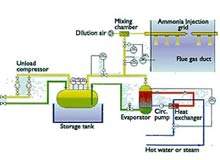
For the last five years in a row, coal has been the fastest-growing fossil fuel. It is also the most polluting. Combustion at the high temperatures found in power plants forms nitrogen oxides and, with increasingly strict limits, coal stations are finding it expensive to comply with environmental regulation.
Reducing NOx (NO and NO2) levels needs an integrated approach. Fluidised bed combustors or low-NOx burners with air staging have lower combustion temperatures so produce less NOx in the first place. However, the remaining combustion products still need to be reduced.
The most effective way of doing this is with selective catalytic reduction (SCR), which combines the flue gases with precise amounts of ammonia or urea over catalysts that speed the reduction of NOx into nitrogen and water.
During this method multiple layers are usually used to promote different reactions using active catalysts like vanadium, titanium and tungsten oxides as well as zeolites and activated carbon.
Titanium is often used for the structural component. Titanium honeycombs have a high surface area but flat plates generally have a higher resistance to deposition and erosion.
Key performance indicators include NOx removal efficiency, ammonia utilisation and ammonia slip. Those all depend on the ability of the control system to inject the exact amounts of ammonia across the cross-section of the flue gases being expelled. Performance must be maintained despite the decline of catalyst effectiveness over time. Catalysts are expensive and after the initial installation costs, replacement costs and lifetimes are the main economic drivers.
Balancing the ammonia supply
A major SCR concern is the release of unreacted ammonia (ammonia ‘slip’), which can cause larger problems than the NOx itself. Ammonia is typically injected through an array of nozzles over the entire flue gas duct. The ammonia injected must be proportional to the NOx mass flow rate.
That means measuring NOx concentrations, pressures and temperatures and estimating the gas flow rate (usually from the air flow rate to the boiler). Feed-forward control calculates the NOx flow rate to the reactor and so controls the ammonia flow proportionally. Trim-back control measures the NOx content after the reactor to adjust the ammonia flow rate.
The efficiency of the whole operation depends on accurate control. And in recent times software developments have helped this. The NOx mass flow rate varies across the duct’s cross-section, for example, and Hitachi, Alstom and others have improved modelling to increase accuracies.
A balanced (ideal) profile would have the same NOx:ammonia molar ratio at all cells in the SCR. For its APC2 software, Alstom simulated first principle process models, comparing the performance of the different control schemes, system configurations and operating modes.
The results enabled the company to fine tune the NOx removal efficiency targets, changes in the flue gas rate (load), changes to the NOx distribution profile and changes to the level of process noise on the inlet NOx. The modelling has also helped to reduce production of SO3 (a precursor of PM2.5 particulates), which can be another issue with SCR systems.
Other pollutants can also be captured. Hitachi has developed an SCR catalyst reaching above 95% oxidation of elemental mercury (Hg0) while keeping SO2 to SO3 conversion below 0.5%. The catalyst promises effective mercury treatment for high-sulphur bituminous coal-fired power plants.
Thorough gas mixing for efficiency
US company Babcock Power has increased its NOx removal efficiencies by thorough gas mixing. Babcock’s Delta WingMixer makes the gas homogeneous by mixing all the characteristics, including temperature, oxygen, dust, NOx, ammonia and SO3 concentrations.
This is particularly effective for non-uniform flow streams with, for example, out-of-service burners in boilers otherwise giving temperature and constituent concentration differences in the stream.
The Delta WingMixer allows gas mixing and reagent injection in one application, with no moving parts in the gas stream. That avoids much tuning during commissioning and annual maintenance. The system achieves homogeneity over the entire load range, allowing the Delta Wing system to consistently reach NOx reductions greater than 90%.
Babcock has also developed systems for flue gases with high levels of catalyst poisons like arsenic. These poisons can seriously degrade performance, as can fly ash.
Estimating catalyst degradation
The best temperature for catalysis is usually between 300 and 400°C, so systems are normally fitted at the economiser outlet. That often means a “high dust” location before the particle collection system, but catalyst performance is greatly affected by dust components. Over time, the catalyst degrades and its surface can become clogged with fly ash.
Although catalysts themselves are expensive, failing to replace an ineffective catalyst can have huge cost effects: operators can be forced to reduce plant output or buy emissions credits. Maintenance can restore SCR performance by adding a fresh layer, but since different catalysts degrade at different rates, maintenance has to be done per layer. With all the incidental costs, a five-day unit outage for SCR work could cost more than $1m for a 500MW unit.
Checking the catalyst conventionally therefore means waiting for a generating outage to take a sample for analysis in a laboratory. For the many plants with year-round operation this becomes difficult. Catalyst-activity testing tools are now helping to predict remaining catalyst life, and consequently maintenance timings.
Fossil Energy Research Corp (FERCo) in the US has a system called KNOxcheck which takes samples of the catalyst during operation. The system allows remote equipment monitoring and calibration across the web. Tests at Southern Company’s Gorgas plant showed similar results to laboratory testing, promising appreciable cost savings for reducing NOx and other pollutants.
Combined systems: the solution?
Coal power stations also produce large amounts of SO2. This usually needs to be removed from the flue gases by fuel gas desulphurisation. Combined SO2/NOx removal systems are complex and costly but prices are dropping for low-to-medium-sulphur coal-fired power stations. Systems are also in development for high-sulphur plants.
SCR is still hugely expensive, particularly for retrofitting since it can need thousands of kilograms of steelwork to hold the large, expensive and delicate catalysts. Much research therefore looks at catalyst-free systems.
The most promising systems seem to be combinations of efficient and precisely controlled low-NOx burners with fuel reburning and overfire air. But even these don’t come close to the 80–90% removal efficiencies of SCR – a technology set to rise in use, given today’s pressing environmental concerns.