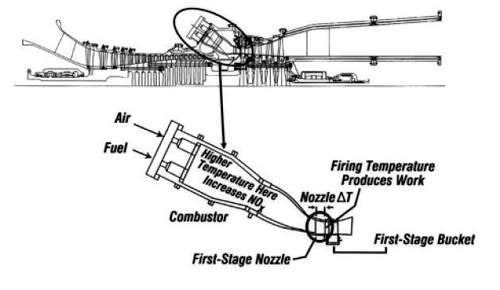
With its latest combined-cycle gas turbine, GE has become the first company to reach the 60% efficiency landmark. To achieve this, firing temperatures were raised to 1,430°C.
The 60% efficiency figure comes with single-digit parts-per-million NOx emissions – a particular challenge because it is a conflicting design goal. Higher efficiency needs higher working fluid temperatures; but temperatures of 1,540ºC reach a threshold of thermal NOx formation.
GE developed the H-Series as part of the US Department of Energy’s advanced turbine system (ATS) programme. General Electric Power Systems (GEPS) was one of two turbine manufacturers (the other was Siemens Westinghouse Power Corporation) partnering with DOE to extend the DOE’s advanced turbine system programme into the utility sector.
GE’s resultant 7H technology (a 400MW, 60Hz combined-cycle system) was converted to the 9H (480MW, 50Hz) system for overseas markets. For both systems, a dry low-NOx combustion system mixes fuel and air before ignition to help reduce emissions as low as 25 parts per million (ppm). The turbine’s first-stage buckets and nozzles use single-crystal materials to withstand the higher temperatures.
An innovative closed-cycle steam cooling system keeps combustion temperatures and hence NOx emissions
relatively low.
With even a 1% efficiency increase substantially reducing operating costs over the life of a typical power plant, GE estimates savings of $2m a year over today’s most efficient (57%-58%) combined-cycle plants.
Despite the innovative technology, the H-Series retains much of previous turbine design. The major units are a burner, the gas turbine itself, and a compressor that compresses the intake combustion air. As with other combined-cycle plant, waste heat in the hot turbine exhaust gases drives a boiler or heat recovery steam generator (HRSG). The resulting steam is passed through a steam turbine to generate extra electrical power.
HIGH BURNER FIRING TEMPERATURE
The temperatures and pressures needed to drive a turbine are normally generated by burning fuel in air. Performance of the gas turbine is primarily determined by the burner firing temperature (temperature into the first rotating turbine stage). Increases in firing temperature raise both specific output (kW per kg of air passing through the turbine) and fuel efficiency (fuel consumption per kW of output).
GE has used aircraft engine materials and cooling techniques to steadily increase firing temperatures over the years. The H-Series turbines raise them a further 110°C over the company’s F-series turbines, while holding NOx emission levels steady.
The H-Series can-annular burner is a lean pre-mix DLN-2.5 (dry low-NOx), similar to GE’s FA-class DLN systems. Fuel flexibility is good, with single-digit parts per million NOx and CO emissions. 12 combustion chambers are used on the 7H, and 14 on the 9H.
The fuel injector uses a ‘swozzle’ (swirler nozzle). The premixing passage of the swozzle uses swirl vanes to rotate the admitted airflow, and each of these swirl vanes also contains passages for injecting fuel into the premixer airflow. The premixer is very aerodynamic and highly resistant to flashback and flameholding.
H-Series mixes fuel and air before ignition to help reduce emissions.”
Downstream of the swozzle vanes, the outer wall of the premixer is integral to the fuel injector to provide added flameholding resistance. Finally, a swirl cup in the centre of each fuel injector aids diffusion flame starting and low load operation.
There are only three combustion modes: diffusion, piloted premix and full premix. These require four fuel circuits: centre nozzle premixed fuel, outer nozzle premixed fuel, burner quaternary premixed fuel and diffusion fuel. The gas turbine is started on diffusion fuel, accelerated to full-speed no-load (FSNL), and then loaded further. At about 20%-35% gas turbine load, the centre and outer nozzle premixed fuel streams are activated in the transfer to piloted premix.
When the gas turbine is at about 40%-50% load, the turbine is transferred to full premix mode and all diffusion fuel flow is stopped while the burner quaternary fuel flow is activated. This very simplified staging strategy has major advantages for smooth unit operability and robustness.
