
Development of New Materials and Device Structures for Competitive Mass Production Methods and Applications of Organic Photovoltaics, funded by Germany’s Federal Ministry of Education and Research and commercial giant Merck, aims to create fully printable photovoltaic cells that unlike regular cells do not contain indium tin oxide (ITO), which is both expensive and resource intensive.
In the long term, the cells could open up new solar applications, including the chance to capture solar power through window coatings. While the consortium involved in the project combines commercial and academic outfits from across Europe, it is led by the Karlsruhe Institute of Technology (KIT) Light Technology Institute. Project lead, Alexander Collsman tells us more about the project goals and what challenges might arise.
AL: What makes organic solar cells different from traditional photovoltaics?
AC: The new generation of solar cells is light-weight, mechanically flexible, semi-transparent, and allows for low-cost production. They can be applied to surfaces of nearly any shape by state-of-the-art printing and coating processes, which Organic opens up new perspectives, in particular, for the architectural design of buildings. The solar modules can be integrated in facades and even windows. In addition, they open up new OEM [Original Equipment Manufacture] applications in the automotive or consumer sectors.
Organic solar cells are fabricated by low-cost printing and coating processes, such as gravure printing, screen printing, slot-die coating or spray coating in continuous roll-to-roll processes. Plastic carriers provide mechanical flexibility of the modules. At the same time, organic solar cells are characterized by an extremely low consumption of environmentally compatible resources, unproblematic disposal, and a very short energy payback time.
AL: What do you hope to achieve through the project?
Although solar power is packed with potential, prices are kept impractically high because output drops to zero after sundown.
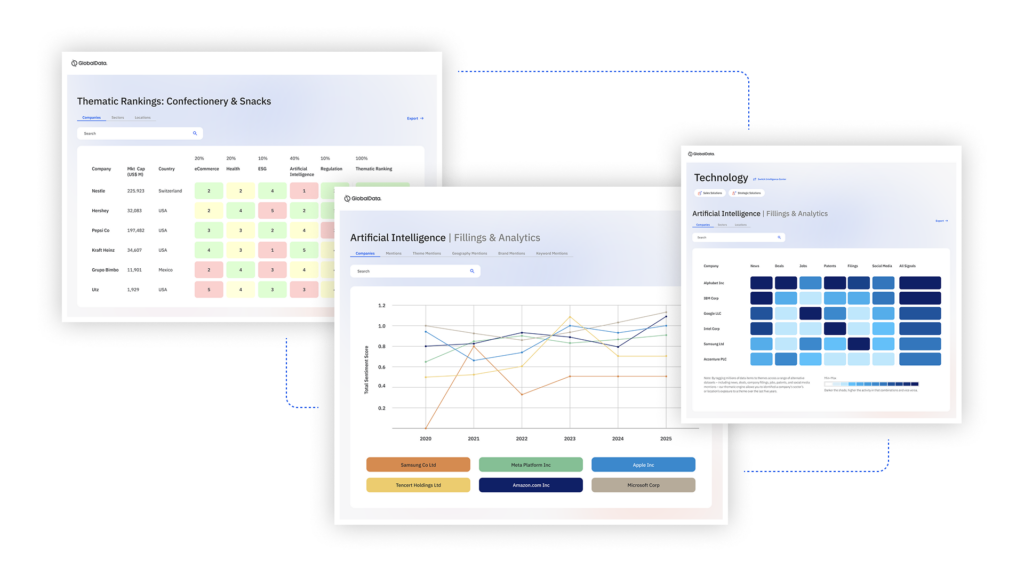
US Tariffs are shifting - will you react or anticipate?
Don’t let policy changes catch you off guard. Stay proactive with real-time data and expert analysis.
By GlobalDataAC: State-of-the-art organic solar cells comprise transparent electrodes from indium tin oxide (ITO) that has a reasonable conductivity while at the same time exhibiting good transparency. On the downside, ITO requires high temperatures during its fabrication. Indium is an expensive commodity with unknown availability and thus unforeseeable price development. The price of ITO has increased more than tenfold over the last couple of years. Furthermore, it is brittle and hence does not comply with the mechanical requirements for flexible substrates.
In our project we aim at printable transparent electrodes. Those can contain e.g. conductive polymers that are supported by metal grids to improve the collection of photo-generated charges. Both the conductive polymers as well as the metal grids can be printed. For the latter we use silver-ink formulations.
