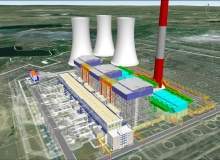
Use of 3D software is quickly becoming the gold standard for power plant design and engineering projects, as in other design-build sectors. The ability to visualise the design and placement of all the complex components of a large-scale power project can help minimise costly mistakes during the construction stage.
But with new features rolling out all the time, modern 3D modelling tools can improve many more processes on a large design-build project, from inter-team communication to short-notice problem solving.
As 3D software suites become more cost-effective to deploy and increasingly integral in the industry, this technology has begun to gain a foothold in developing markets, where companies are often engaged in infrastructure projects of an unprecedented scope and scale.
India, for example, is pushing through hundreds of infrastructure projects to support the sustained economic growth spurt that has seen the country become one of Asia’s pre-eminent powerhouses. As older power stations are phased out, massive supercritical thermal power plants are being ordered by the government to provide more reliable and plentiful electricity to the Indian population in a way that is more efficient, both environmentally and financially.
Koradi mega-plant
One such project is the new $1.5bn Koradi supercritical thermal power plant in the Indian city of Nagpur, Maharashtra, being built to modernise the existing power facility there. The power station incorporates three 660MW steam turbine generators with supercritical boilers, along with all the associated auxiliary infrastructure and equipment, including heat exchangers, vacuum pumps, concrete water pumps and safety systems.
Gujarati engineering and consultancy firm L&T – Sargent & Lundy (L&T – S&L), the joint venture of Indian engineering firm Larsen & Toubro (L&T) and US-based power design consultant Sargent & Lundy, was chosen, through L&T, to provide complete engineering and design for Koradi’s main plant.
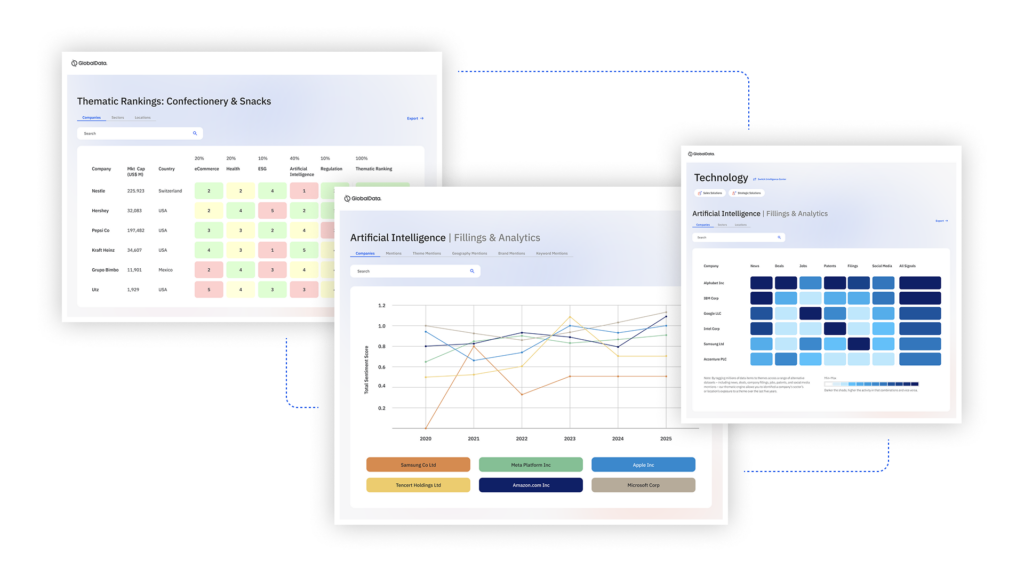
US Tariffs are shifting - will you react or anticipate?
Don’t let policy changes catch you off guard. Stay proactive with real-time data and expert analysis.
By GlobalDataThe company’s project scope included the all-important boilers, turbines and generators, as well as a host of other minor facilities. L&T – S&L’s engineering role on the project is now 90% complete, with the construction stage firmly underway and an estimated first phase commissioning date set for September 2013.