FOUR GAS TURBINE STAGES
To capture the energy in the gas stream, the stream is directed by vanes at the base of combustor nozzles to hit the turbine blades (airfoils). The curved blades redirect the gas stream, converting the forward momentum of the gas into rotary motion to produce the power.
A series of turbine blade stages is attached to a rotor / shaft assembly. The shaft rotation drives an electric generator and a compressor to force the air into the gas turbine combustor.
Combined-cycle designs are increasingly using a single-shaft configuration, where the gas and steam turbines are on either side of a common generator. This reduces capital costs, operating complexity and space requirements. The plant footprint is also reduced with plants, like the H-Series, which have high specific output.
23:1 COMPRESSOR PRESSURE RATIO
GE used the high-pressure compressor design from its CF6-80C2 aircraft engine. The four turbine stages are prompted by the use of a 23:1 compressor-pressure ratio. This is a major change from the earlier ‘F’ class gas turbines with their 15:1 ratio and three turbine stages. The higher pressure ratio needs the extra stage to prevent stage loading from reducing efficiencies. The 23:1 ratio also allows the last-stage gas turbine bucket to be uncooled.
The compressor allows 558kg/s and 685kg/s airflow for the 7H and 9H gas turbines respectively. In addition to the variable inlet guide vane (IGV) used on previous GE gas turbines to modulate airflow, the H-Series compressors have variable stator vanes (VSV) at the front of the compressor. They are used, together with the IGV, to control compressor airflow during turndown, as well as to optimise operation for variations in ambient temperature.
H-Series compressors also circulate cooled discharge air in the rotor shaft to regulate temperature and allow the use of steel instead of Inconel. To allow a reduction in compressor airfoil tip clearance, the design included a dedicated ventilation system around the gas turbine.
CLOSED-LOOP STEAM COOLING
Gas turbines produce high-quality waste heat that can generate steam for combined-cycle and CHP (combined heat and power) applications, significantly enhancing efficiency. Combined cycle is the usual choice by utilities because the gas turbine exhaust can produce steam that can power a steam turbine to generate extra electricity. Around 75% of all gas turbines are now used in combined-cycle plants.
Conventional for gas turbines is open-loop air cooling, which diverts a significant amount of air from the compressor into the working fluid. This unfortunately introduces a significant temperature drop (around 150ºC) across the first stage nozzles, which reduces firing temperature. It also loses compressed air energy into the hot gas path. A major design aim for the H-Series was to cool the nozzles while minimising the temperature decrease in combustion product as it passes
through.
Closed-loop steam improves cooling and efficiency because steam has better heat transfer characteristics than air, and retains heat in the closed loop. The coolant reduces the temperature decrease to below 44°C. This results in a firing temperature of 1,430°C with no increase in combustion temperature and resulting emissions (the firing temperature must not exceed the NOx formation combustion temperature of 1,540ºC).
Closed-loop steam cooling is used on the nozzle and turbine blades (buckets) of the turbine’s first two stages, air cooling on the third stage, while the fourth (last) stage is uncooled. Closed-loop cooling eliminates the film cooling on the gas path side of the airfoil, and increases the temperature gradients through the airfoil walls. This method of cooling however causes higher thermal stresses on the airfoil materials, and has led GE to use single-crystal nickel super-alloys for the
first stage, with thin ceramic thermal barrier coatings (TBCs).
Single-crystal fabrication eliminates grain boundaries in the alloy, and improves thermal fatigue and creep characteristics. However, single-crystal material characteristics contribute to the difficulty in airfoil manufacture, and were previously limited to relatively small hot-section parts. The thermal barrier coatings insulate and protect the metal substrate from combustion gases. A ceramic TBC topcoat provides thermal resistance, and a metal bond coat provides oxidation resistance and
bonds the topcoat to the substrate.
The heat transfer system integrates cooling both of gas turbine bucket / nozzle and steam plant reheat process. Using heat from the steam coolant in the steam turbine makes what was traditionally waste heat into usable output. Closed-loop cooling also minimises parasitic extraction of compressor discharge air, increasing flow to the head-end of the combustor for fuel premixing. Using steam enhances cycle efficiency by up to 2% and significantly increases gas turbine output.