These hybrid electrodes will then be integrated into organic solar cells. If both the ITO and the metal counter electrode are replaced by this new electrode, the devices become semi-transparent. Here, semi-transparency refers to some light absorption in the photo-active layer, no solar cell without light absorption. Still, it is possible to peer through the device as not all light is absorbed.
People use semi-transparent shadowing foils to shade their offices in summer. The basic idea behind semi-transparent solar cells is to add some extra functionality to these foils. If the light gets absorbed anyway, one may want to use it to be converted to electrical power.
AL: How can it move the development of organic solar cells forwards?
AC: In general, at KIT we believe in future printing of organic solar cells, because printing has the potential to allow low production costs. Making the electrodes printable will help the technology to evolve. Semi-transparent devices in particular are considered as one of the key applications for organic photovoltaics. Common silicon solar cells cannot be built semi-transparent. Therefore organic solar cells can enter a market segment without strong competition. Having a market for this young technology will increase the awareness of organic solar cells.
AL: What was the initial driving force to get the project started?
AC: The project is industry driven. It aims at enforcing the business location Germany. Germany hosts highly specialized companies all along the value chain for the fabrication of organic solar cells. This is very much reflected in the project consortium where Merck synthesizes new light-absorbing materials for organic solar cells, PolyIC and Kurz will develop new device architectures and do the printing of the devices and Siemens, Webasto and Centrosolar will take care of the device integration. No other country has such a strong economy all along the value chain. It is a natural development to join the scientific and economic forces and resources to bring products on the market. Moreover, world-wide renowned research groups at universities and research centres elucidate fundamental scientific questions that occur during the development of new products.
AL: What is the make-up of the project team in terms of people and skill sets?
AC: At KIT the project is embedded into the Organic Photocoltaics Group at the Light Technology Institute. This group comprises 14 scientific co-workers and about 20 Bachelor and Master students. All team members have different background from electrical engineering, physics, material science or chemistry. This interdisciplinary approach allows to cover many aspects of solar cell design. It also facilitates the collaboration with other scientific and industrial groups with different backgrounds such as material suppliers and product end-users.
AL: What are the key deadlines throughout the project?
AC: The project will run for three years. At KIT we will deliver small-area prototypes of semi-transparent solar cells. These prototypes will then be handed over to partners to do the scale-up.
AL: Can you tell me more about the new component architectures for semi-transparent and non-transparent solar cells that you will be studying?
A new innovation that can ‘print’ coloured glass and use it to harness electricity from the sun’s rays is currently reaping awards – so what’s all the hype about?
AC: Commonly, organic solar cells are built according to the following architecture; Glass or plastic carrier (substrate), transparent electrode, light-absorbing layer, metal counter electrode. Usually, buffer layers are applied between the electrodes and the light-absorbing layer to facilitate charge carrier extraction from the device. For a semi-transparent device, the metal counter electrode is replaced by a second transparent electrode. However, this architecture requires special attention to the design of the buffer layer in-between.
AL: What are the main challenges that you have encountered or expect to encounter over the course of the project?
AC: Typically, layers from organic semi-conductors and the envisaged printable electrodes have a thickness on the order of 50-200 nm, this is about one hundredth of the diameter of a human hair. Technically, one of the main challenges is to apply those ultra-thin layers on large scale, i.e. applying nanoscale functionality on square meters. The layer homogeneity is crucial to allow deposition of the subsequent layers. Furthermore, the devices will have to exhibit power conversion efficiencies and device lifetimes that make them suitable for real-life products. Giving numbers here is difficult because we are shooting at a moving target, i.e. market requirements and performance of competitive technologies change. Roughly, for semi-transparent devices power conversion efficiencies well beyond 5% will enable first commercialization.
AL: How does the research fit into the broader programme of organic photovoltaic research?
AC: At KIT these activities are implemented into wider organic solar cell research. This project covers only some aspects of organic photovoltaics. Further challenges to master will be further enhancements of the device stability and performance. The latter we attempt to tackle in another BMBF funded project on organic tandem solar cells that, according to theory, should enable competitive power conversion efficiencies well beyond 10%. Another important aspect of large-scale fabrication of organic solar cells is the replacement of the commonly used hazardous solvents.
These solvents work well on lab-scale to investigate the fundamental working principles of organic solar cells. However, on large-scale, eco-friendly materials are mandatory as the use of toxic solvents would blow any budget due to expensive safety precautions. Within the next three years, we will work on this topic in a new project that is funded by the European Commission.