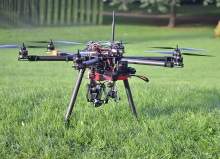
Fukushima was rightly classed as a disaster, and its long-term legacy is unlikely to deviate away from such a definition. But it won’t necessarily be utterly devoid of positives. One possible welcome development might bring an end to placing human pilots at risk of radiation in the aftermath of a leak.
Inspired by these events, a team of researchers at Bristol University’s Interface Analysis Centre set about developing a semi-autonomous drone called the AARM system that could replace the flesh and bones of humans with the wires and chips of robots.
The team launched a first model of the system in November 2013, having successfully tested the radiation monitoring capability at two sites with levels of radiation in southern Romania and the UK. Since then, there have been a number of development changes to both the drone, which evolved from a six-armed hexacopter to an octocopter with eight rotors laid out in a quad formation to increase power and stability, and the technology that drives the flight system and the sensors. Having been inspired by the Fukushima events, the team is now set to take it to Japan to assist in the cleanup operations.
Dr. Tom Scott, project lead and director of the Interface Analysis Centre, tells Adam Leach how things have progressed both technologically and commercially and what the future holds.
Flying radiation monitor in a backpack
Adam Leach: What changes have you made to the system since it was first launched in November of last year?
Dr. Tom Scott: We’ve just taken receipt of our latest prototype from our workshop. It has folding frames so that it can fit in a backpack, which means we can deploy our hexacopters anywhere in the world and take them on a plane with the least possible hassle.
It’s a carbon fibre frame which folds down and has eight rotors on it set out in a quad formation. We started with six, which was very stable but what we wanted to get was more grip in the airstream so we wanted to go with eight. But instead of having eight separate arms we went back to four but with two on each arm because it improves both power and stability and means we can carry more.
Not only are we able to carry radar detectors but we’re now starting to carry scanning Lidar, which is on the order of 2kg and can reconstruct incredibly accurately the 3-D environment below the octocopter with millimetre precision that we can lay the radiation data on top of. It’s almost unrecognisable. It’s going so fast it’s ridiculous.
AL: What software does the drone use and how complex is it to use?
TS: We’ve got a flying gamma ray spectrometer which is mediated by the onboard micro-computer which is an Anduino-based system and we have a full suite of software that controls everything, which you can control on a laptop.
It’s very easy to use; you can pre-programme your flight path and stuff. My five year old can use it in fact. It was initially a Raspberry Pi but we’ve jumped to Arduino as it’s tough as old boots.
AL: What permissions or licenses are required to fly the drone on nuclear power station sites?
TS: If you’re going to fly in the UK, you need an airframe and a pilot that is certified by the Civil Aviation Authority (CIA) and you need an exemption to fly over a nuclear facility because usually they are no-fly zones. You might also need to provide flight plans. In the event of a disaster, nobody really cares about the rules, so we can do a lot more than standard operational day-to-day rules allow.
AL: What stage are you at with taking the technology over to Japan to support the cleanup of Fukushima?
TS: I went to Japan in January for preparation and we’re going to be going out at the end of April to go into the prefecture region and use a small number of drones to map areas that are outside the immediate confines of the Fukushima. There’s a 1.5km exclusion zone around the site, but hopefully we’ll get onto the site before the end of the trip with some help from Hitachi and AMEC, who we’re working with.
We’re going to use the trip as a demonstration where we’re going to work in the contaminated zones outside that and work in the hottest areas outside the plant.
AL: What other sites are you planning to use it at?
TS: We’re going to Fukushima; we’ll also be going to some of the UK site license companies. We’re just in the process of getting permissions to fly at the Diamond Light Source [the UK’s national synchrotron science facility at the Harwell Science and Innovation Campus] which is adjoining the Carwell Site. We’re also in the process of doing all the paperwork to do a test reactor site in Cornwall and we’re putting together paperwork and risk assessments for Sellafield and Aldermaston.
AL: What is the target market for the system?
TS: In the UK you have your site licensing companies who would want it for site monitoring and also disaster response.
Sellafield was evacuated a few weeks ago because they had an alarm go off. If they had an octocopter like ours they could have deployed it at the touch of a button and flown it out to the alarm and taken a replica reading at the same point to see if it replicated the same results and verify it. Instead they evacuated the site for a day, which probably cost a couple of million in operations because they still had to pay people for that day.
Also, I’ve just got back from a UKTI event in Turkey where we were showing it to the Turkish government because they’re about to go into nuclear power. It was very fruitful.
AL: How are you going to develop it commercially?
TS: We’re university guys; we do R&D to produce a product. It’s quite unusual that we’ve got it commercially ready, but ultimately we’re in it to do the research so we want to have a company that licenses and takes it on for us. We’re discussing with the university whether we spin out a company to directly lease for certain activities to a services company.
AL: What further developments are you working on?
TS: Where we’re going with it now is not just having laser distancing combined with gamma spectrometry but having thermal imaging, photo grammatary, scanning vidar, gas sensing and acoustic sensing.
We’re making it into a multi-tool, a bit like The Thunderbirds but instead of having different vehicles to serve different purposes, we have one vehicle with different attachments. The computer immediately recognises what tool is plugged in and immediately starts controlling it.