
Computer-aided design (CAD) and 3D modelling is not a new concept in the design-build industry, but using advanced software in the design stages to save time, money and labour has become increasingly essential when planning new power plants. When dealing with such complex infrastructure and minute calculations, the precision of these tools can bring benefits to many aspects of a new power project.
ESI of Tennessee, US, used design and engineering software on a recent contract for the US Department of Energy. The department contracted the company to design and engineer a new biomass cogeneration facility to replace an inadequate coal powerhouse in Aiken, South Carolina. According to estimates, the new facility will save $35 million a year in energy, operation and maintenance costs and remove approximately 100,000t of greenhouses gases from the atmosphere.
Power-Technology caught up with Demetrius Franklin, CAD manager at ESI, who has over 20 years of experience in the field, to talk about the design process for the facility and the benefits of utilising 3D design software for a large-scale power project.
Could you give some background on the biomass project in South Carolina and ESI’s role?
This biomass project was initiated by the Department of Energy, which was looking into doing a large biomass facility in Aiken, South Carolina. It was replacing some coal boilers out there with biomass ones. It had contracted Ameresco to put the boiler in.
Ameresco was looking for a company that specialises in biomass technology, which ESI does, and which could coordinate the engineering efforts with other parts of the project. That’s how we got involved. Prior to my arrival at ESI, the company had worked with Ameresco on another project, so there was confidence we could coordinate this effort.
What is the status of the project at the moment?
The project is under construction. They have both the boilers installed. There’s quite a bit of construction done and a lot of the underground piping has been run as well. They’re probably about 20% into the project.
How well do you really know your competitors?
Access the most comprehensive Company Profiles on the market, powered by GlobalData. Save hours of research. Gain competitive edge.
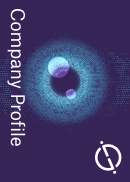
Thank you!
Your download email will arrive shortly
Not ready to buy yet? Download a free sample
We are confident about the unique quality of our Company Profiles. However, we want you to make the most beneficial decision for your business, so we offer a free sample that you can download by submitting the below form
By GlobalDataWhat are the advantages of using 3D simulation and modelling in power plant design?
I think a huge benefit is the interference detection. On this project, we have to coordinate a lot. For example, the two boilers came from one vendor, the turbine came from another and a lot of the water treatment equipment came from another vendor. They were all using different CAD packages. In the past, when it was a 2D only environment, we had to get all the different drawings, print off a lot of paper and have meetings for a few weeks, trying to visualise all these different components together.
When you have a 3D model, it is everything. So it enables you to make decisions really fast. It cuts out misinterpretations, because with 2D you can give those drawings to six different people who might have six different interpretations. The 2D drawings aren’t going to have everything in them. You might see a plan view, but it may only show you 5-6ft-worth of space. It’s the same thing with a section view. But with a 3D model, it’s every nut and bolt. It puts everything out there, immediately. On a large project, I wouldn’t really want to do it any other way.
So, interference detection is one huge benefit, because each vendor is mostly concerned about their piece of the pie, but as the engineers are overseeing everything, we’re concerned with all the pieces. It’s kind of funny, because even with the boiler manufacturer, we were able to identify interferences with their parts.
From a design perspective, what are the differences between 2D drawings and 3D modelling?
From a design perspective, a problem with 2D is you have to do a lot more work. For example, if I get a set of vendor drawings and I’m modelling a water treatment building, I’m running that but I’m going to make some assumptions about other components that are in there, like forklift assets and removing motors. In the 2D world, I’m limited to making a lot of educated guesses on my spacing. In a 3D model, once I get all the equipment routed, I can take a forklift and animate it through the whole plant and identify where the problem areas are.
What software did you use for designing the biomass project?
On this particular project, we used several products from Bentley. We used Bentley AutoPlant; that is the software we used to run all of our piping. We also used the program to extract our isometric programs. From there we were able to export files from the model that the engineers could import into Bentley AutoPipe.
Another feature we used was the Bentley Equipment Modeller. On this project we used Bentley equipment and manually modelled things for some of the more detailed equipment, but we went with Bentley Equipment so we could match our pipes up to it and get the bolts and gas and everything else. We used Bentley P&ID on the project so all the pipelines have intelligence to them so we can automatically kick out equipment lists, line lists, valve lists and so on.
We also used Pro-Structure, along with Staad. We used these programs to do all the steel design, steel analysis and modelling. We used Data Manager, which is a program that allows you to connect all the Bentley software, so that’s where we managed the data.
You’ve got the engineers, the designers, the project managers and the client. Using all the components makes sure that everybody is responsible for a particular thing, so I fixed the software to the point that everybody could do that.
Does this technology have a lot of potential when it comes to designing power plants in a cost-effective way?
In my experience, when I first started everything was on the board, everything was hand-drawn. So you had to know how to draw to get a job, whereas today, with all this computer technology, somebody can come in and be thrown into a project. So they don’t have a lot of foresight to see this stuff, but the 3D model helps our newer engineers to visualise the project, which helps them be more productive a lot more quickly.
Can 3D simulation help to analyse processes and future scenarios for a project?
It can and we do a lot of that here. You have to complete the project and put it together, but we try to pre-plan for future scenarios, whether it’s putting some pumps in or anything else. We have to ask how we’re going to get the materials in, what kind of crane we’re going to use. So we actually have a model of a crane and simulate it, laying it out for ourselves and for the client so they’ll be comfortable. It shows that we’ve thought it through. So we’ve pre-planned, we know what kind of equipment we’re going to use, we’ve modelled it, and we even simulate pulling the old equipment out and bringing the new equipment in. We go through the whole scenario.
What do you think could be incorporated into 3D simulation technology in the future?
We do something unique at our company: we use our 3D model as a document management tool. For example, when my field guy has the 3D model, I try to fix it so that everything is encased within it. When he’s walking through the 3D model and he comes to a particular water pump, a little tag will pop up, giving him the equipment name and number, and he can also click on it and it will bring up the drawing right there for him. He doesn’t have to have a stack of drawings in the construction trailer, coming back and forth; everything is right there in the model.
I think if the program could have more attributes added to it for the field contractor, I think that would be awesome, because another thing about 3D is that the model can be updated every day.
Every user has a viewer on their computer and they can look at and review the model just like the project managers. I think that’s something that could be added for the field contractors to make their jobs a little bit easier.
Something they request is the ability to take the model, even though they’re not experts in AutoCAD or Bentley, and manipulate it in the field. That would be very beneficial – then they could send the information back to us and we could make the official changes and send the model back to them.