L&T – S&L’s experience with supercritical power projects, having designed two in the past (one in India and one abroad), played a role in the company’s selection, but as L&T – S&L deputy manager – mechanical and Koradi project manager Ashutosh Singhvi said the company’s 16 years of experience with 3D modelling software is also a differentiating factor for the company in the Indian market.
"Not many companies use the 3D platform for power plant engineering in India. The use of them tends to be limited to critical areas. Unlike other companies in India, L&T – S&L develops each and every component of the plant that will be required for physical interface check and visualisation."
Overcoming challenges
The use of 3D modelling and planning software – the company uses Bentley software, including MicroStation, Navigator and Structural Modeler – was particularly necessary for the Koradi project, which is a tricky and complex build in a number of ways.
"This project is one initiative where the power station expansion has been proposed to phase out old facilities," said Singhvi. "The site is near to the existing plant, which brings a lot of constraints regarding limited land, strict environmental norms, a stringent project schedule and more imposing corporate social responsibilities."
The main challenge on the project was simply to fit the massive units and all necessary infrastructure into the designated space on the existing Koradi site. 3D software played a central role in overcoming this limitation, as the ability to model all aspects of the main plant on a single 3D platform allowed L&T – S&L to ensure the drawings used on-site, which are derived from the 3D models, would be accurate.
The simulated visualisation of how the plant’s components would fit together in reality helped immensely in the project’s frequent constructability reviews with project partners, according to Singhvi. "The entire main plant is being developed on a 3D platform, which mean’s there’s consistency right from conceptualisation to detailed design," he claimed.
As a result, the L&T – S&L team found that the extra effort of modelling the plant in its entirety during the design and conceptualisation phases has paid dividends in terms of making the project smoother and more cost-effective in its later stages. "A 3D model is a replacement for thousands of 2D drawings and not much human imagination is required in case of 3D," says Singhvi.
"A 3D model takes a little more time at the beginning of the project, but once we go further, it definitely helps the project as design and physical integration is ensured."
Perhaps the clearest demonstration of this software advantage is the fact that the design and engineering teams’ navigation software was made available to on-site construction workers, who have been able to use the detailed 3D model as a reference point to the work they are doing.
Communications advantages
As well as making sure that all plant components are precisely where they need to be when it comes to construction, the team found that using a single, flexible software platform was a key facilitator for efficient communication between geographically disparate teams.
As on any project of this size, the stakeholders and contractors are spread far and wide. Site owner Maharashtra State Power Generation Company (Mahagenco) and client / parent firm L&T both needed to be kept abreast of the project’s development. The plant’s turbines were manufactured by Japanese firm Mitsubishi Heavy Industries, meaning frequent consultation was required with Mitsubishi as well as other original equipment manufacturers.
Software proved to be a simple way of visualising the project’s development in a simple way while also maintaining accuracy. From the client’s perspective, more advanced visual renders were central to explaining any issues and describing how the finished plant would actually look. "The superior quality of visualisation images obtained from the MicroStation Luxology rendering engine helped in explaining the aesthetic aspects of the plant to the customer to secure approval," Singhvi said.
Within L&T – S&L’s teams, the ability for remote collaboration and real-time updates of new key data simplified the communication process considerably. "All plant information resides in a centralised database. The project engineering team is given access based on their needs. Information – both physical and technical – from vendors is integrated in database. Information that is important among various disciplines is also recorded in this central place. So the entire project team is using the same information, wherever they are."
Although Singhvi noted that L&T – S&L is currently one of only a few companies in India to routinely use advanced 3D software for power plant design projects, it’s unlikely this situation will persist for long. As 3D modelling tools continue to drop in price and India moves forward with more large-scale power projects to guarantee a solid electricity supply for its population, this digital resource looks set to become as ubiquitous in India as it is in the West.