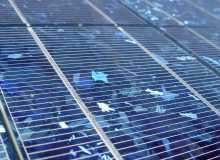
The year of 2011 has perhaps been one of the toughest for the photovoltaic (PV) industry. In 2010, solar production nearly doubled, growing into a major market in leading nations such as Germany, Japan and the US. But only a few months later, the industry has to face subsidy cuts, plummeting prices, overcapacities and weak demand.
What was set to become a glorious transition period toward more global market saturation has turned out to be one of the hardest years since solar became commercially viable some 30 years ago.
Nevertheless, according to a November 2011 report by IMS Research, global solar installations will reach 24GW by the end of the year, pushing up the worldwide capacity to about 64GW.
Figures from BSW-Solar and Bank Sarasin show that Germany will remain ahead of most competitors, adding approximately 5-6GW of PV to its grid in 2011, closely followed by Italy. Emerging markets, such as China and India, however are the driving force behind the figures.
According to industry experts, this growth strategy is the best way to escape the wrath of the weak market conditions. However, what the sector needs is more research into advanced and efficient technologies that are able to curb energy outcomes and minimise costs.
Some progress has been made regardless of the difficult situation: be it in the improvement of solar cells through the use of until now unexplored materials, the optimisation of PV production itself, as well as in the aesthetic design build sector – all are set to get PV back on track to ultimately become a major source in the world energy mix.
Improving PV cell production
Billions of solar cells are manufactured each year. At the heart of PV production is heat, which is used to test the cells’ mechanical strength, to oxidise, anneal, purify, diffuse, etch and layer them. Large furnaces are therefore part of all manufacturing steps of solar cells.
A conventional thermal furnace heats up a wafer by convection, while a rapid-thermal-processing furnace would use radiative heat to enhance the temperature of a silicon wafer up to 1,000°C within seconds.
A big leap in improving this process and to cut down costs has recently been made by the US Department of Energy’s National Renewable Energy Laboratory (NREL). Using optics to heat and purify solar cells, researchers introduced the Optical Cavity Furnace (OCF), calling it a ‘game-changing’ device.
The OCF combines the assets that photonics can bring to the process with strongly controlled engineering to maximise efficiency by 4%, while decreasing heating and cooling costs. It includes a range of lamps in a chamber, lined with highly insulating and reflecting ceramics.
"Our calculations show that some material that is at 16% efficiency now is capable of reaching 20% if we take advantage of these photonic effects," said NREL principal engineer Bhushan Sopori in a statement released at the end of October 2011. "That’s huge."
The furnace, which won the R&D 100 Award from the R&D Magazine in July, is also said to use about 50% less of the energy used by standard furnaces, costs significantly less money and has shorter process times with only a few minutes per solar wafer.
NRL is now aiming to build a manufacturing-size furnace that is able to process 1,200 wafers an hour, which would further push cost-effective and precise PV production.
The copper solar cell
The two main PV technology types in common use today are nano-crystalline and thin film PVs. As the latter currently offers lower efficiencies than crystalline – typically ranging from 7-10% compared to the energy output from the sun being 100% – crystalline silicon cells are in favour for many applications today.
However, with efficiencies of around 12-16%, crystalline cells are still far off the third generation solar cells that are potentially able to overcome the Shockley-Qeisser limit of 31-41% power efficiency.
Germany’s leading developer of PV technology, the Fraunhofer Institute for Solar Energy Systems ISE, claimed to have developed 21.4% efficiency multicrystalline cells. Through the use of long-term stable copper metallisation for the cell contact, they are set to improve both the efficiency of the PV and reduce their production costs.
The key challenge of copper metallisation lies in the creation of a high-quality layer between silicon and copper as a barrier against diffusion in the PV semiconductor, which otherwise could result in a potential failure of the operating cell.
According to the institute, nickel can be included here and act as a barrier to copper and silicon as well as an electrical contact to the silicon.
The researchers replaced the expensive standard silver contact on the front side of solar cells with cheaper nickel-copper plating, using feasible galvanic processes. The increase in efficiency is comparable with very costly solar cells using titanium / palladium / silver contact systems, which must be created in a considerably more expensive process.
Metallisation based on copper and nickel could also have considerable potential for cost savings for the next generation of silicon solar cells. The cells have shown better stability, with no consequences for their efficiency in thermal stress tests.
The researchers also noted that due to the significant cost difference between silver and copper, just changing the material and keeping the efficiency the same, it was possible to reduce the production costs by up to 10%.
Fraunhofer ISE is now working to transfer the results to industry-standard wafer sizes, something which has already been achieved by US-based Schott Solar. The company announced at the end of November, that it had reached an 18% efficiency measurement for its metallised copper solar cell.
With this method, the company has cut the production costs for the front-side of the cell by more than half. Schott will now produce prototypes to install them in a test module that aims to study the technology’s long-term stability and to reach an efficiency of over 19%.
Solar electric architecture
On a rather aesthetic level, a reviving architectural concept could aid the industry to make necessary steps towards market consolidation. Starting from 2010, interest in the building integration of PV, where solar elements actually become part of a building, has been growing worldwide.
Traditionally, building-integrated PV (BIPV) has often been degraded to a niche market because solar modules and panels were simply too expensive and their installation on roofs, building walls, windows and other parts of a building’s structure was difficult. But with cheaper and more efficient cells in the pipeline, BIPV is set to increase to almost 2.4GW by 2016.
PV architects and innovative designers throughout Europe, the US and Japan have started exploring creative ways to incorporate solar panels into their works and the trend of ‘solar electric architecture’ has began to emerge.
This has especially been driven by the rapidly falling costs per watt, greater ease of installation of rooftops by the means of new and highly efficient panels and shingles, but also has an aesthetic aspect as solar tiles and shingles have started blending into buildings.
Also the desire to ‘go green’ by owners of residences and commercial buildings has further boosted interest.
BIPV radically changes the orientation, plan layout, form and the footprint of a building, which in turn will look more futuristic and striking in appearance. A complete BIPV system includes PV modules, which can be thin-filmed or crystalline, transparent, semi-transparent or opaque, a charge controller that regulates the power in and out of the battery storage bank, along with a power storage system, which is generally the local utility grid.
It further integrates power conversion equipment, backup power supplies such as diesel generators as well as all necessary mounting hardware, wiring and safety disconnects.
Once integrated onto the building façade or roof, they work as a power generator and are usually interfaced with the available utility grid. It can also be used in stand-alone and off-grid systems, however, the benefits of grid-connected BIPV are still greater. The storage is essentially free, it is unlimited in capacity and reduces energy costs for the building owner, while it also helps support the utility grid during peak demand times.