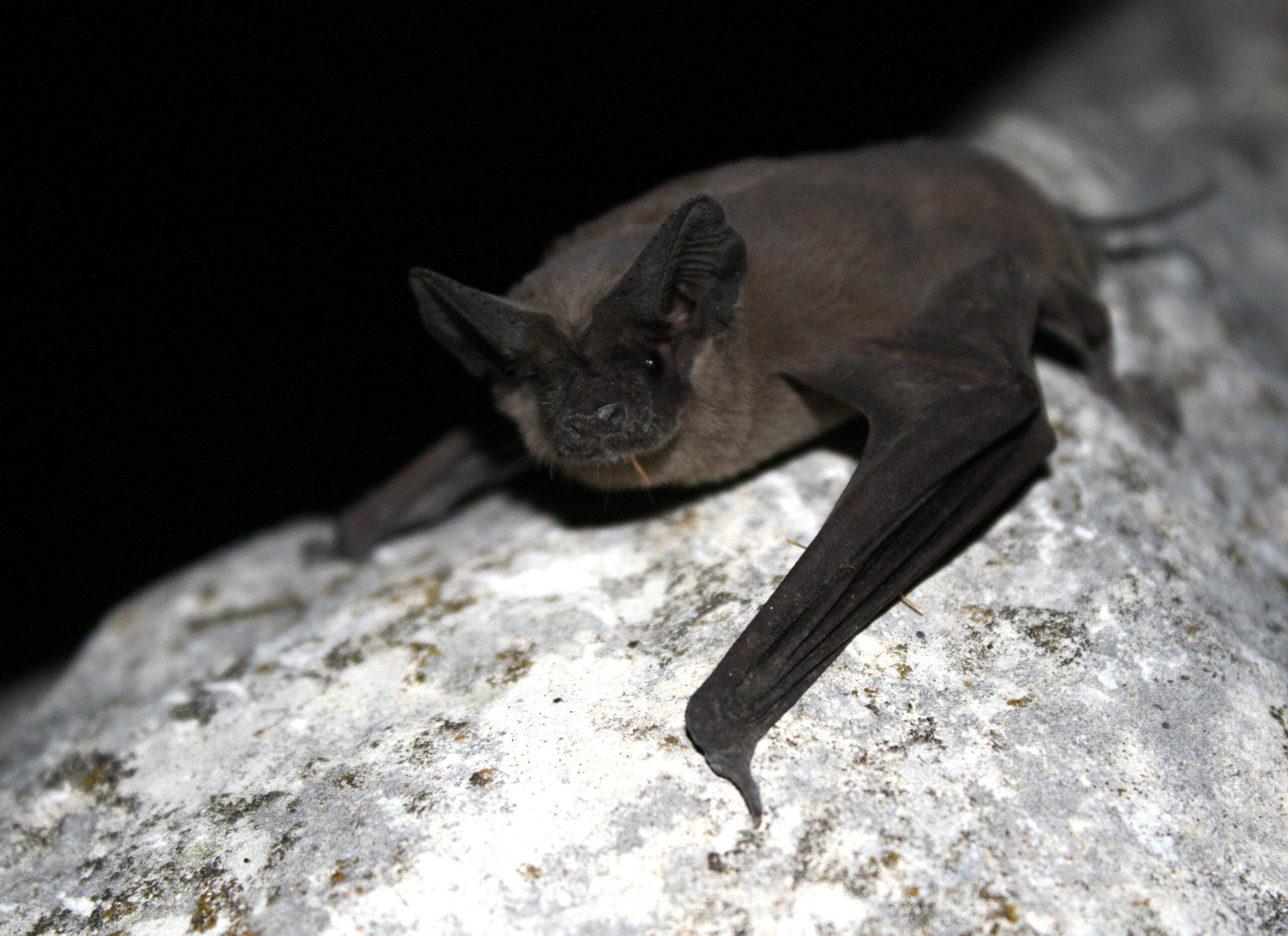
The vessels in nuclear power plants contain highly radioactive nuclear fuel cores. If cracks appear, it could be an indication that the reactor isn’t working as it should, leading people to worry about its dangerous contents. In an extreme scenario a failure to spot faults could cause vessels to release massive amounts of radiation, which would be catastrophic for the surrounding community if exposed to it.
