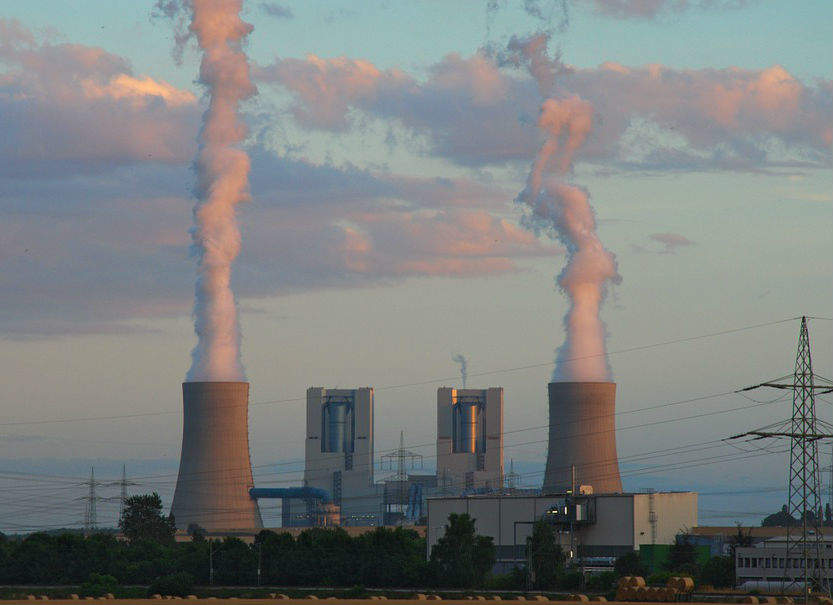
In January, US President Barack Obama mounted the latest offensive in what Republicans have dubbed his ‘war on coal’ by halting new coal mining leases on federal land, home to roughly 40% of US coal reserves.
Yet, despite protests from ‘big coal’, the decision will have little impact on production of the fossil fuel in the short to medium-term. Companies can continue to mine reserves under lease, estimated at enough to sustain current levels of coal production from public land for 20 years.
“Even as our nation transitions to cleaner energy sources…we know that coal will continue to be an important domestic energy source in the years ahead,” states Interior Secretary Sally Jewell, proof that while the West’s love affair with coal may be on the wane thanks to tough emissions standards, cheap natural gas and slowing global demand, its reliance on the fossil fuel is most certainly not.
Global demand for coal is projected to increase 15% by 2040, yet burning it releases almost 14 billion tonnes of carbon dioxide into the atmosphere every year, the majority from power generation.
“Do you realise we’ve got 250 years of coal?” Obama’s predecessor George W Bush said at the outset of his second term in office in 2005. “Coal has got environmental hazards to it, but I’m convinced technology can be developed so we can have zero-emissions coal-fired electricity plants.”
Ten years on, is this aspiration any nearer to becoming a reality, and how are modern power plant designers using structures and systems to maximise operational efficiency and reduce emissions?
Steaming ahead: ultra-supercritical boiler, turbine and generator design
At the heart of coal-fired electricity generation lies the steam cycle. Typically, pulverised coal is fed into a giant industrial furnace surrounded by boiler tubes filled with water. The burning coal heats the water to create steam, which is transferred at high-pressure to turbines linked to a generator.
As the generator spins, electrons are generated that are stepped up in voltage by transformers, while the turbine steam is condensed back into water and returned to the boiler for reheating.
In ultra-supercritical steam (USC) power plants, the extreme boiler temperature and pressure heat the water so that it becomes a ‘supercritical’ fluid that exhibits properties of liquid and gas phases.
In this state, supercritical steam is much more efficient at driving the giant turbines that spin the plant’s generators. The upfront cost of such technology is 20%−30% more expensive than a traditional subcritical unit, but that is offset by improved net thermal efficiency levels and reduced emissions.
