The power industry faces mounting pressure to maximise productivity and efficiency. Ageing transmission and distribution infrastructure is highly inefficient and long overdue for modernisation. Equipment failures can lead to costly power outages and expensive asset losses, affecting company profitability and disrupting electricity supply to consumers.
Automation technologies will be key to driving productivity and efficiency across the power industry over the coming decades.
Industrial robotics: precision and performance at scale
In future, industrial robots will become ubiquitous in power plants managing complex and monotonous tasks. Robots can operate continuously at peak efficiency, completing activities faster and more precisely than human workers. While the initial investment in robotics may be substantial, the long-term financial benefits include lower labour costs and increased operational efficiency.
Industrial robots will also play a greater role in the efficient operations and maintenance of renewable assets such as solar and wind farms, supporting the energy transition by making these more economically viable. Robots are already installing, maintaining and repairing renewable energy infrastructure at speed and scale. For example, AES claims its AI-powered Maximo robot can reduce the time and cost of deploying solar panels by 50%, with the company predicting that 70% of solar construction could be automated.
Robotic process automation: cutting administrative inefficiencies
Beyond physical infrastructure, robotic process automation will streamline administrative workflows by automating back-office tasks such as compliance reporting and billing, eliminating inefficiencies and manual errors. This will free up staff for higher revenue-generating activities such as customer engagement.
Autonomous drones and satellites: revolutionising infrastructure inspections
Autonomous drones will be central to infrastructure inspections across the power industry by delivering faster and more precise assessments. Drones with high-resolution imaging, LiDAR [light detection and ranging] and thermal sensors can detect issues such as cracks, overheating and wear in power equipment and infrastructure before they escalate into costly failures. Edison International’s Southern California Edison uses drones to monitor 400,000 poles, transformers and lines in high-fire risk areas annually, significantly reducing inspection times and allowing frontline staff to focus on ignition risks. Autonomous drones will be particularly indispensable in the renewable energy sector for inspecting wind and solar farms, which can cover huge distances and be inconvenient to reach (ie offshore wind farms). AI-powered satellite inspections will supplement autonomous drone inspections by offering monitoring of infrastructure and environmental factors (such as vegetation encroachment) on a large scale. While autonomous drones provide detailed close-up diagnosis, AI-powered satellite inspections will focus on high-level surveillance, enabling a more complete assessment of critical assets.
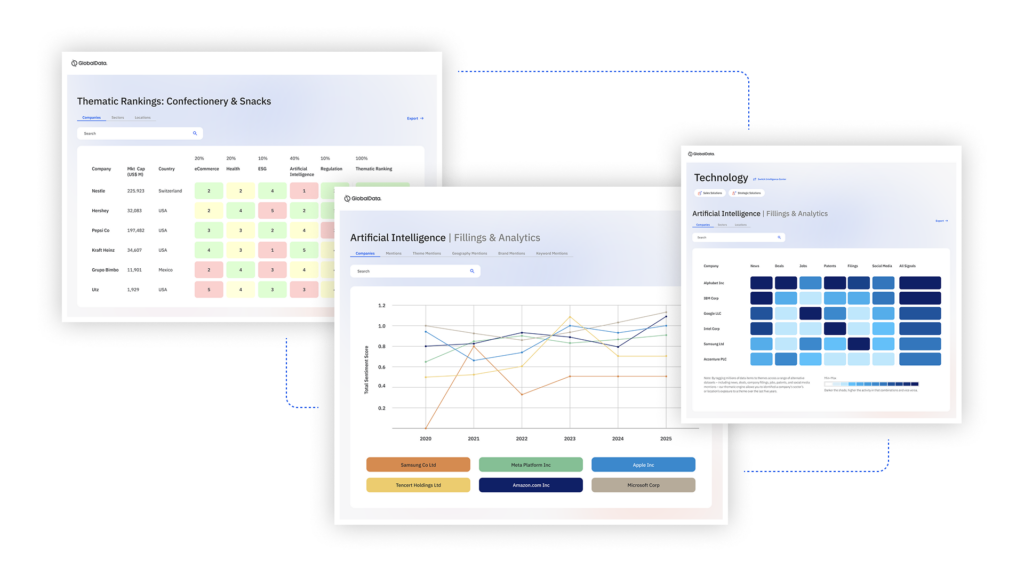
US Tariffs are shifting - will you react or anticipate?
Don’t let policy changes catch you off guard. Stay proactive with real-time data and expert analysis.
By GlobalData3D printing: a new frontier in equipment manufacturing
3D printing will make manufacturing across the power industry faster and more accurate. Automation can produce consistent parts at a high quality while minimising defects and reducing wastage. Power companies can use 3D printing to create custom replacement parts on demand, cutting lead times and limiting downtime when infrastructure needs repairing. EDF has a laboratory dedicated to robotic-enhanced 3D printing of large equipment components, which integrates a robotic arm and advanced motion control to improve flexibility and efficiency over traditional 3D printing processes. 3D printing will lower innovation costs by enabling relatively cheap and rapid prototyping of components such as advanced energy storage solutions and turbines, with successful designs offering potentially significant returns on investment.