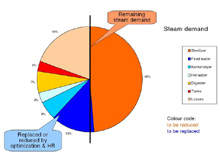
Anyone interested in speeding the adoption of renewables in Asia would have done well to hear some of the papers being read at PowerGen Asia in October. Successes are being reported from small and medium scale projects, reinforcing early experience in energy and environmental improvements. But the message is clear; populations still often underuse or misuse their existing resources.
Environmental improvements can therefore, surprisingly, also improve profits. And using small/medium-scale local resources and distributing power around the grid have the added benefit of reducing the costs and losses involved with long-distance power transmission.
Some of the most recent and interesting work being undertaken focuses on environmental protection strategies, cleaner and distributed generation, biomass, and hydropower. In particular, there are lessons to be learned from biomass energy development in Southeast Asia
Biomass has gathered much attention, and individual projects have proven profitable. However, many more would come on line if governments would form more level playing fields. Along this line, it is also vital to move away from the ‘hidden’ subsidies given to fossil fuels. Investors should instead be rewarded with (for example) feed-in tariffs – an essential and low-cost incentive for developing renewables.
A need for feed-in
Among the speakers at Powergen were Christoph Kwintkiewicz and Allan Mountain of Key Energy, New Zealand. Kwintkiewicz and Mountain are energy consultants, and have before now made powerful arguments for feed-in tariffs. In 2007 they produced a paper on the subject for the New Zealand government. Kwintkiewicz and Mountain say that feed-in tariffs make a whole range of efficient technologies economically viable, including fuel drying, heat recovery, and CHP from wood processing plants.
There have been notable successes and in Europe Germany has led the way. Meanwhile, in Asia Thailand introduced feed-in tariffs in its Very Small Power Producer (VSPP) Act on local and national level. Key Energy has been supervising and training local engineers in the palm oil industry, using organic wastes for biogas and steam turbine power generation.
Kwintkiewicz and Mountain’s most recent work has been focused on process optimisation for combined heat and power (CHP) in palm oil mills. Mills are often now self sufficient, but not fully optimised – for example, steam boilers are often designed for coal. But recent advances are working towards the aim of true zero waste production.
New heat recovery systems can cool the flue gas below dew point to condense for efficient heating from wet fuel like that used in a palm oil mill, also important because it cleans the flue gases of dust and acids.
Other profitable improvements include automatic moving step grates or vibrating gates which can replace manual fly ash removal from fixed grates to reduce handling costs, steam fluctuations and fly ash. Flash steam from the condensate can replace low pressure steam for hot water, tanks and oil recovery heating. New controllers can reclaim steam blown off by safety valves. Blow out steam can sometimes be profitably recovered, too.
Recovered heat can be used for feed water pre-heating or fuel drying. Blow-down heat recovery and deaerator operation can often be optimised (depending on salt content and water treatment, blow-down can be up to 9m³/h of steam in a 20-ton boiler).
There are also good possibilities for biogas recovery to produce diesel for example. Some mills have already started to use palm oil mill effluent to produce biogas for running internal combustion engines to generate power. The engine cooling and exhaust heat is usually not used, though, and can also profitably be recovered.
Kwintkiewicz and Mountain say that giving steam a value by selling power to the grid alters the economics of production. The steam and heat losses tolerated in older processes now visibly reduce plant profits, while the improvements give a stable income to the mill from selling power.
CHP from biomass
The key is that these improvements are good for a company’s ‘bottom line’. A paper by Dr. Helmut Korber, CEO of APC Consulting, discusses the large potential for additional income in the palm oil industry by “sustainable conversion of biomass wastes into energy”.
Malaysia, Indonesia, and Thailand for example, produce more than 75% of the world’s palm oil. Besides being inefficient, the processes can produce highly polluting process waste, particularly surface water pollution. Improvements here have moved the crude palm oil industry towards sustainability. In Malaysian mills, the Department of Environment introduced early laws to require the treating of the palm oil mill effluents to an acceptable standard before discharge. The palm oil industry grew rapidly in Thailand, too, and the country has an estimated power potential of nearly 100 GWh/year from palm oil mills.
The manner of production is of course key, but there are many opportunities throughout the various energy intensive industries for replacing old and inefficient process heating with more modern and efficient CHP. Sawdust and waste/green wood is often now burned wet, for example, with over with 50% moisture content. Heat recovery and wood drying can cut boiler wood demand by 15-25%.
Converting pollution into energy
CHP from biomass has perhaps the greatest potential among all Asian renewable energy sources, with several very fruitful sources. There have been successes, for example, with rice mills. The Bangsue Chia Meng Rice Mill is one of the largest rice mills in Thailand, and was an early demonstration project built over ten years ago in 1997 supported by the EC-ASEAN Cogen Programme.
The mill was producing over 100 metric tons of rice husk per day from processing the paddy. Angewandte Physik Consulting GmbH (APC) of Germany were involved in using the rice husk as fuel in a boiler coupled with a fully condensing steam turbine for power generation. A 2.5 MW cogeneration facility was commissioned in March 1997, and has been working profitably ever since.
The plant generates hot air for use in drying the rice paddy, cold water from the condenser is used to maintain the cool white rice storage cells, and there is no need to dispose of 100 tons of rice husk a day. It has made the plant self-sufficient in power, adding to security of supply, and also exports power to the grid.
When these factors combine and produce financial as well as environmental incentives is when projects can really get off the ground. Building suitable technologies is therefore, vital to the success of biomass and will help garner more government support.
PowerGen International will be held in Orlando, Florida, US, from 2-4 December 2008.