
Centrifugal compressors operate by accelerating gases through an impeller and converting kinetic energy into pressure. Their applications span natural gas processing, petrochemical refining, and even hydrogen production. These systems are designed to handle high volumes, often under immense pressure and fluctuating temperatures, making reliability a critical factor of growing importance. Fortunately, there are multiple steps that OEMs can take to upgrade and improve the reliability and efficiency of their compressor designs, translating to better profitability for customers using them in the field.
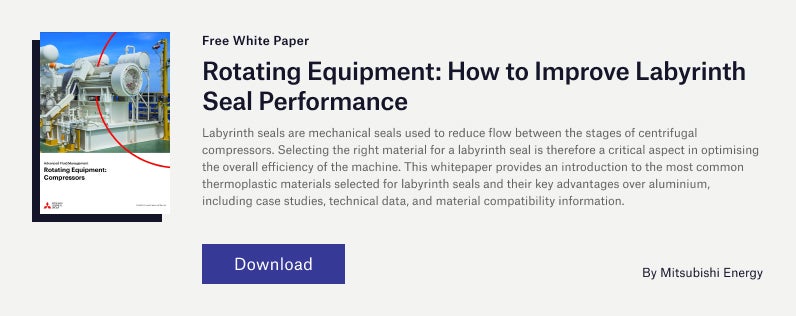
Well-optimised sealing systems are pivotal in maintaining the compressor’s efficiency. Located between various internal components of the centrifugal compressor, labyrinth seals are required to minimize process gas leakage. Historically, labyrinth seals have been made of metals such as aluminium, which offers the advantages of low cost and ease of manufacturing. However, metal’s limitations—such as susceptibility to deformation, wear, and chemical corrosion—have become increasingly apparent. These inefficiencies not only compromise performance but also lead to increased maintenance cycles and unplanned downtime. Even the most minor leakage can cost companies millions over the course of a compressor’s lifespan, significantly outweighing any upfront savings for low-cost components.
Benefits of polymer labyrinth seals
Labyrinth seals are a key component of centrifugal compressors, ensuring minimal leakage of process gases while maintaining operational integrity. Vibrations, thermal fluctuations, and chemical exposure often lead to deformation in conventional aluminium labyrinth seals, causing increased leakage and reducing overall efficiency.
According to Douglas Mahler, senior business development manager, energy segment at Mitsubishi Chemical Group: “Aluminium is only 100% as efficient as it can be after the first rotation.
“Aluminium labyrinth seals will mushroom and deform during contact between seal and shaft, therefore they won’t seal as designed against the rotor after contact was made. You’ll have increased leakage over time. Polymer labyrinth seals don’t have that issue because even though they are very rigid, it’s going to hit and then bend back, with minimal increase of the clearance between seal and shaft after contact was made. Except for some minor wear, you won’t lose the adequate sealing performance that polymer labyrinth seals offer after contact as you do with aluminum labyrinth seals.”
One of the standout features of polymer seals is their “memory” property, which allows them to return to their original shape after deflection. Unlike metal seals that sustain permanent damage after contact or due to thermal expansion, polymer seals maintain their structural integrity. This reduces the need for frequent replacements, ensuring longer service life and cost savings.
Beyond aluminium: advancements in material science
Mitsubishi Chemical Advanced Materials (MCAM) now offers advanced thermoplastics such as Duratron® PAI, Ketron® PEEK, Ketron® HT PEK, and Fluorosint PTFE, which are engineered to endure extreme conditions. These materials demonstrate superior performance in terms of heat resistance, chemical resistance, dimensional stability, and mechanical strength.
For example, Ketron® PEEK offers exceptional chemical resistance and can operate at temperatures up to 250°C (482°F), making it suitable for harsh environments. Similarly, Duratron® PAI provides high load-bearing capacity and remains dimensionally stable under thermal stress, outperforming metals in critical applications.
Another innovative development is the use of abradable polymer seals, such as Fluorosint 500, which allow for tighter clearances during operation. Unlike metal seals, these abradable materials wear in a controlled manner, creating a customised seal that maintains efficiency without damaging other compressor components. Fluorosint 500 has long been the industry standard for abradable polymer seals, allowing for superior sealing efficiency in certain applications as well as high resistance to temperature extremes, fuels, lubricants and chemicals.
Future trends and innovations
The evolution of compressor technology is far from over. Research into nanocomposites and hybrid materials aims to push the boundaries of what is achievable with polymers. Enhanced surface treatments and coatings are being developed to further improve wear resistance and reduce friction, making compressors even more efficient and reliable.
The integration of digital monitoring systems is another promising avenue. By equipping compressors with sensors that monitor seal performance and detect leaks in real time, operators can proactively address issues before they escalate, reducing unplanned downtime.
Optimising centrifugal compressor technology is not merely a technical upgrade but a strategic investment in efficiency, reliability, and sustainability. Polymer labyrinth seals and advancements in material science are paving the way for a new era of compressor performance. While the upfront costs may be higher, the long-term benefits—ranging from reduced emissions to operational savings—make these innovations indispensable in today’s energy landscape.
Mitsubishi Chemical Advanced Materials is a global leader in high-performance polymer solutions, providing cutting-edge materials for some of the world’s most demanding industries. With a legacy rooted in innovation, MCAM develops advanced engineering plastics that enhance efficiency, reliability, and sustainability across sectors such as energy, aerospace, and healthcare. Renowned for its expertise in custom polymer formulations, MCAM offers solutions tailored to specific industrial challenges, ensuring unmatched performance under extreme conditions. Committed to driving progress through collaboration and technology, MCAM is at the forefront of transforming industries with its pioneering materials and applications.
As the oil and gas industry continues to adapt to evolving demands, embracing these advanced technologies will be key to staying competitive and achieving a sustainable future. To find out more about the necessity of upgrading labyrinth seal materials from traditional aluminium to next-generation polymers, and how MCAM can optimise efficiencies on your project, download the whitepaper below.
Sources:
- John K Whalen, Eduardo Alvarez, Lester P Palliser. Thermoplastic Labyrinth Seals for Centrifugal Compressors.
- John S Stahley. Mechanical Upgrades to Improve Centrifugal Compressor Operation and Reliability.