Just this year around 16,000 cracks were found in the steel reactor pressure vessels in one of the reactors at the Tihange nuclear power complex in Belgium. The reactors were immediately shut down, causing public uproar and resulting in cost-worthy downtime – outcomes which could have been prevented with earlier detection.
Mathematicians Dr Tony Mulholland and Dr Ebrahem Algehyne at the University of Strathclyde in Scotland may have developed a way to help reduce the costs of maintenance with an improved means of detecting structural problems. They have come up with a new mathematical model, based on the way bats detect their environment, which they have used to develop a new ultrasound detector, called a transducer.
The new model has a more intricate design than conventional transducers, and is better at spotting cracks in structures. In the case of power plant inspections, it could "streamline the process and lead to time and cost savings", the researchers say.
How it works
The device works in a similar way to how a bat builds up a picture around itself, by firing out and receiving sound. It is stimulated by an electrical signal, which causes it to vibrate and emit a mechanical wave. The wave then passes through the structure of interest, before being received by a second transducer at the other end that converts the vibration back into an electrical signal.
How well do you really know your competitors?
Access the most comprehensive Company Profiles on the market, powered by GlobalData. Save hours of research. Gain competitive edge.
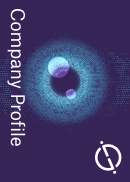
Thank you!
Your download email will arrive shortly
Not ready to buy yet? Download a free sample
We are confident about the unique quality of our Company Profiles. However, we want you to make the most beneficial decision for your business, so we offer a free sample that you can download by submitting the below form
By GlobalDataA few of these transmitting and receiving devices are placed around the structure and an image of the interior of it is formed out of a grid of pixels. For each pixel, the distance from each of the receivers is calculated and an image of the inside of the structure is built up.
Traditionally, transducers like this were man-made from sawing and cutting material to shape and build the device, and were typically composed of components of one size. The new device contains components of various sizes, meaning it can detect a much larger range of frequencies.
"To increase the frequency range that the device can operate over it would seem logical to build a device that is composed of a range of sizes of resonators," says Mulholland. "Think of the way in which a piano creates a wide range of notes by using strings of different lengths."
Mathematics plays its part
Due to the complexity of the device in comparison to traditional ones, building it would be expensive and time-consuming. So the researchers came up with their mathematical model to begin with, to check that their idea had promise.
They led a mathematical investigation to look for design possibilities that would contain a wide range of length scales, such as the structure of a snowflake.
"One such design is called a fractal," explained Mulholland. "This is where a geometrical shape is repeated over and over, at finer and finer length scales, to create the final design."
During an inspection of a nuclear power plant, there are likely to be cracks of different sizes, so it would be preferable to send out waves of varying wavelengths. The transducer would need to be able to operate over a wide range of frequencies to achieve this.
"Cracks can be more readily imaged if the ultrasound wave that interacts with them is of a wavelength that is of a commensurate size," says Mulholland. "Hence, these fractal ultrasound transducers could be more accurate."
The timeliness of the design
Researchers can come up with more complex and more intricate designs for transducers, thanks to the development of 3D printing. As Mulholland says, "there’s a certain timeliness to this fractal transducer design".
One of the reasons that the traditional transducers were more restricted is because the manufacture of them was based on sawing and on removing material to shape the device.
"With modern additive manufacturing such as 3D printing, we can build far more complex structures which are limited only by our imagination," says Mulholland. "This new-found freedom needs direction and guidance, and so these fractal devices provide this."
As is stands, to carry out an inspection a set of transducers are required that operate at different frequencies, which can take some time. To save time and money, these could be replaced with just one type of device that works with this fractal system.
Mulholland says that he hopes these new devices will "aid in the prognosis of detected flaws and improve safety".