THREE-PRESSURE-LEVEL HRSG
Besides the gas turbine, the H-Series has a three-pressure-level HRSG and a reheat steam turbine. The high-pressure steam from the HRSG is expanded through the steam turbine’s high-pressure section. The exhaust steam from this turbine section is then split. One part is returned to the HRSG for reheating; the other is combined with intermediate-pressure (IP) steam and used for cooling in the gas turbine.
The H-Series machines are ‘bottoming cycle’ types. ‘Topping cycle’ systems use the gas turbine to generate electricity, with the exhaust gas generating steam (or hot water), ‘bottoming cycle’ systems use this steam to produce more electricity. The output and efficiency of the bottoming cycle is a function of the gas turbine exhaust temperature.
For a given firing temperature, the turbine exhaust temperature is largely determined by the work required to drive the compressor. That is, in turn, affected by the compressor pressure ratio.
WORKING AS A SYSTEM
The burner, compressor and gas turbine must operate as a system, particularly at the design point (baseload), part load turndown conditions and no load. The power plant and all power island components must also operate efficiently at steady state and under transient conditions, from start-up and purge, to full speed.
To manage all the various sub-systems, the H-Series incorporates an integrated control system (ICS). This manages steam flows between the HRSG, steam turbine and gas turbine. It also schedules the distribution of cooling steam to the gas turbine.
The H-Series uses digital control – the Mark VI system. A pyrometer system rapidly detects rises in temperature, enabling automatic turbine shutdown before damage occurs.
The success of the Mark VI has prompted GE to incorporate it into other (non-steam-cooled) engines.
GE DESIGN, MANUFACTURING AND TEST CHALLENGES
Because ATS goals required advances in virtually all components of the gas turbine, GE used a new systems approach for the H-Series – the ‘design for six sigma’ (DFSS) process.
DFSS accelerated development by improving up-front definition of performance requirements and specifications for subsystems and components, and by focusing the research and development activities. Despite the turbine’s higher operating temperatures the start-up times, maintenance intervals, and turndowns are all similar to GE’s F-product line.
GE used improved 3D computational fluid dynamic (CFD) tools to redesign the compressor flow path. Full-scale evaluation of the 7H compressor at GE’s Lynn, Massachusetts compressor test facility validated both the CFD model and the compressor performance. The turbines were exhaustively tested, with more than 7,000 sensors placed around the equipment.
H-Series has a three-pressure-level HRSG and a reheat steam turbine.”
The transition from manufacturing 25cm 1kg aircraft blades to those two to three times longer and ten times heavier represented a significant challenge. Adding to the challenge is the need to maintain very tight airfoil wall thickness tolerances for cooling, and airfoil contours for aerodynamics.
GE developed non-destructive evaluation techniques to verify production quality of single-crystal ATS airfoils, as well as the directionally solidified blades used in stages three and four.
Ultrasonic, infrared, and digital radiography X-ray inspection techniques helped the work. An e-beam test facility replicated turbine blade surface temperatures and thermal gradients to validate the process.
The initial commercial units were the MS9001H (9H) and MS7001H (7H). The 9H preceded the 7H into commercial service, with the MS9001H leading to the development of the Baglan Energy Park in South Wales, United Kingdom. It was then the world’s largest gas turbine at 12m long, 5m in diameter, and weighing 370t. It is rated to generate 480MW of electricity in combined cycle operation. The MS7001H was the basis for Sithe Energies’ 800MW Heritage Station in Scriba, New York.
SYSTEM INTEGRATION IS THE KEY
The H-Series shows the benefits of integrated design, and this should not stop with the turbines alone. It was taken a step further at the Baglan Bay, which is a model for modern, efficient gas-fueled plants. Besides supplying electricity to the national grid, the plant provides electricity and steam to the adjacent Baglan Energy Park and BP Chemical’s isopropanol plant.
The plant shows that, even in the most efficient turbines, there is plenty of useful ‘low-grade’ waste heat.
With fuel being the single largest cost of running a power plant, GE remarks that even a 1% gain in thermal efficiency can mean as much as a $15m to $20m saving over the life of a plant the size of Baglan Bay.
That gives an idea of the energy waste from the many conventional power stations that work at below 40% efficiency.
Such waste is no longer acceptable in a world of dwindling fossil fuels. Energy is a precious resource, and we should be making the best possible use of it. Turbines like GE’s H-Series save huge amounts of money while doing it.