High-efficiency low-emissions (HELE) solutions are proven to reduce both emissions and fuel costs by maximising the amount of power from the steam produced, yet the International Energy Agency (IEA) reports that in 2011 around 75% of coal-fired units worldwide employed non-HELE technology.
The situation had barely improved three years later when an IEA study into coal-fired power plant design in China found that the global average efficiency of coal-fired power plants in operation was around 33%, significantly lower than the 45% possible using modern, ultra-supercritical technology.
Progress is undoubtedly being made, however. General Electric (GE) is pioneering ultra-supercritical technology at the RDK 8 coal-fired power plant in Karlsruhe, Germany with considerable success.
Operated by German utility EnBW, the plant achieves 47.5% net thermal efficiency while producing 912MW of electricity, making it one of the world’s most efficient hard coal-fired steam power plants.
Role models: cutting-edge power generation in Denmark and Japan
Nordjylland power station located in Northern Jutland, Denmark is touted by its owner Vattenfall as holding the world record for most efficient coal utilisation since Unit 3 was commissioned in 1998.
The 400MW, USC Unit 3 employs a 70m-high, once-through steam generator plus a double-reheat steam cycle and cold seawater for cooling, resulting in a net electrical efficiency of 47% (LHV basis). Its dual-use design allows it to use up to 91% of the energy content in the bituminous coals it burns.
The Isogo thermal power station near Yokohama, Japan houses two coal-fired units. Unit 2 operates at 600°/620°C reheat, achieving 45% efficiency while Unit 1 operates at a slightly lower temperature.
Combined, the facilities emit 50% less sulphur, 80% less nitrogen, 70% less particulate and 17% less carbon dioxide than the previous subcritical units using a regenerative activated coke dry-type control technology (ReACT) that captures multiple pollutants, while only using 1% of the water of conventional systems.
A 2015 report published in the coal industry journal Cornerstone cites Isogo as the world’s cleanest coal-fired power plant in terms of emissions intensity. The two units more than doubled the power generated at the site while lowering emissions to that of a natural gas-fired combined-cycle facility.
New frontiers: China and advanced ultra-supercritical technology
In South East Asia where energy demand is projected to spike by 80%, coal will likely be the single largest energy source. In the first nine months of last year alone, Chinese state-owned companies received initial or full approval to build 155 new coal power plants with a total capacity of 123GW.
The aforementioned 2014 IEA study, ‘Emissions Reduction through Upgrade of Coal-Fired Power Plants’, evaluated the efficiencies of two operational units in China’s Shandong and Jilin provinces.
In addition to guidance on retrofitting new technology to existing facilities, the report issued advice on improving efficiencies at the design phase − where there exists a reasonable degree of flexibility − using supercritical steam conditions, the inclusion of a second reheat stage on the steam turbine, and a reduction in condenser pressure, excess air ratio and in the stack gas exit temperature.
According to GE, a prime mover in air quality control systems (AQCS) in existing power plants, moving the average global efficiency rate of coal-fired power plants from 33% to 40% by deploying advanced solutions such as ultra-supercritical technology would cut annual CO2 emissions by two gigatonnes and contribute to containing the global warming within the 2°C scenario specified by the IEA.
GE is already looking into what happens when you bring steam temperatures up to 1,300°F (700°C) − advanced ultra-supercritical technology (AUSC) − which could achieve coal-fired efficiencies as high as 50%. Such high pressures and temperatures will require power plant designers to employ more advanced nickel or nickel-iron super-alloys, as well as overcome fabrication and welding challenges.
In 2014, Alstom and Southern Company announced a milestone in the development of AUSC, with steam loop temperatures maintained at 760°C for 17,000 hours at Plant Barry Unit 4 in Alabama, US.
By pushing the boundaries of power plant design in this manner, the fossil fuel industry will ensure that clean coal continues to play a pivotal role in the global energy mix to mid-century and beyond.