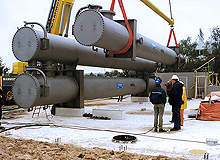
When fossil fuels eventually run out, future generations will look back in amazement at how we wasted so much of this vast resource. Indeed, this is a major cause of our environmental problems. Internal combustion engines convert only about a seventh of the energy in petrol into useful work, while often only a third of the fuel energy in a power station is delivered to customers, with most of the rest going down the environmental drain.
Using the waste heat makes for a much more efficient supply. Early power stations were smaller and closer to the demands they supplied, and so many actually combined both heat and power. The trend towards large power stations reduced the demand for combined heat and power (CHP), but it has become more popular again over the last 20 years. Plants have capacities of 100s of MWe with fuel efficiencies of above 90%. Ideally, they avoid fossil fuels altogether and can be powered by renewable sources like solar, biomass and geothermal.
The best returns on the use of heat come from the energy intensive industries (chemicals, engineering, foods, glass, oil, mining, metals, paper and textiles).
Another key use is to provide district heating, which supplies residential and commercial properties including large apartment blocks, offices and hospitals, even cities. The ready availability of heat in homes has additional benefits – it cuts electricity used for heating space and water.
Heating the district
Although district heating has only a 10% market share in Europe as a whole, Euroheat reports penetration of 50% or more in North, Central and Eastern Europe. The EU has estimated that District Heating and Cooling (DHC) alone could reduce European CO2 emissions by nearly 10% using mainly renewable sources and industrial waste heat.
A major question is what to do with the heat during summer. The Summerheat project analysed the possibility of using it for cooling, particularly for working chillers and air-conditioning systems (tri-generation).
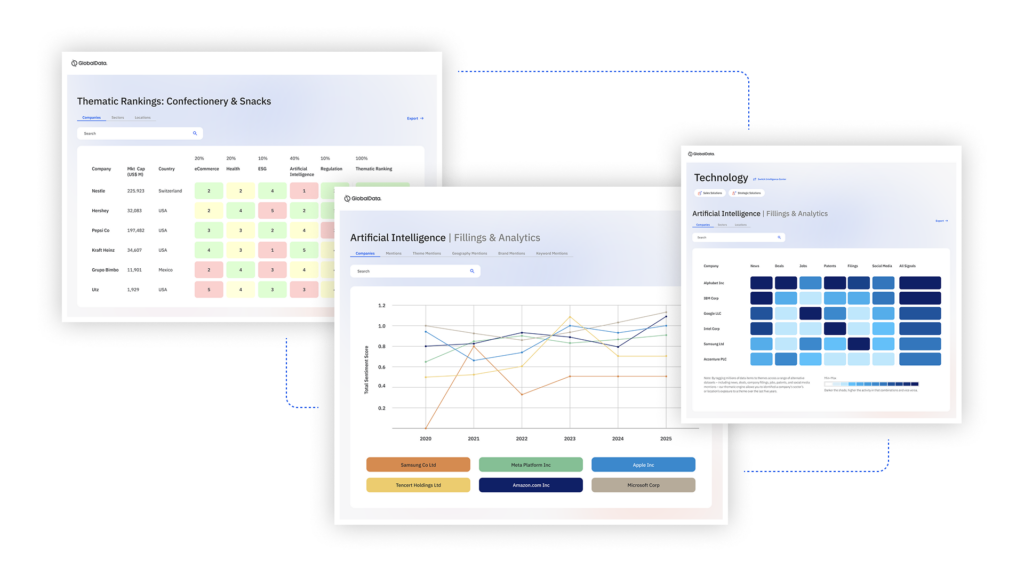
US Tariffs are shifting - will you react or anticipate?
Don’t let policy changes catch you off guard. Stay proactive with real-time data and expert analysis.
By GlobalDataBesides reducing the repayment times of district heating as a whole, it is more energy efficient than standard cooling systems and can therefore reduce overall CO2 emissions. The project favoured single-effect LiBr absorption chillers, a mature technology that can be operated efficiently even in 90°C heat. The best environmental performance of all was reported from a centrally supplied system in Copenhagen using both absorption and free cooling.
There must also be some way of dumping heat if the district heating system temporarily goes out of action. Bronswerk Heat Transfer has developed a fast, air-cooled dump condenser. The condenser immediately switches from standstill to full capacity, but should only be used when needed to avoid wasting the heat.
Economically, the electrical output of CHP is more valuable than the heat output, so the key figure is the electrical power efficiency, and only then the heat efficiency. Fast project repayment times, however, require efficient heat exchangers.
Heat exchange
Reclaiming waste heat from the cooling system (often 30% of the total) is fairly straightforward. Heat from the engine’s exhaust gases (another 40%) can also be reclaimed, but the gas-to-water or gas-to-air heat exchangers need to withstand the NOx and SOx held in the high temperature gases. Extracting all the heat means condensing the water vapour when it forms acids, which attack the exchanger (which also periodically needs to be cleaned of soot). Key design factors are the construction materials, temperatures and pressures, and water quality. Heat transfer rates depend on geometry and heat transfer area, coolant composition, coolant inlet temperature and flow rate.
Bowman Exhaust Gas Heat Exchangers, for example, work with Cogeneration / CHP equipment up to 1MW. They are fully welded, with stainless steel tubes, tube plates and body, and cast iron end covers, making them compatible with biogas, diesel gases and natural gases. Used with equipment like header tank heat exchangers, charge air coolers and oil coolers, the exchangers can reclaim up to 60% of lost heat from the engine.
The 600kW engine versions can recover up to 425kW from exhaust gas flows of up to 45kg/min and exhaust gas outlet temperatures of 120°C. The exhaust gas pressure drop is 3.1kPa. The primary circuit (tubeside) is installed through the tubes and the secondary circuit (shellside) is installed over the tubes. According to sales manager Jamie Pratt, Bowman has recently supplied five Exhaust Gas Heat Exchangers for use on three CHP power plant units in a new residential eco-village of ten houses in Finland. The plant is fuelled by gas produced from a wood burner, and the Bowman units cool the exhaust gases and recover heat from Sisu Gensets.
Maintenance is crucial to efficient heat exchange. Tube fouling cuts heat transfer, but there are so many tubes in heat exchangers that it is normally impractical to test them all. AcousticEye’s Dolphin system uses acoustic pulse reflectometry, which sends an acoustic wave down the tubes. Any change in the cross sectional area creates a reflection, which can be detected.
District heating substations
Heat exchanger substations transfer heat from the network to the building for radiators, underfloor heating and domestic hot water. DH substations normally use plate heat exchangers, which are compact, lightweight and efficient.
Traditional gasketed plate heat exchangers can be opened for cleaning and maintenance. Brazed heat exchangers instead have a brazed seal. Danfoss is a major manufacturer, offering a range of gasketed and brazed plate exchangers. Outputs, temperature ranges and pressure drops can be adjusted by varying the number of plates. The XG gasketed exchangers can be opened for cleaning and replacing plates and gaskets. The XB brazed exchangers are virtually self cleaning, using a cleaning pump and cleaning compound.
All-welded exchangers suit high temperature, high pressure systems. Alfa Laval’s new Alfa Nova fusion-bonded exchangers form a single stainless steel unit. Corrugated stainless steel plates are bonded together for high thermal efficiency and strength. High turbulence gives low risk of fouling. They work in temperatures ranging from -50°C–550°C, with a design pressure range up to 25bar, and can be used for high or low alkalinity water.