
A team of materials scientists at Duke University in the US has developed a new laser evaporation technique to create new hybrid thin-film materials that could be used to make solar cells, light-emitting diodes and photodetectors.
The crystalline structure of hybrid thin-film perovskites materials makes it suitable for light-based applications.
Methylammonium lead iodide (MAPbI3) has the ability to convert light to energy and is the most common perovskite used in solar energy.
Duke University’s mechanical engineering and materials science professor David Mitzi said: “Methylammonium lead iodide has a very simple organic component, yet is a very high-performing light absorber.
“If we can find a new manufacturing approach that can build more complex molecular combinations, it will open new realms of chemistry for multifunctional materials.”
The new resonant infrared matrix-assisted pulsed laser evaporation (RIR-MAPLE) technique involves freezing a solution containing the molecular building blocks for the perovskite, before blasting the frozen block with a laser in a vacuum chamber.
How well do you really know your competitors?
Access the most comprehensive Company Profiles on the market, powered by GlobalData. Save hours of research. Gain competitive edge.
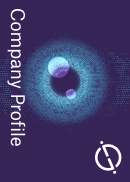
Thank you!
Your download email will arrive shortly
Not ready to buy yet? Download a free sample
We are confident about the unique quality of our Company Profiles. However, we want you to make the most beneficial decision for your business, so we offer a free sample that you can download by submitting the below form
By GlobalDataWhen a small piece of the frozen target is vaporised using a laser, the vapour travels upward in a plume that coats the bottom surface of an object hanging overhead, such as a component in a solar cell, according to the university scientists.
The product is then heated to crystallise the molecules and set the thin film in place.
Duke University electrical and computer engineering associate professor Adrienne Stiff-Roberts said: “The RIR-MAPLE technology is extremely gentle to the organic components of the material, much more so than other laser-based techniques.
“That also makes it much more efficient, requiring only a small fraction of the organic materials to reach the same final product.”