proprietary solvent in India, is Sharma confident that CCSL can now scale up the technology globally? The UK, for example, is committed to an 80% reduction in its carbon emissions by 2050, but regulations and emissions targets vary markedly around the world.
“Today, $1bn worth of amines are sold in the market to various industries to capture CO2, mainly the oil and gas sector,” Sharma states.
“The second set of customers wants to capture the CO2 and do something with it to reduce their emissions footprint. At present chemical manufacturers capture CO2 for around $150-$170 per ton; we can do this at $30 in India and $40 in Europe, so we see the uptake happening immediately.
“We have just secured a second client that will capture the CO2 to produce inorganic chemicals and we envisage a third client in the next quarter capturing the carbon and converting it into urea.”
“CCSL’s target is to reduce the cost of CCU technology by a further 50%,” Sharma continues. “From a UK perspective, for example, power plants pay a total of around £24 per ton in tax; if we can reduce this by a further half then it makes business sense for all power plants to implement the technology.
“We are working with a glass manufacturer in the UK that emits 100,000t of CO2 a year − one third from electricity and two thirds from the fossil fuels in the furnace. As a result, they cannot reduce their emissions by using renewable electricity unless they do so with CCU technology. In addition, the whole solution can be implemented or retrofitted in nine months and quickly pays for itself.
“If we can help our customers reduce production costs and in the same amount of time utilise the CO2 emissions on-site, then that’s going to be the game changer from a market point of view.”